-
-
News
News Highlights
- Books
Featured Books
- design007 Magazine
Latest Issues
Current IssueAll About That Route
Most designers favor manual routing, but today's interactive autorouters may be changing designers' minds by allowing users more direct control. In this issue, our expert contributors discuss a variety of manual and autorouting strategies.
Creating the Ideal Data Package
Why is it so difficult to create the ideal data package? Many of these simple errors can be alleviated by paying attention to detail—and knowing what issues to look out for. So, this month, our experts weigh in on the best practices for creating the ideal design data package for your design.
Designing Through the Noise
Our experts discuss the constantly evolving world of RF design, including the many tradeoffs, material considerations, and design tips and techniques that designers and design engineers need to know to succeed in this high-frequency realm.
- Articles
- Columns
- Links
- Media kit
||| MENU - design007 Magazine
The Rise of Collaborative Intelligence in Manufacturing
May 22, 2024 | Jennifer Davis, Arch SystemsEstimated reading time: 2 minutes
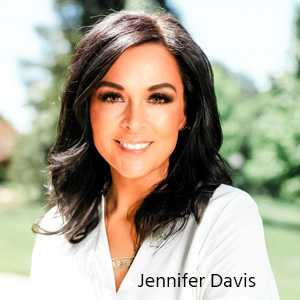
Every modern manufacturer grapples with a common challenge: extracting actionable insights from the ever-growing sea of operational data. The challenge of the data deluge isn’t just overwhelming; it coincides with a broader shift in automation needs. While traditional forms of automation, such as robots, remain vital, the focus is expanding to encompass automating the very intelligence needed to run a factory efficiently. As a result, a new generation of tools and technologies, including artificial intelligence (AI) is beginning to transform the way factories operate.
Designed to unlock the true potential of data, AI algorithms can analyze vast amounts of data, identify hidden patterns, predict potential issues, and empower manufacturers to make data-driven decisions and optimize production processes in real-time.
However, AI's effectiveness hinges on high-quality, readily utilizable data. Manufacturers increasingly demand solutions that not only leverage AI but also seamlessly integrate with existing data infrastructure. Because of this, we’re seeing an exciting trend emerge: solution providers are increasingly forging partnerships to bridge data silos and unlock the full potential of AI for their clients. This collaborative ecosystem holds the key to accelerating the path toward manufacturing excellence.
While collaboration is crucial to accelerating that path, manufacturers must first have a digitalization plan, one that includes a specialized approach to data as well as alignment and commitment from internal teams to the successful application of it.
From Data to Actionable Insights: The Power of Analytics
Modern factories generate a wealth of data from machines, sensors, and software systems. But the true power lies in transforming the data into actionable insights to drive tangible improvements. This requires a seamless information flow, from rich machine data to insightful dashboards and, ultimately, actionable steps on the shop floor.
Here's a breakdown of the ideal data-to-action cycle:
- Rich machine data: Capture comprehensive data from all aspects of production.
- Standardization and brokering: Ensure data standardization through a central broker, allowing for seamless integration across different systems.
- Cloud analytics: Leverage the power of cloud computing for advanced analytics and AI model training.
- Insightful dashboards: Present insights and key performance indicators (KPIs) in a user-friendly and visually appealing manner. This allows potential bottlenecks, equipment failures, quality issues, etc., to be identified in real-time.
- Intelligent actions: Bring corrective actions to the surface, complete with AI-guided playbook recommendations, and enable annotation by factory experts—allowing excellence anywhere in the organization to become excellence everywhere.
Continue reading this article in the May 2024 issue of SMT007 Magazine.
Suggested Items
Specially Developed for Laser Plastic Welding from LPKF
06/25/2025 | LPKFLPKF introduces TherMoPro, a thermographic analysis system specifically developed for laser plastic welding that transforms thermal data into concrete actionable insights. Through automated capture, evaluation, and interpretation of surface temperature patterns immediately after welding, the system provides unprecedented process transparency that correlates with product joining quality and long-term product stability.
Smart Automation: The Power of Data Integration in Electronics Manufacturing
06/24/2025 | Josh Casper -- Column: Smart AutomationAs EMS companies adopt automation, machine data collection and integration are among the biggest challenges. It’s now commonplace for equipment to collect and output vast amounts of data, sometimes more than a manufacturer knows what to do with. While many OEM equipment vendors offer full-line solutions, most EMS companies still take a vendor-agnostic approach, selecting the equipment companies that best serve their needs rather than a single-vendor solution.
Keysight, NTT, and NTT Innovative Devices Achieve 280 Gbps World Record Data Rate with Sub-Terahertz for 6G
06/17/2025 | Keysight TechnologiesKeysight Technologies, Inc. in collaboration with NTT Corporation and NTT Innovative Devices Corporation (NTT Innovative Devices), today announced a groundbreaking world record in data rate achieved using sub-THz frequencies.
Priority Software Announces the New, Game-Changing aiERP
06/12/2025 | Priority SoftwarePriority Software Ltd., a leading global provider of ERP and business management software announces its revolutionary aiERP, leveraging the power of AI to transform business operations.
Breaking Silos with Intelligence: Connectivity of Component-level Data Across the SMT Line
06/09/2025 | Dr. Eyal Weiss, CybordAs the complexity and demands of electronics manufacturing continue to rise, the smart factory is no longer a distant vision; it has become a necessity. While machine connectivity and line-level data integration have gained traction in recent years, one of the most overlooked opportunities lies in the component itself. Specifically, in the data captured just milliseconds before a component is placed onto the PCB, which often goes unexamined and is permanently lost once reflow begins.