-
- News
- Books
Featured Books
- design007 Magazine
Latest Issues
Current IssueProper Floor Planning
Floor planning decisions can make or break performance, manufacturability, and timelines. This month’s contributors weigh in with their best practices for proper floor planning and specific strategies to get it right.
Showing Some Constraint
A strong design constraint strategy carefully balances a wide range of electrical and manufacturing trade-offs. This month, we explore the key requirements, common challenges, and best practices behind building an effective constraint strategy.
All About That Route
Most designers favor manual routing, but today's interactive autorouters may be changing designers' minds by allowing users more direct control. In this issue, our expert contributors discuss a variety of manual and autorouting strategies.
- Articles
- Columns
- Links
- Media kit
||| MENU - design007 Magazine
Estimated reading time: 5 minutes
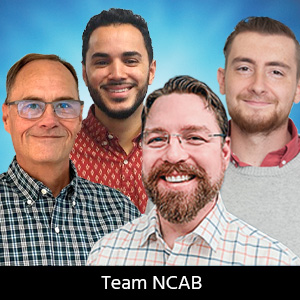
Fresh PCB Concepts: The Vital Role of Front-end Engineers
Front-end engineers are the gatekeepers of factories and a cornerstone of successful fabrication. They are highly valued professionals who could be considered the protectors of our field. They study the details of each PCB that comes into their factories. Many of the boards they work on have not been manufactured before. Others have not been manufactured with their factory’s tools. Since factory engineers are not often in the public eye, many people do not understand the wealth of knowledge they have. I encourage you to develop a good relationship with the engineers at your favorite supplier. The guidance they can offer is invaluable to some PCB designs.
In this column, I share my experiences with the benefits of working with your PCB suppliers’ engineers to facilitate a successful build.
The front-end engineers provide an extra layer of protection for a PCB design to ensure a successful build. They accomplish a very detailed analysis of the PCB during tooling. The first order of business involves setting up the data in the computer-aided manufacturing (CAM) software and reviewing the accompanying board specifications.
During this phase, factory personnel will analyze the fabrication drawings and other documentation provided with the PCB. Any specifications not provided cannot be considered. This may seem obvious, but in my experience, it is not. Sometimes, front-end engineers will learn something is missing by reading the documentation that accompanies the PCB data or by reviewing the manufacturing data. This will begin with a list of engineering questions (EQs) sent to the designer to answer. The last thing anyone wants is assumptions based on unclear or missing documentation.
During this part of the process, EQs may be generated. If there is one piece of advice I could share, it would be to make sure the notes on the fabrication drawing are clear. I have read many professionally written fabrication drawings that did not clearly explain board fabrication requirements. On one occasion, an engineer sent me a hand-written fabrication drawing he produced with colored pencils. It did not look as professional as other drawings, but it had every detail I needed to make his board a success. At any rate, the goal in this part of the tooling phase is to study the board and its requirements.
The next step is to begin optimization. If applicable, the engineer will review the stackup, impedance requirements, and array drawing. They will also produce an in-house stackup with the exact pressing results from the factory’s specific presses. If there are no stackup requirements, the front-end engineers will still complete an in-house stackup. This is a safety measure to obtain the correct board thickness the first time. They know exactly how the board will press out using their factory’s tools and the required materials. They will also use tools to calculate impedance traces to ensure the impedances will work. Many times, customers send stackups with impedance requirements that simply do not work. The array will also go through an optimization process. If not already included in the manufacturing data, the front-end engineer will draw the array using CAM software.
Factory engineers are familiar with every detail required to maximize the number of parts in the array while maintaining stability for assembly. They will question the customer-provided array if something does not work. On one occasion, a customer asked me to produce a two-layer board on polytetrafluoroethylene (PTFE) material. He was in a hurry, so he did not want to wait on the lead time for more material. He supplied one panel of the material. The front-end engineer raised concerns about the parts being too close together to remain in the array after the routing operation. There was not enough material between boards to retain each PCB in the array. However, our customer was relentless in his inexperience. Once completed, most of the PCBs fell out of the array. The front-end engineers are great at catching issues like this during tooling. Suffice it to say, sometimes they will save us from our blunders.
When the factory tools the data, the detailed analysis continues. Many factories will run the manufacturing data through several software systems to find issues in the data. On some occasions, CAD systems generate bad data. While the mystery of “what happened here” may not be solved, the front-end engineer will catch the mistake. Sometimes the IPC allows the factory to fix it. Other times, questions will be added to the growing EQ list. During this stage, engineers examine trace widths and copper spacing to ensure sufficient room to apply the appropriate amount of etch compensation. In addition, he or she will resize the drills, solder mask clearances, and clip silkscreen as necessary, among other operations. If a problem is discovered, rest assured, this engineer will also have the best possible solution. When the data is completely tooled, the digital files are then sent to the applicable factory departments that will require the data to run the machines. For example, the printing department will use the data to print the electrical layers.
At some point, the end customer will respond to the submitted EQs. The front-end engineers will make final adjustments based on the answers to the questions. Before starting the manufacturing process, the front-end engineers will produce proprietary travelers for each PCB. Depending on the design, some PCBs will have multiple travelers. Travelers are the instructions that accompany the job through the factory. This list of instructions will be with the job from the material preparation department through the final inspection. It contains details for each department to follow. For example, during the pressing operation, the layup personnel can look at the traveler and in-house stackup to understand exactly what they need to do. They will have details on exactly how the materials should be placed in the book and the press recipe. PCB factories do not share the travelers with anyone, as they are proprietary, and in some cases, may have information regarding the factory’s processes and procedures.
I worked for many years in a factory as part of the front-end team and was privileged to learn from many different engineers. After so much detailed analysis, front-end engineers know the PCB and its specifications well. This leaves them with little time to talk with all their customers. Some PCB suppliers have engineers who work directly with the factory and customers to solve problems. As I mentioned, front-end engineers are the gatekeepers of the PCB manufacturing world. They save our designs from ourselves and our systems, as both can make mistakes. Until we perfect PCB manufacturing, we cannot overstate the value of a factory engineer.
Ryan Miller is a field applications engineer with NCAB Group.
More Columns from Fresh PCB Concepts
Fresh PCB Concepts: Designing for Success at the Rigid-flex Transition AreaFresh PCB Concepts: More Than Compliance—A Human-centered Sustainability Approach
Fresh PCB Concepts: Assembly Challenges with Micro Components and Standard Solder Mask Practices
Fresh PCB Concepts: The Power of a Lunch & Learn for PCB Professionals
Fresh PCB Concepts: Key Considerations for Reliability, Performance, and Compliance in PCBs
Fresh PCB Concepts: Traceability in PCB Design
Fresh PCB Concepts: Tariffs and the Importance of a Diverse Supply Chain
Fresh PCB Concepts: PCB Stackup Strategies—Minimizing Crosstalk and EMI for Signal Integrity