Estimated reading time: 5 minutes
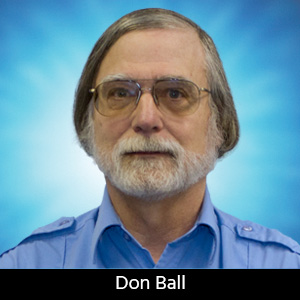
The Chemical Connection: Controlling an Alkaline Etch Bath With Low Copper Loading
This month, I wanted to continue my discussion on how much process control is actually needed for high-density circuit production. However, in the last month, I have been called on to help with a specific process control problem: how to control an alkaline etch bath when you’re not etching much copper. This problem has been cropping up more frequently as smaller shops (and a few larger ones) concentrate on low-volume, high-value plated through-hole panels such as prototypes, resistor cores, etc.
Alkaline etchants were introduced in the early 1970s as production of double-sided and multilayer boards requiring plated through-holes began to increase. The advantage of alkaline etchant over the alternative etchants was that the Cu+1 etching byproduct could be re-oxidized back to Cu+2 to maintain a steady etch rate. The alternatives were all batch etchants that required frequent make-up of new baths and, especially in the case of chrome/sulfuric acid etchant, were environmentally unfriendly.
Alkaline etch has three etchant parameters that must be controlled to keep everything in a delicate balance:
- Specific gravity: This is the main control point. Copper is etched and dissolves into the etchant, raising the specific gravity. When the specific gravity increases to the specified control point, replenisher fluid is added to the system until the specific gravity falls below the set point. The replenisher fluid is basically etchant with no copper in it and excess amounts of ammonia and ammonium chloride (to replace losses of those two commodities during the etching process), keeping everything in balance. The system works well as long as there is a steady supply of copper to be etched. If the supply of copper is not steady, such as small lots of prototype panels with long periods of time between lots, or resistor cores with not much exposed copper to be etched, then the system begins to break down.
- pH: The pH continues to fall, even when the system is not in use, because the ammonia molecule is very small and volatile and will continue to escape no matter how well you think everything is sealed. To get the pH up again and avoid the dreaded sludge-out (low pH causing the copper to crystalize out of solution) more replenisher solution is manually added to the system. Unfortunately, the amount of replenisher that needs to be added to get the pH back to spec lowers the specific gravity to the point where the etch rate is significantly changed. It then becomes necessary to etch more copper (either scrap or dummy panels from the plating shop) to get the copper levels back up to spec.
- Ammonium chloride: Now you are using up the ammonium chloride without replacement since the specific gravity is too low to trigger the replenisher flow and the pH continues to fall again. You must manually add more replenisher solution to both raise the pH and replace the chlorides which, of course, drops the specific gravity again and so on until everything is completely out of control.
What can be done? Here are a few things that could help keep the alkaline etch system under control.
One of the most important and least understood parts of the system is venting, which is needed to not only control ammonia fumes, but to draw air into the etcher for the reoxidation process to get the Cu+1 complex back to the Cu+2 complex. There is such a thing as too much venting. Too much venting will pull more ammonia up the stack and contribute to the pH problem. To set the proper venting the draw on the vents on the etch chamber or after the replenisher rinse should be set so there is negative pressure in the etch chamber. This can be checked by closing the vent at the etcher entrance and holding a rag with the end soaked in hydrochloric acid to the etcher entrance. In the presence of ammonia, the rag will give off a white vapor. Open the vents until the vapor is just drawn into the etch chamber and no more. This should be enough to keep the ammonia fumes in the etcher. The vent at the entrance of the etcher should be set so any stray fumes are captured but not enough to interfere with airflow into the etcher.
Aqueous Ammonia
Use aqueous ammonia (30% ammonium hydroxide) to raise the pH. This will still cause some drop in the specific gravity of the etchant but not nearly as much as using replenisher solution. Aqueous ammonia should be available from any industrial chemical supply company in various size containers. Industrial grade is okay; it doesn’t need to be laboratory grade.
Ammonium Chloride Crystal
Get some ammonium chloride crystal to control the chloride content without affecting the specific gravity of the etch solution. Weigh out the amount of crystal you need to bring the chloride level back into spec and place it in a bucket. Draw some hot etchant from the etch sump into the bucket and stir until the crystal is dissolved, then pour it back into the etcher. Just dumping the crystal into the etcher will cause most of it to settle to the bottom and take a significant time to dissolve. This should also be available from any industrial chemical supplier as well in 20- to 50-pound bags. Again, industrial grade is good enough.
Prepping for More
If you’ve finished one lot but plan to do others that day, leave the heat on, but shut off all sprays, including water rinses and the dryer if the system has one. Close the vent valves to minimize ammonia loss. The butterfly valves provided by most equipment suppliers for venting do not close 100% so there will still be enough vent to control fumes if the spray is off.
When you are done for the day but plan to run the next day, follow the same procedure as above but turn off the heat. Also, remove the pH probe and put it into some 6M KCl storage solution overnight.
It’s probably okay to leave the etchant in the etcher for up to a week if the venting is completely closed or shut off and the solution is up to specifications in terms of the specific gravity, pH, and chloride levels. For longer periods between running, it would be wise to consider putting the etchant back into the original drums and sealing them tight.
Final Tip
Alkaline etchant is notoriously hard on pH probes. Its viscosity is so low that it will inevitably backflow into the probe. When this starts happening, it is best to recalibrate the probe before the first run of the day at a minimum and, even better, twice per shift.
This column originally appeared in the July 2024 issue of PCB007 Magazine.
More Columns from The Chemical Connection
The Chemical Connection: Sales Organization from a Capital Equipment PerspectiveThe Chemical Connection: Through-glass Vias in Glass Substrates
The Chemical Connection: Reducing Defects in Circuit Board Production
The Chemical Connection: Common Misconceptions in Wet Processing
The Chemical Connection: Surface Finishes for PCBs
The Chemical Connection: Earthquakes, Astronauts, and Aquatics—A Lighter Look at the Past
The Chemical Connection: Better Fabs Attract a Better Workforce
The Chemical Connection: Can Changing Spray Nozzles Improve My Etch Quality?