-
- News
- Books
Featured Books
- design007 Magazine
Latest Issues
Current IssueProper Floor Planning
Floor planning decisions can make or break performance, manufacturability, and timelines. This month’s contributors weigh in with their best practices for proper floor planning and specific strategies to get it right.
Showing Some Constraint
A strong design constraint strategy carefully balances a wide range of electrical and manufacturing trade-offs. This month, we explore the key requirements, common challenges, and best practices behind building an effective constraint strategy.
All About That Route
Most designers favor manual routing, but today's interactive autorouters may be changing designers' minds by allowing users more direct control. In this issue, our expert contributors discuss a variety of manual and autorouting strategies.
- Articles
- Columns
- Links
- Media kit
||| MENU - design007 Magazine
Estimated reading time: 7 minutes
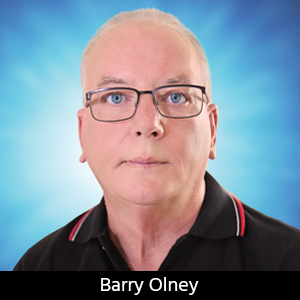
Beyond Design: Dielectric Material Selection Guide
Materials used for the fabrication of multilayer PCBs absorb high frequencies and reduce edge rates. That loss in the transmission line is a major cause of signal degradation. However, not all of us are designing cutting-edge boards and sometimes we tend to over-specify requirements that can lead to inflated production costs. In this month’s column, I will look at the types of materials commonly used for PCB design and how to select an adequate material to minimize costs.
Signals carried by electromagnetic energy propagate through the PCB medium, guided by the signal traces. It is the dielectric material between the copper signal and plane layers in the PCB that affects signal velocity. Dielectric constant (Er or Dk) and dielectric loss (dissipation factor/loss tangent, Df) play crucial roles in signal propagation:
- Dk describes how the material increases capacitance and decreases speed. Higher Dk increases capacitance and decreases signal velocity. It also reduces the impedance of the transmission line.
- Df quantifies the inherent dissipation of electromagnetic energy within the material. It is best to select materials with a low dissipation factor. High Df leads to energy dissipation and signal attenuation. While lossy materials may impact impedance, they are often more cost-effective.
These properties are independent of transmission line geometry but depend on the dielectric material and frequency. They are a function of the dielectric material in which the signal propagates their distribution in the PCB stackup and the applied frequency. These mechanisms contribute to the frequency-dependent loss and degradation of the speed of the signal. The signal quality transmitted through the medium and picked up at the receiver will be affected by any impedance discontinuities and by the losses of the dielectric materials.
The glass epoxy material (FR-4) commonly used for PCBs exhibits negligible loss for digital applications below 1 GHz. But at higher frequencies, the loss is of greater concern. It is crucial to consider the entire bandwidth of the signal. For instance, a 10 Gbps square wave is made up of a series of odd harmonics. It will have a fundamental frequency of 5 GHz, a third harmonic of 15 GHz, a fifth of 25 GHz, and possibly higher odd harmonics. These high harmonics can suffer excessive losses in amplitude and a degradation of edge sharpness, which results in distortion of the signal eye. Plus, when the frequency exceeds 1 GHz, copper roughness, conductor loss, skin effect, and skew, due to variations of glass weave in the dielectric, begin to come into play.
Also of interest is the glass transition temperature (Tg), the point at which a glassy solid changes to an amorphous resin/epoxy. If the reflow temperature exceeds the Tg for an extended period, the material rapidly expands in the Z-axis. Also, the mechanical material properties—strength and bonds in the material—degrade rapidly. A high Tg guards against barrel cracking and pad fracture during reflow. Standard FR-4 has a Tg of 135-170°C, whereas the high-speed materials are generally over 200°C. Therefore, Tg is not a factor that needs to be considered for high-speed design but is certainly worth checking.
Alternatively, low-dielectric polymer materials are widely used in printed circuit boards, communication materials, and other fields due to their several advantages, including processability, thermal stability, and electrical insulation. Materials such as polytetrafluoroethylene (PTFE), liquid crystal polymer (LCP), and polyimide (PI) have already been widely used in RF circuit board substrates.
Low dielectric constant and loss polymeric materials have become increasingly important key areas of electronics and communication due to the demand for high-frequency microelectronics employing minimum signal losses. Low polymer materials are used in high-speed communication networks to improve the overall performance of the devices due to their lower dielectric constant than traditional dielectric materials (Figure 2), which allows for faster signal transmission. These materials are being used in cutting-edge fabrication of microelectronic devices like PCBs, antennas, microwave components for 5G, Internet of Things (IoT), intersatellite communications, and automotive radar applications. The sub-6 GHz range (3.5–7 GHz) is being used for the recently formed 5G, and it is already more congested than the public bands (2.5 GHz and 5 GHz) for Wi-Fi. The next generation 5G network opportunities rely on mainly mmWave (24–71 GHz) frequency range, which is expected to transfer data multi-gigabit per second.
One approach to achieving low Dk and Df is to modify the polymer composite structure by incorporating fillers such as nanoparticles, nanotubes, nano-cubes, and nano-clays. These filters can reduce the Dk and Df of the polymer matrix by increasing the interfacial polarization and facilitating the free volume of the polymer. Another approach is to develop new polymers with inherently low dielectric constant and loss properties. For example, fluorinated polymers such as PTFE and perfluorocyclobutane (PFCB) have low dielectric constants due to the high electronegativity of fluorine atoms. In addition, polyimides (PI), polyphenylene ethers (PPE), and polybenzoxazoles (PBO) have been developed with low dielectric constants and losses for high-frequency applications, employing future electronics and communication industries’ perspectives.
Given the plethora of options available, selecting the right material for your specific product can be quite a task. While opting for low-cost materials might seem tempting, it often comes with compromises in quality. Additionally, poor yields can escalate the overall material cost.
The dielectric material selection primarily hinges on the frequency and rise time of the digital signal. For high-frequency applications, materials with lower loss are preferable. These materials typically exhibit lower dielectric constants, resulting in faster signal propagation. Remember, striking the right balance between performance and cost ensures an optimal choice.
For instance, if we are looking for a dielectric material with a reasonably low dielectric constant and low loss, then we may choose Isola 370HR, which is a suitable all-arounder. This material has a Dk = 3.92 and Df = 0.025 at 5GHz specified in the datasheet. However, the manufacturers always specify the best material in the class, and depending on which glass type you use, it may vary significantly.
From the Isola datasheet, we get a variation in Dk from 3.6 (for the 106) to 4.2 (for the 7628). Also, the Df varies from 0.02 (for the 7628) to 0.03 (for the 106) at 5GHz. The dielectric constant of resin is less than that of the fiber. Increasing the resin content in the laminate reduces the effective Dk of the PCB. So, you should take an average of each class to hone them down. Figures 3 and 4 compare these variables. From these graphs, we can see that 370HR has a rather high Df and an average Dk. A better selection may be the EM-285 or EM-828, which both exhibit lower Dk and Df by comparison. Also, because EMC is a Chinese manufacturer, it will undoubtedly be of low cost. If you are looking for a flex material, then the Isola P96 has reasonable properties.
Also, to further reduce costs and improve power integrity, expensive high-speed material should not be used between the planes. A standard FR-4 material has a higher dielectric constant (Dk), which increases capacitance of the planes, and has a higher dissipation factor (Df), which dampens electromagnetic energy through the relatively high loss of the material.
The materials planner allows designers to strike a balance between performance and production costs. You can set up a list of materials from your preferred suppliers and then compare them directly to get the best material for your product.
Key Points
- Materials used for the fabrication of the multilayer PCBs absorb high frequencies and reduce edge rates and that loss in the transmission line.
- It is the dielectric material between the copper signal and plane layers in the PCB that affects signal velocity.
- The glass epoxy material (FR-4), commonly used for PCBs, exhibits negligible loss for digital applications below 1 GHz.
- When the frequency exceeds 1 GHz, copper roughness, conductor loss, skin effect, and skew, due to variations of glass weave in the dielectric, begin to come into play.
- Low dielectric constant and loss polymeric materials are widely used in printed circuit boards and communication materials due to their several advantages, including processability, thermal stability, and electrical insulation.
- While opting for low-cost materials might seem tempting, it often comes with compromises in quality.
- The dielectric material selection primarily hinges on the frequency and rise time of the digital signal.
Resources:
- “It’s a Material World,” “Material Selection for Serdes Design,” “Material Selection for High-speed Design,” by Barry Olney.
- Research progress of low dielectric constant polymer materials, Zhendong Hu, et al.
- Polymer-based low dielectric constant and loss materials for high-speed communication network: Dielectric constants and challenges, MD Zahidul Islam, et al.
This column originally appeared in the May 2024 issue of Design007 Magazine.
More Columns from Beyond Design
Beyond Design: Effective Floor Planning StrategiesBeyond Design: Refining Design Constraints
Beyond Design: The Metamorphosis of the PCB Router
Beyond Design: Radiation and Interference Coupling
Beyond Design: Key SI Considerations for High-speed PCB Design
Beyond Design: Electro-optical Circuit Boards
Beyond Design: AI-driven Inverse Stackup Optimization
Beyond Design: High-speed Rules of Thumb