-
- News
- Books
Featured Books
- pcb007 Magazine
Latest Issues
Current IssueSales: From Pitch to PO
From the first cold call to finally receiving that first purchase order, the July PCB007 Magazine breaks down some critical parts of the sales stack. To up your sales game, read on!
The Hole Truth: Via Integrity in an HDI World
From the drilled hole to registration across multiple sequential lamination cycles, to the quality of your copper plating, via reliability in an HDI world is becoming an ever-greater challenge. This month we look at “The Hole Truth,” from creating the “perfect” via to how you can assure via quality and reliability, the first time, every time.
In Pursuit of Perfection: Defect Reduction
For bare PCB board fabrication, defect reduction is a critical aspect of a company's bottom line profitability. In this issue, we examine how imaging, etching, and plating processes can provide information and insight into reducing defects and increasing yields.
- Articles
- Columns
- Links
- Media kit
||| MENU - pcb007 Magazine
Estimated reading time: 6 minutes
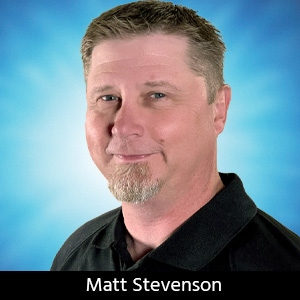
Connect the Dots: Designing for Reality—The Pre-Manufacturing Process
I have been working with Nolan Johnson on a podcast series about designing PCBs for the reality of manufacturing. By sharing lessons learned over a long career in the PCB industry, we hope to shorten learning curves and help designers produce better boards with less hassle and rework. Episode 2 deals with the electronic pre-manufacturing process.
Moving from CAD (computer-aided design) to CAM (computer-aided manufacturing) is a key step in PCB manufacturing. CAM turns digital designs into instructions that machines can use to actually build the PCB. This involves exporting files in a specific format, such as Gerber files. Essentially, the pre-manufacturing process shifts from designing a PCB in a computer to the practical work of manufacturing it. This ensures that what was designed can be precisely made into a physical product with actual, working boards.
Designing for Manufacturability (DFM)
Realistic designs should prioritize manufacturability and reliability of the PCB as well as meet the other design requirements. To do so, one must account for the production variables associated with individual manufacturing partners.
DFM is a great approach for vetting your design and making sure that it will be manufacturable before moving to the quote stage. DFM is all about designing your product in a way that makes it easy and cost-effective to manufacture without compromising quality. This process spots potential issues early and makes the manufacturing process smoother, ensuring the final product is of high quality.
Consider the Manufacturer’s Design Requirements
One important factor to consider in the DFM stage is that design requirements are specific to the manufacturer. Be aware of this when choosing which tool to use for DFM. Your preferred manufacturer may offer a tool or suggest specific tools. In addition, some CAD tools have DFM-type features, but those need to be configured to match your preferred manufacturer's tolerances and requirements. Note that DFM tools operate on either a completed design file or on individual modules.
Understanding both your CAD tool's features and the requirements of your preferred manufacturer is key. To get a better understanding of DFM and this part of the process, please refer to my book, Designing for Reality.
Key Takeaway: Important Design Considerations
Designers should use wider traces and gaps (when possible) in their PCB layouts for the best reliability/cost, though sometimes narrower ones might be necessary. It is important to avoid treating every trace the same way. Utilizing larger holes for vias is another tip for increasing manufacturability and lowering cost. Old concerns about acid traps—caused by sharp angles in traces—may not be much of a manufacturing issue anymore, but best practice for design and signal routing would have you minimize these sharp angle routes.
Maintaining enough distance between component pads with protruding "fingers" is critical to minimize potential solder shorting between these features. A minimum of 4 mils (0.004") solder mask webbing between SMT pads is advised to maintain a solder mask dam between the pads. These practices increase board reliability and durability with today's manufacturing techniques.
Preparing Your Design to Send to the Manufacturer
In the pre-manufacturing phase, different file formats become important. We start with native file formats, which are specific to the CAD software used. However, these files can't always be directly used by manufacturing equipment, so the designer may need to supply Gerber files or have Gerbers created from the native file by the manufacturer. Gerber files have long been the go-to format for sharing PCB design data with manufacturers because they provide the essential information needed to make the boards. This is a venerable file format with a history going back several decades to the early days of PCB manufacturing, though it has been improved over time.
In addition to Gerber files, some manufacturers might require smart data files, like ODB++ and IPC-2581. These carry not just layout information but details about components, assembly, and tests. Sometimes, certain CAD tools or manufacturers might instead use proprietary file types.
When it is time to send your design to your preferred manufacturer, you will need to export your design into the proper file format, such as the Gerber files I’ve mentioned. Once you have exported the file, I highly recommend viewing it in an external file viewer to make sure everything looks right. Gerber files, in particular, can benefit from this additional step.
How the Manufacturer Triages Inbound Designs
At the manufacturer, your PCB design will undergo a triage process. First, CAM software checks the design against the specifications provided in the order, including dimensions, materials, and layer counts, to confirm everything aligns with your expectations and their manufacturing capabilities.
Following this is a manufacturability review, which identifies any elements in the design that might pose challenges during production, such as intricate features that exceed machinery capabilities or materials that are difficult to source. Component availability and lead times are increasingly important, given recent supply chain fluctuations. Ensuring that specified components are readily available helps avoid delays once the production process begins.
It is important to identify and rectify any design issues before the manufacturing phase commences. Although it might seem like an extra step, this saves time, reduces costs, and guarantees that the final products meet both quality standards and client requirements. Essentially, it bridges the gap between design and the practicalities of manufacturing, setting the stage for a smooth and efficient production process.
Key Takeaway: When CAM Changes PCB Designs
Noticed some unexpected tweaks in your design? It's likely in the solder mask layers; more than 50% of all CAM edits occur in these two layers. While it might seem like setting up the solder mask layers should be pretty straightforward, this is not always the case. Your design may flood the entire board with a solder mask, and then you can carefully carve out spaces around all things that need soldering—like SMT pads, through-hole pads, and test points.
It's a delicate art of ensuring these spaces are big enough for soldering to be effective but not so large that they leave nearby copper unnecessarily exposed, which could lead to dreaded solder bridges. Indeed, achieving the ideal balance in solder mask adjustments is an intricate dance the CAM software performs to keep everything in harmony.
The Feedback Loop Between the Designer and the Manufacturer
Once a manufacturer approves a design, the work doesn’t stop there. It can kick off a feedback loop between the manufacturer and the designer, which, though it might seem like extra work at first, can be valuable in the long run. This feedback loop allows the manufacturer to highlight any problems they encounter while trying to make the design a reality, giving the designer a chance to tweak and improve the design. This not only improves the current project but also smooths the path for future designs. This back-and-forth helps spot and fix issues early, avoiding delays and ensuring a better final product.
The feedback loop teaches designers valuable lessons about manufacturing needs and limits, helping them create smarter, more feasible designs right from the start. Over time, as designers become better versed in the practical requirements of their preferred manufacturer, they start to design with manufacturing in mind, leading to reliable, finished PCBs sooner. Therefore, while it may require more effort and patience up front, this collaborative process between designers and manufacturers is important for creating better products and constantly improving design practices.
I hope this has given you greater insight into the electronic pre-manufacturing process of PCB design. In our next episode of On the Line with…, we will be discussing the inner layer process, including materials, imaging, etching, and inspection.
Download The Printed Circuit Designer’s Guide to… Designing for Reality by Matt Stevenson. You can view other titles in the I-007eBooks library.
This column originally appeared in the April 2024 issue of Design007 Magazine.
More Columns from Connect the Dots
Connect the Dots: The Future of PCB Design and ManufacturingConnect the Dots: Proactive Controlled Impedance
Connect the Dots: Involving Manufacturers Earlier Prevents Downstream Issues
Connect the Dots: Stop Killing Your Yield—The Hidden Cost of Design Oversights
Connect the Dots: Designing for Reality—Routing, Final Fab, and QC
Connect the Dots: Designing for Reality—Surface Finish
Connect the Dots: Designing for Reality—Solder Mask and Legend
Connect the Dots: Designing for Reality: Strip-Etch-Strip