-
- News
- Books
Featured Books
- pcb007 Magazine
Latest Issues
Current IssueThe Hole Truth: Via Integrity in an HDI World
From the drilled hole to registration across multiple sequential lamination cycles, to the quality of your copper plating, via reliability in an HDI world is becoming an ever-greater challenge. This month we look at “The Hole Truth,” from creating the “perfect” via to how you can assure via quality and reliability, the first time, every time.
In Pursuit of Perfection: Defect Reduction
For bare PCB board fabrication, defect reduction is a critical aspect of a company's bottom line profitability. In this issue, we examine how imaging, etching, and plating processes can provide information and insight into reducing defects and increasing yields.
Voices of the Industry
We take the pulse of the PCB industry by sharing insights from leading fabricators and suppliers in this month's issue. We've gathered their thoughts on the new U.S. administration, spending, the war in Ukraine, and their most pressing needs. It’s an eye-opening and enlightening look behind the curtain.
- Articles
- Columns
- Links
- Media kit
||| MENU - pcb007 Magazine
Scrutinizing Solder Printing
September 10, 2024 | Nolan Johnson, I-Connect007Estimated reading time: 2 minutes
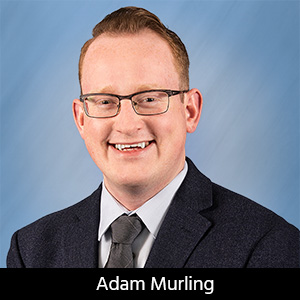
As members of the technical staff at Indium, Adam Murling, technical manager, and Ron Lasky, senior technologist and professor at Dartmouth University, know their way around metallurgy and solder formulation. I corralled them for a conversation on solder application techniques from the solder’s perspective and their insights did not disappoint.
Nolan Johnson: Adam, what are some threshold moments when you go to solder jetting over solder printing?
Adam Murling: It’s a tandem approach, not all-or-nothing. Let’s say you have a four- or five-mils- (100 to 123 micron) thick stencil, but you also have really fine-pitch BGAs on the same device. There's an argument to be made for not cutting those apertures out because the area ratio will be too challenging.
But then you have a jet or dispenser down the line that can take care of those finer particles, and you want to make sure that the flux chemistry is compatible with the paste you're using in a jet as well as the solder paste on the screen printer; they need to be compatible.
But what happens when things are too large? You have most smaller devices—the 01005s, the 0201s and 0.3-millimeter pitch BGAs, etc.—but you also have connectors that require more solder volume than a 3-mil (75 micron) stencil can provide. You can always use a step stencil—it's been a practice for a long time—but at the same time it causes some process challenges.
If you had both pieces of equipment (stencil printing and jetting) you could then do additive manufacturing and essentially jet the paste on top of your 3-mil (75 micron) height, which was deposited through the stencil, to get more solder volume before placing the connector in place.
Johnson: If you factor in additive manufacturing thinking to solder paste application to get a certain height, does that become a designer concern as much as an assembly concern?
Murling: Nolan, everything's going super small. You're having these automotive manufacturers that are getting into the space and they're not able to find those larger parts that they're comfortable working with anymore. Everyone's focusing more on the smaller devices. They're more readily available with the same power output, but they still need those connectors. You will need a step stencil or you could do the additive approach.
To read this entire conversation, which appeared in the September 2024 issue of SMT007 Magazine, click here.
Suggested Items
Hands-On Demos Now Available for Apollo Seiko’s EF and AF Selective Soldering Lines
06/30/2025 | Apollo SeikoApollo Seiko, a leading innovator in soldering technology, is excited to spotlight its expanded lineup of EF and AF Series Selective Soldering Systems, now available for live demonstrations in its newly dedicated demo room.
Indium Corporation Expert to Present on Automotive and Industrial Solder Bonding Solutions at Global Electronics Association Workshop
06/26/2025 | IndiumIndium Corporation Principal Engineer, Advanced Materials, Andy Mackie, Ph.D., MSc, will deliver a technical presentation on innovative solder bonding solutions for automotive and industrial applications at the Global Electronics A
Fresh PCB Concepts: Assembly Challenges with Micro Components and Standard Solder Mask Practices
06/26/2025 | Team NCAB -- Column: Fresh PCB ConceptsMicro components have redefined what is possible in PCB design. With package sizes like 01005 and 0201 becoming more common in high-density layouts, designers are now expected to pack more performance into smaller spaces than ever before. While these advancements support miniaturization and functionality, they introduce new assembly challenges, particularly with traditional solder mask and legend application processes.
Knocking Down the Bone Pile: Tin Whisker Mitigation in Aerospace Applications, Part 3
06/25/2025 | Nash Bell -- Column: Knocking Down the Bone PileTin whiskers are slender, hair-like metallic growths that can develop on the surface of tin-plated electronic components. Typically measuring a few micrometers in diameter and growing several millimeters in length, they form through an electrochemical process influenced by environmental factors such as temperature variations, mechanical or compressive stress, and the aging of solder alloys.
SolderKing’s Successful Approach to Modern Soldering Needs
06/18/2025 | Nolan Johnson, I-Connect007Chris Ward, co-founder of the family-owned SolderKing, discusses his company's rapid growth and recent recognition with the King’s Award for Enterprise. Chris shares how SolderKing has achieved these award-winning levels of service in such a short timeframe. Their secret? Being flexible in a changing market, technical prowess, and strong customer support.