-
-
News
News Highlights
- Books
Featured Books
- pcb007 Magazine
Latest Issues
Current IssueSales: From Pitch to PO
From the first cold call to finally receiving that first purchase order, the July PCB007 Magazine breaks down some critical parts of the sales stack. To up your sales game, read on!
The Hole Truth: Via Integrity in an HDI World
From the drilled hole to registration across multiple sequential lamination cycles, to the quality of your copper plating, via reliability in an HDI world is becoming an ever-greater challenge. This month we look at “The Hole Truth,” from creating the “perfect” via to how you can assure via quality and reliability, the first time, every time.
In Pursuit of Perfection: Defect Reduction
For bare PCB board fabrication, defect reduction is a critical aspect of a company's bottom line profitability. In this issue, we examine how imaging, etching, and plating processes can provide information and insight into reducing defects and increasing yields.
- Articles
- Columns
- Links
- Media kit
||| MENU - pcb007 Magazine
Estimated reading time: 5 minutes
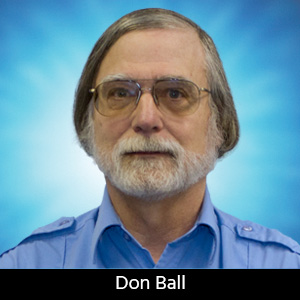
The Chemical Connection: Reducing Etch System Water Usage, Part 2
In my last column, I reviewed some relatively simple ways to reduce water usage in existing etch systems: cutting down cooling coil water flow, adding chillers to replace plant water for cooling, lowering flow rate nozzles for rinses, etc. This month, I’ll continue with more ways to control water usage in your etcher. Most of these are not easily retrofittable to existing equipment but should be given serious consideration when new equipment is contemplated. With the right combination of add-ons, it is possible to bring the amount of water used in an etch system to almost zero.
One of the best ways to reduce rinse water volume is the use of counter-current cascade rinses in place of single rinses to drain. This technology has been around for a long time and consists of several short stages, each with its own sump (usually nine to 10 gallons each), pump, and a single spray tube. Water is fed to the last stage, which then overflows into the preceding stage and so on down the line to the first stage immediately after the etcher. In this way, the water is used (n)times, with n being the number of stages in the rinse, instead of just once and down the drain. Also, most of the contaminants dragged into the rinse end up in the first stage of the rinse with each stage having fewer contaminants as the board passes through until the board sees fresh water in the final stage.
This concentration of contamination in the first stage also has waste treatment benefits. It is far more efficient and cost-effective to remove 1,000 parts per million of copper from 10 gallons of water than it is to remove 10 parts per million of copper from 1,000 gallons of water. More water savings can be achieved by using some of the water from the contaminated first stage for specific gravity control of the etchant instead of sending it all to waste treatment.
How many stages of cascade rinse do you need? Tests have shown that a four-stage rinse is plenty. After four stages, you run into the law of diminishing returns where you spend a lot more effort for far fewer gains. For most, a three-stage rinse is more than adequate and doesn’t take up much more space than a one-time rinse.
Alkaline etchers have an advantage over cupric chloride and ferric chloride etchers in that they have a flood rinse with replenisher solution right after the etcher. The flood rinse is a low-pressure, recirculated rinse that floods the surface of the panel with a replenisher solution to remove contaminants. This solution is then used for specific gravity and pH control in the etcher. By doing this, most of the etchant dragout is washed off the surface of the panel and put back in the etcher, which is where it belongs.
There is no reason you can’t use this principle for cupric and ferric etchers as well. A two-stage flood rinse using water instead of replenisher solution will wash most of the etchant dragout off the panel surface and put most of it back in the etcher by using this water for specific gravity control. An automatic water add to the second stage will replace the water used from the first stage for specific gravity control. Using this type of flood rinse will reduce the amount of etchant dragout going to your water rinse by about 90%. In turn, this allows even more water-saving options in that water rinse.
I have a three-stage cascade rinse following a two-stage flood rinse on my cupric etcher. Each stage of the cascade rinse has an upper and lower spray tube. Each spray tube has 11 nozzles, each with a flow rate of 0.5 gallons per minute (gpm) at 40 psi for a total flow of 5.5 gpm per spray tube or 11 gpm for the stage. By using the flood rinse to remove most of the dragged-out etchant from the panel surface before the cascade rinse, I can reduce the amount of freshwater flow into the third stage from 11 gpm to about 2 gpm and still keep the water in the sump clean enough to provide a good rinse.
So far, with the use of a chiller for the cooling coil and a two-stage cascaded flood rinse followed by a three-stage cascaded water rinse, we have been able to reduce the water usage in the etch system to about 2 to 3 gpm. With the flood rinse removing most of the drag-out and returning it to the etcher, and by using that water for specific gravity control, the contamination level in the first stage of the water rinse levels out at a few hundred parts-per-million of copper (or iron for a ferric chloride etcher), down from several thousand parts-per-million. This is very treatable and shouldn’t overwhelm most treatment systems.
For those with cupric chloride etchers, even further water savings are possible. The flow and copper levels in the first stage are low enough that a small ion exchange column can be added to the rinse. Water from the first stage goes through the ion exchange to remove the copper and is returned to the last stage of the cascade rinse. In this way, the water usage of the etcher is reduced to practically zero (you’ll need a few gallons per hour of new water due to drag-out and evaporation) and the load on waste treatment systems is greatly reduced. A look at your costs for water and waste treatment should allow you to quickly determine whether the extra expenditure involved for this type of system is justified.
Note: A further environmental benefit can come from using an ion exchange column. It will periodically need to be regenerated as the copper levels inside build up. This is usually done by backwashing with a sulfuric acid solution, resulting in a concentrated copper sulfate solution. This solution can be transferred to an electrolytic cell, and the copper can be recovered, so virtually no copper goes into the waste treatment flow. When we showed this to our local waste treatment authority inspector, he was so ecstatic about it that he forgot to do the rest of the inspection. As everybody knows, a well-disposed and friendly environmental inspector is a good thing.
This column originally appeared in the April 2024 issue of PCB007 Magazine.
More Columns from The Chemical Connection
The Chemical Connection: Sales Organization from a Capital Equipment PerspectiveThe Chemical Connection: Through-glass Vias in Glass Substrates
The Chemical Connection: Reducing Defects in Circuit Board Production
The Chemical Connection: Common Misconceptions in Wet Processing
The Chemical Connection: Surface Finishes for PCBs
The Chemical Connection: Earthquakes, Astronauts, and Aquatics—A Lighter Look at the Past
The Chemical Connection: Better Fabs Attract a Better Workforce
The Chemical Connection: Can Changing Spray Nozzles Improve My Etch Quality?