-
- News
- Books
Featured Books
- smt007 Magazine
Latest Issues
Current IssueSupply Chain Strategies
A successful brand is built on strong customer relationships—anchored by a well-orchestrated supply chain at its core. This month, we look at how managing your supply chain directly influences customer perception.
What's Your Sweet Spot?
Are you in a niche that’s growing or shrinking? Is it time to reassess and refocus? We spotlight companies thriving by redefining or reinforcing their niche. What are their insights?
Moving Forward With Confidence
In this issue, we focus on sales and quoting, workforce training, new IPC leadership in the U.S. and Canada, the effects of tariffs, CFX standards, and much more—all designed to provide perspective as you move through the cloud bank of today's shifting economic market.
- Articles
- Columns
- Links
- Media kit
||| MENU - smt007 Magazine
Battling Counterfeit Electronics in Manufacturing
October 7, 2024 | Nolan Johnson, I-Connect007Estimated reading time: 2 minutes
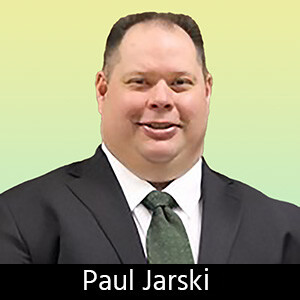
Paul Jarski, product development manufacturing leader at Case New Holland (CNH), discusses his extensive experience with counterfeit electronics throughout his career. He highlights the challenges faced during market allocations, where counterfeit parts infiltrated supply chains and causing significant issues. Paul recounts the rigorous processes implemented to detect and prevent counterfeits, including advanced material analysis and testing. Counterfeit parts occasionally slipped through despite these measures, leading to costly and time-consuming audits and verifications to ensure product integrity and safety.
Nolan Johnson: Paul, tell me a little about your background.
Paul Jarski:
Paul Jarski: I currently work with large and compact tractors at CNH. I’m the liaison between the product development and manufacturing organizations.
Prior to this role, I’ve spent most of my career in agricultural technology, both with CNH and other companies. With the advances in farming technology, the development of rugged electronics equipment has been and continues to be a critical part of the business.
Johnson: So, you have an extensive background in managing counterfeiting issues.
Jarski: Yes. For most of my career, I have been involved in the manufacturing, quality, and supply chain portions of the AG electronics business. I started my career in this area as a process/quality engineer as a liaison between my company and EMS providers. We'd get a product stable and move it to the EMS provider. We still owned the design and controlled everything in the BOM, the AML.
We all know the electronics industry goes through allocations every three to four years. When that happened, we looked for parts. We went to the broker market if we couldn’t get them through normal chains.
I remember some of the first brokered parts we bought in the mid-2000s. After the 2008 economic meltdown, everybody in the electronics industry had slashed their capacity. For the ag industry, it was a blip. In the space of a year, we went from building at 100% capacity to cutting production to going all out and needing to increase equipment capacity. When everybody in the electronics component industry had cut capacity, we had to go to the broker market to find components. However, we also realized the inherent danger in this approach, so we knew we had to be careful of what we purchased.
When we purchased components from the secondary (broker) market, we started implementing checks to verify authenticity. I remember clearly some of the first counterfeits. As soon as they came in, we suspected something was wrong. The labels were poorly printed on the reels, the silk screening on the physical parts wasn't spelled correctly, and you could rub the labeling off the part. I remember us throwing some samples in the X-ray, only to find there was nothing inside. We saw a lot of crude stuff. If you had an X-ray and a cotton swab with acetone, you could tell if it was a counterfeit.
Fast forward to the next market allocation in the 2013-14 timeframe and we found that counterfeiters had advanced their game significantly.
To read this entire conversation, which appeared in the October 2024 issue of SMT007 Magazine, click here.
Testimonial
"The I-Connect007 team is outstanding—kind, responsive, and a true marketing partner. Their design team created fresh, eye-catching ads, and their editorial support polished our content to let our brand shine. Thank you all! "
Sweeney Ng - CEE PCBSuggested Items
It’s Only Common Sense: 20 Lessons in 20 Years—A Career in Common Sense
08/25/2025 | Dan Beaulieu -- Column: It's Only Common SenseIt’s been 20 years and 1,000 columns since I published my first monthly edition called “It’s Only Common Sense” on Sept. 5, 2005. I had only written 10 columns when I realized I couldn’t be confined to once a month. I simply had too much to say. So, on July 31, 2006, I started writing once a week, and let me tell you, that’s a lot of Mondays spent thinking, listening, watching, and writing about this wild, brutal, and beautiful industry we call the printed circuit board business.
Survey Says Reshoring is a TCO Equation
08/13/2025 | Nolan Johnson, SMT007 MagazineHarry Moser, founder of the Reshoring Initiative, and Kathy Nunnally of Regions Recruiting partnered to survey contract manufacturers and OEMs earlier this year, querying them about their offshoring beliefs and practices. They found that while offshoring, tariffs, trade balances, and the like, are important to a company’s bottom line, there’s a larger and more extensive issue: workforce. In this interview, they detail the results of that survey and what they believe can and should be done to fix this long-standing issue.
Akrometrix Announces 30 Year Anniversary as Industry Leader in Thermal Warpage Metrology
02/25/2025 | Akrometrix LLCAkrometrix is celebrating their 30 year anniversary as an industry leader in thermal warpage metrology. Professor Ifeanyi Charles Ume founded Akrometrix out of Georgia Tech 30 years ago to address issues in PCB flatness using the shadow moiré warpage measurement technique.
PCB Designers of the Future—and Their Software Tools
02/14/2025 | Andy Shaughnessy, Design007 MagazineThe PCB designers of tomorrow have their work cut out for them. They’ll be dealing with the continuing drive for “faster, smaller, cheaper,” while electronics become more complex. But EDA companies have improved their software tools’ capabilities over the past few years, incorporating functionalities such as AI and increasing productivity. I asked David Wiens, product marketing manager at Siemens, to share his thoughts on the continuing evolution of PCB design and PCB designers, and how EDA software companies can help designers meet the technological requirements of tomorrow.
Delivering on a Promise: Mid-America Taping and Reeling Outpacing the Competition
02/10/2025 | Linda Stepanich, IPCA motto on the conference wall at Mid-America Taping and Reeling, “Promise only what you can deliver and then deliver more than you promised,” has led Barbara Pauls from the has led from starting her business in her parent's basement to a thriving company with locations in Illinois and Florida and 75 employees.