-
- News
- Books
Featured Books
- design007 Magazine
Latest Issues
Current IssueProper Floor Planning
Floor planning decisions can make or break performance, manufacturability, and timelines. This month’s contributors weigh in with their best practices for proper floor planning and specific strategies to get it right.
Showing Some Constraint
A strong design constraint strategy carefully balances a wide range of electrical and manufacturing trade-offs. This month, we explore the key requirements, common challenges, and best practices behind building an effective constraint strategy.
All About That Route
Most designers favor manual routing, but today's interactive autorouters may be changing designers' minds by allowing users more direct control. In this issue, our expert contributors discuss a variety of manual and autorouting strategies.
- Articles
- Columns
- Links
- Media kit
||| MENU - design007 Magazine
In-mold Electronics: The Convergence of Innovative Materials and Manufacturing Techniques
August 7, 2024 | Linda Stepanich, IPCEstimated reading time: 1 minute
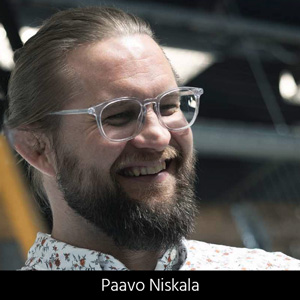
Paavo Niskala, a noted expert in in-mold electronics (IME) at TactoTek, recognized the need for an industry-wide standard when one of his automotive OEM clients asked him how to test a prototype TactoTek had developed. That question led to the creation of the first-ever IPC standard of this type, IPC-8401, Guidelines for In-Mold Electronics, to be released later this year.
“When the customer asked me how to test the part, which is a combination of mechanics and electronics, I realized that a standard for IME does not exist, and that sparked the idea that we should do something,” Paavo says. “Later on, the French plastronics network had the same idea. Our proposal and the French proposal led to the formation of the IPC 3D Plastronics Steering Group. Our first face-to-face meeting was in Lyon, France, in April 2022.”
IME technology merges printed electronics, surface mount (SMT) components, and injection molding using mass-production processes, materials, and components. IME parts are structural electronics characterized by their lightweight, seamless integration. This technology appeals to industries such as automotive or aerospace because it reliably enhances the functionality of surfaces in illuminating spaces, such as door panels, center consoles, and front grill emblems. Combining printed electronics, SMT components, and injection molding is an ideal option for mass production due to the simplicity of both processes.
The automotive industry has driven the development of IME because it significantly reduces the cost, weight, waste, and energy required to produce vehicle interior parts. Rather than using a PCB in a plastic molding with features interacting with PCB sensors, IME components are integrated directly into the plastic molding, making the manufacturing process more streamlined, sustainable, and efficient.
“There's a big market pool for IME, especially in the automotive industry, which is looking for sustainable smart structures,” Paavo says of the new technology's appeal. “They want to build lighting on a 3D surface within the vehicle, whether it's an interior or exterior application. For example, automobiles are full of plastic parts. With IME technology, you can make those thin plastic parts smart and build a lighting application you cannot build with conventional electronics.”
To learn more about the standards being developed for in-mold electronics, read the rest of this article in the Summer 2024 issue of IPC Community.
Testimonial
"Advertising in PCB007 Magazine has been a great way to showcase our bare board testers to the right audience. The I-Connect007 team makes the process smooth and professional. We’re proud to be featured in such a trusted publication."
Klaus Koziol - atgSuggested Items
Nordson Electronics Solutions to Exhibit High-yield Fluid Dispensing Technologies for Panel-level and Wafer-level Packaging at SEMICON Taiwan 2025
08/18/2025 | Nordson Electronics SolutionsNordson Electronics Solutions, a global leader in reliable electronics manufacturing technologies, will demonstrate their latest equipment for semiconductor manufacturing at SEMICON Taiwan 2025, September 10-12, booth i2326.
Thermal Interface Materials – Transition to High-Performance Materials
08/18/2025 | IDTechExIDTechEx forecasts that the market size of thermal interface materials (TIMs) will exceed US$7 billion, covering multiple industries including EV batteries, EV power electronics (TIM1 and TIM2), data centers, advanced semiconductor packaging (TIM1 and TIM1.5), ADAS sensors, consumer electronics, and 5G.
Wistron Announces 1st Half Year of 2025 Financial Results and BOD Results
08/18/2025 | WistronWistron Corp. held a meeting of the Board of Directors. Following the meeting, the company announced the financial results for the first half of 2025.
Foxconn Offers Rare View On Electric SUV And AI Infrastructure At Taiwan Expo USA
08/18/2025 | FoxconnHon Hai Technology Group (Foxconn) on Thursday displayed, for the first time in the United States, its North American-variant electric SUV and demonstrated, for only the second time, its cutting-edge artificial intelligence infrastructure, at Taiwan Expo USA, a conference highlighting the strength of a key partnership in this era of industrial evolution.
Koh Young Appoints George Hsu to Lead Newly Opened Taiwan Office to Drive Semiconductor and Advanced Packaging Growth
08/18/2025 | Koh YoungKoh Young Technology, the global leader in True 3D measurement-based inspection and metrology solutions, is pleased to announce the appointment of George Hsu as Managing Director of Koh Young Taiwan, its newly established branch office in Zhubei City, Hsinchu County.