-
- News
- Books
Featured Books
- pcb007 Magazine
Latest Issues
Current IssueInventing the Future with SEL
Two years after launching its state-of-the-art PCB facility, SEL shares lessons in vision, execution, and innovation, plus insights from industry icons and technology leaders shaping the future of PCB fabrication.
Sales: From Pitch to PO
From the first cold call to finally receiving that first purchase order, the July PCB007 Magazine breaks down some critical parts of the sales stack. To up your sales game, read on!
The Hole Truth: Via Integrity in an HDI World
From the drilled hole to registration across multiple sequential lamination cycles, to the quality of your copper plating, via reliability in an HDI world is becoming an ever-greater challenge. This month we look at “The Hole Truth,” from creating the “perfect” via to how you can assure via quality and reliability, the first time, every time.
- Articles
- Columns
- Links
- Media kit
||| MENU - pcb007 Magazine
Estimated reading time: 5 minutes
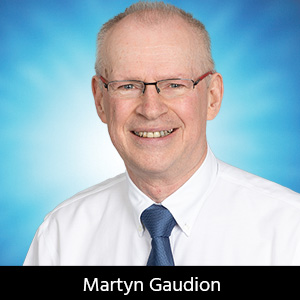
The Pulse: Rough Roughness Reasoning
Reliable bonding reduces the risk of delamination through thermal stresses. The tried-and-tested way of achieving a good, reliable bond is to ensure that the copper is sufficiently rough to promote adhesion to the epoxy resin in the prepreg material. As materials and bonding technology improves, the copper surfaces can be made increasingly flatter and still achieve the desired reliability. In the future, new bonding methods—some already here but still on the high-priced side of the equation— may allow extremely flat copper to bond reliably. Meanwhile, as the industry is heading down the road of “smoother” copper, there is still a need to model the effects of a rough surface on signal transmission.
Models and Methods
There are four or five primary methods for modelling signal losses owing to roughness, depending on how you interpret them. Hammerstad and Groisse are legacy methods, but still valid at the low GHz range. Hammerstad was developed around World War II to calculate the losses caused by machining grooves in early radar systems. Groisse extends the frequency capability a little higher. But if you are pushing into the high GHz, then these legacy models soon start to saturate, and they will both under-predict the contribution that surface roughness makes to loss. Newer methods (of the last decade or two) perform to much higher frequencies and correlate well with measurement systems.
Huray modelling describes the dendritic surface of the copper as small pyramids of copper balls. Using a scanning electron microscope (SEM), the SI engineer can enter the ball count, area, and number of balls in area to prime the Huray model. If this seems a little tedious and only for academics with time on their hands, there is a welcome answer. Bert Simonovich of Lamsim Enterprises has a paper which describes a preprocessor which takes the matte and drum side’s Rz roughness measurement and, as if by magic, generates a set of Huray parameters. This saves us a lot of time and effort with analysing SEM images.
The second relatively recent method for modelling is the gradient method. Its authors propose that rather than model the detail of the surface, that the interface between the copper and the dielectric be treated as a gradient where the characteristics blend from pure conductor to pure dielectric over the RMS (Rq) roughness of the surface. Papers on the gradient method propose that not only does this model help the effects of roughness on loss but also takes quite good care of the effects of roughness on phase.
Are You a Snowball or a Ski Slope?
The two modern methods take a different approach to roughness modelling with Huray comparing and modelling the surface topology as small stacks of snowballs (further simplified by Bert Simonovich with his Cannonball Huray method). The gradient method offers a “ski slope” down from the pure conductivity of copper, through a blended zone of decreasing conductivity, until the rough surface ends in pure dielectric material. Huray takes data analysed from an SEM to model the roughness. The Cannonball method uses commonly available Rz roughness data, and the gradient method uses RMS (Rq) roughness data.
Roughness Not Just a Number
RMS Rq Rz Rz (ISO), Rz(DIN), Rz(JIS), and a myriad other roughness metrics reveal a minefield of complexity to the SI engineer who may just ask, “How many microns of Cu is the roughness on this foil?” What is important is that the methods mentioned are modelled using specific roughness metrology, and there is no trustworthy conversion from one to the other. You may find some articles that say something like, “In a limited number of circumstances a conversion is possible,” but it is prone to error and pitfalls. So, the bottom line is to use the gradient method; you need to use RMS (sometimes called Rq) roughness. For the Cannonball Huray, use Rz (DIN or JIS). There is good reason for the variety, as in mechanical engineering you may be looking at a certain roughness to hold lubricant on a bearing or cylinder surface, or the measurement may simply be one of process control.
The OEM Rules
Regardless of the method you would like to use, or you feel is best for your application, if an OEM is specifying a particular model then you had best stick to that. It’s fine to compare with other methods, but for product qualification, if the OEM is using roughness model “A,” then that’s the choice made for you.
Future Directions
You may have noticed earlier in the article that with improvements in resin systems and copper surface pretreatments, that profiles are getting smoother. Over time (and we are not there yet), the need for roughness modelling will ease.
A Little Knowledge is…
…a dangerous thing, as the saying goes. Whilst roughness data may be readily available from your foil or laminate supplier, remember that depending on where the material is in the stack, it is likely to undergo further treatment or plating on drill end layers. Not only do you need to have material data, but also stackup information on how the fabricator further treats it before bonding is valuable to form a complete picture.
Conclusion
Whilst at first sight roughness modelling may seem fearsomely complex, roughness is only part of the loss budget. Getting a reasonable figure in for roughness and choosing the correct model will enhance your prediction of insertion loss compared with solvers that simply model smooth surfaces.
Resources
- "A Physical Surface Roughness Model and Its Applications," by G. Gold and K. Helmreich, IEEE Transactions on Microwave Theory and Techniques, vol. 65, no. 10, pp. 3720-3732, October. 2017.
- "Fundamentals of a 3-D ‘snowball’ model for surface roughness power losses," P. G. Huray et al., in IEEE Electromagnetic Compatibility Magazine, vol. 9, no. 2, pp. 62-65, 2nd Quarter 2020.
- Bert Simonovich’s Design Notes: “Cannonball Huray model demystified,” Lamsim Enterprises.
- Surface roughness comparison of Gradient and other methods: Polar Instruments Ltd. Click here.
Martyn?Gaudion?is managing director of Polar Instruments Ltd. To read past columns or contact?Gaudion,?click here. ?Martyn is the author of The Printed Circuit Designer’s Guide to… Secrets of High-Speed PCBs, Part 1andPart 2. You can view other titles in the I-007e library here.
This column originally appeared in the July 2023 issue of Design007 Magazine.
More Columns from The Pulse
The Pulse: Design Constraints for the Next GenerationThe Pulse: Ultra Upgrade Unknowns—What’s Coming for UHDI?
The Pulse: Commonsense Cost Cutting
The Pulse: Overconstraining: Short, Slim, and Smooth
The Pulse: Drilling Down on Documentation
The Pulse: New Designer’s (Partial) Guide to Fabrication
The Pulse: Simplest Stackups Specified
The Pulse: Industry Organizations Keep Knowledge Alive