-
-
News
News Highlights
- Books
Featured Books
- pcb007 Magazine
Latest Issues
Current IssueThe Hole Truth: Via Integrity in an HDI World
From the drilled hole to registration across multiple sequential lamination cycles, to the quality of your copper plating, via reliability in an HDI world is becoming an ever-greater challenge. This month we look at “The Hole Truth,” from creating the “perfect” via to how you can assure via quality and reliability, the first time, every time.
In Pursuit of Perfection: Defect Reduction
For bare PCB board fabrication, defect reduction is a critical aspect of a company's bottom line profitability. In this issue, we examine how imaging, etching, and plating processes can provide information and insight into reducing defects and increasing yields.
Voices of the Industry
We take the pulse of the PCB industry by sharing insights from leading fabricators and suppliers in this month's issue. We've gathered their thoughts on the new U.S. administration, spending, the war in Ukraine, and their most pressing needs. It’s an eye-opening and enlightening look behind the curtain.
- Articles
- Columns
- Links
- Media kit
||| MENU - pcb007 Magazine
Maximizing ROI Through Better Wet Process Control
August 20, 2024 | I-Connect007 Editorial TeamEstimated reading time: 2 minutes
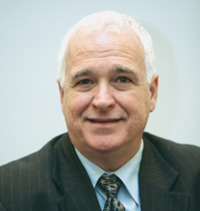
Mike Carano is a program manager and SME for advanced packaging and PCB technologies at Trusted Semiconductor Solution. He has more than 40 years of experience in the electronics industry, with special expertise in manufacturing, performance chemicals, metals, semiconductors, medical devices, and advanced packaging.
For this issue, we reached out to Mike to learn more about how dialing in on wet process can benefit your bottom line.
“When things get out of control, the variation in your wet process begins,” Mike says. “Just because they look like good boards and may even pass electrical test, it does not necessarily mean you have good boards. Once the chemistry is headed toward the right or left side of the process control parameter cliff, the plating is compromised. If the copper is thinner than it should be, when the customer puts it into service, the board may fail after 500 cycles vs. the requisite 1,000 or 2,000 cycles. The root cause issue is that you plated 7/10ths of a mil of copper instead of one-mil of copper because you were not controlling your process. The fact that you passed your own electric test becomes inconsequential.”
What he’s really talking about is the need for a paradigm shift “where tight control of your processes is the way you manage your organization, wet process being one particular and crucial area of operations.”
With respect to process control, he tells his clients, “you have to stop thinking like a fabricator and think more like a semiconductor company.” Don't be solely reliant on your suppliers’ technical support to do the job either, he adds, because by then, it could be too late. “We all need to be laser-focused on precision. We need to be better at what we do. Perfection may not be attainable, but we should strive to get as close as we can. You achieve that through process control, which encompasses the critically essential skills of troubleshooting, root-cause analysis, problem-solving, and strategizing.
Marcy LaRont: Mike, PCB fabricators care about quality and yield because it ultimately translates to cost and profitability. Today, we also have sustainability goals and requirements. What should be the priorities in tightening up control?
Mike Carano: It has been frustrating over the years to witness the general lack of ability to troubleshoot and solve problems in some of the places I visit, which is why I write articles and present courses on advanced troubleshooting. I often see a “teeter-totter” mindset, this conundrum that you must sacrifice either quality or productivity and that somehow you can’t have both. Of course, the manufacturing folks err toward greater productivity, so you always have control over all your processes in real-time. Things will always go wrong. But when you simply rely on mass inspection, and don’t focus on process control, costs and rework go up, and productivity ultimately declines, all because of an imperfect system.
To read the rest of this article, which appeared in the August 2024 issue of PCB007 Magazine, click here.
Suggested Items
SMT007 Magazine July—What’s Your Competitive Sweet Spot?
07/01/2025 | I-Connect007 Editorial TeamAre you in a niche that’s growing or shrinking? Is it time to reassess and refocus? We spotlight companies thriving by redefining or reinforcing their niche—what are their insights? In the July 2025 issue of SMT007 Magazine, we spotlight companies thriving by redefining or reinforcing their niche and offer insights to help you evaluate your own.
Smarter Machines Use AOI to Transform PCB Inspections
06/30/2025 | Marcy LaRont, PCB007 MagazineAs automated optical inspection (AOI) evolves from traditional end-of-process inspections to proactive, in-line solutions, the integration of AI and machine learning is revolutionizing defect reduction and enhancing yields, marking a pivotal shift in how quality is managed in manufacturing.
Magnalytix and Foresite to Host Technical Webinar on SIR Testing and Functional Reliability
06/26/2025 | MAGNALYTIXMagnalytix, in collaboration with Foresite Inc., is pleased to announce an upcoming one-hour Webinar Workshop titled “Comparing SIR IPC B-52 to Umpire 41 Functional & SIR Test Method.” This session will be held on July 24, 2025, and is open to professionals in electronics manufacturing, reliability engineering, and process development seeking insights into new testing standards for climatic reliability.
The Death of the Microsection
06/26/2025 | Bob Neves, Reliability Assessment Solutions, Inc.I got my start out of college grinding and polishing PCB microsections. My thumbs are a bit arthritic today because of the experience (microsection grinders know what I mean). Back then, via structures were rather large, and getting to the center in six steps of grinding and polishing was easy compared to what my team has been doing recently at the lab.
Specially Developed for Laser Plastic Welding from LPKF
06/25/2025 | LPKFLPKF introduces TherMoPro, a thermographic analysis system specifically developed for laser plastic welding that transforms thermal data into concrete actionable insights. Through automated capture, evaluation, and interpretation of surface temperature patterns immediately after welding, the system provides unprecedented process transparency that correlates with product joining quality and long-term product stability.