-
- News
- Books
Featured Books
- smt007 Magazine
Latest Issues
Current IssueSupply Chain Strategies
A successful brand is built on strong customer relationships—anchored by a well-orchestrated supply chain at its core. This month, we look at how managing your supply chain directly influences customer perception.
What's Your Sweet Spot?
Are you in a niche that’s growing or shrinking? Is it time to reassess and refocus? We spotlight companies thriving by redefining or reinforcing their niche. What are their insights?
Moving Forward With Confidence
In this issue, we focus on sales and quoting, workforce training, new IPC leadership in the U.S. and Canada, the effects of tariffs, CFX standards, and much more—all designed to provide perspective as you move through the cloud bank of today's shifting economic market.
- Articles
- Columns
- Links
- Media kit
||| MENU - smt007 Magazine
NEOTech Announces Implementation of Enhanced Wire Bonding Process to Boost Microelectronics Manufacturing Efficiency
October 8, 2024 | NEOTechEstimated reading time: 3 minutes
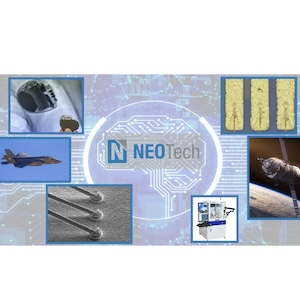
NEOTech, a leading provider of electronic manufacturing services (EMS), design engineering, and supply chain solutions in the high-tech industrial, medical device, and aerospace/defense markets, is excited to announce the recent implementation of an enhanced wire bonding manufacturing process for microelectronics circuit assemblies. This innovative process significantly increases production yields while reducing the production cycle time for each assembly. NEOTech remains committed to continuous improvements, particularly in the manufacturing of extraordinarily high-tech microelectronics products for the nation’s leading OEMs in the Aerospace & Defense, Medical Device, and Industrial markets. As part of this commitment, NEOTech has researched, tested, and qualified an advanced wire bonding technique known as Standoff Stitch (SOS), which further reinforces the company’s dedication to delivering high-quality, precision-driven solutions.
NEOTech, already recognized as an industry leader in SMT electronics manufacturing, stands at the forefront of high-tech microelectronics circuit assembly as well. The company’s original first-pass yields for wire bond and bond pull test processes were already excellent, achieving a 99.3% success rate. However, for mission-critical electronics used in aerospace, defense, space, and medical implantable device applications, even this high yield rate required further improvement. Common methods to enhance wire bond yield and reliability, such as the Burnishing process and the Security Bonding process, have been effective but significantly increase production time. To address this challenge, NEOTech has researched and implemented the SOS wire bond process, which not only boosts reliability but also reduces the production cycle time, offering a more efficient solution without compromising quality.
The SOS wire bond process is a superior method for ensuring high-quality interconnects of micro fine wires to the conductive pads on the substrate surface, which are often uneven or wavy due to the screen-printing process. When standard wire bonding methods are applied to these uneven surfaces, poor bond adherence can result, impacting overall quality. The SOS process addresses this issue by incorporating a gold ball approximately 2.5 mil in diameter during the first step of the wire bonding process. This gold ball accommodates the uneven surfaces without the need for additional steps, significantly reducing production time for each assembly. Furthermore, the increased surface area at the substrate bond interface created by the gold ball forms a more robust bond, enhancing reliability. NEOTech has seen remarkable improvements from this method, with production yields increasing to 99.99% and throughput doubling.
Jim Doyle, Chief Executive Officer of NEOTech’s Aerospace & Defense Business, expressed his enthusiasm for the recent advancements, stating, “At NEOTech, we are dedicated to fostering a culture of continuous improvement to ensure we consistently deliver the highest quality products to our customers. The implementation of the SOS wire bonding process is a testament to our commitment to innovation and operational excellence. By enhancing our wire bonding capabilities, we not only improve production efficiency but also ensure the reliability and performance of mission-critical microelectronics for the aerospace, defense, medical, and industrial sectors. We are proud of our team’s unwavering focus on quality and their efforts to push the boundaries of what’s possible in electronics manufacturing.”
NEOTech distinguishes itself through its broad capabilities and exceptional service offerings, serving industries such as aerospace/defense, medical devices, industrial, and high-tech sectors. Renowned for delivering high-quality products and solutions, NEOTech has become a trusted partner for complex, mission-critical electronic manufacturing projects. The company’s cutting-edge facilities and advanced manufacturing technologies guarantee precision and reliability in every product. NEOTech’s commitment to quality is evident through its adherence to stringent standards, backed by certifications like ISO 9001:2015, ISO 13485:2016, and AS9100.
At the core of NEOTech’s success is its customer-centric approach. Offering a comprehensive suite of services — from design and prototyping to full-scale production and post-production support — NEOTech tailors its solutions to meet each customer’s specific needs. The company’s ability to provide personalized solutions, while also reducing time-to-market and optimizing costs, has earned it a strong reputation for delivering exceptional value.
Testimonial
"In a year when every marketing dollar mattered, I chose to keep I-Connect007 in our 2025 plan. Their commitment to high-quality, insightful content aligns with Koh Young’s values and helps readers navigate a changing industry. "
Brent Fischthal - Koh YoungSuggested Items
MacDermid Alpha Awarded for Innovation: Driving Process Optimization and Efficiency with Major Indian EMS Provider
08/28/2025 | MacDermid Alpha Electronics SolutionsMacDermid Alpha Electronics Solutions, a leading global supplier of integrated materials for the electronics industry, is recognized by one of India’s top EMS providers, Syrma SGS, with an award for innovation that advanced process optimization, enhanced operational efficiency, and yield gains.
Partnerships Drive Innovation for a Brighter Manufacturing Future
08/26/2025 | Barry Matties, I-Connect007When Schweitzer Engineering Laboratories (SEL) opened its greenfield facility in 2023, it did so with careful attention to choosing its suppliers. In this discussion, Collin Peters, electronics business director for North America at MKS’ Atotech, and Justin Kennedy, manager of engineering at SEL, explore their unique partnership that includes collaborative efforts to develop innovative solutions like the Uniplate® PLBCu6 line.
The Art and Science of PCB Floor Planning: A Comprehensive Guide
08/14/2025 | Cory Grunwald and Jeff Reinhold, Monsoon SolutionsPCB design is an intricate and crucial part of developing electronic products. One of the foundational stages of PCB design is floor planning, a phase where the placement of components and the flow of signals are meticulously mapped out. A good floor plan ensures that the PCB performs well, is easy to manufacture, and meets all mechanical and electrical requirements. We’ll explore the essential aspects of floor planning, from its objectives and process to the challenges that designers face.
Advint and SanRex Expand High-Performance DC Rectifier Access for North American PCB Fabricators
08/12/2025 | Advint IncorporatedAdvint Incorporated has entered a strategic partnership with SanRex Corporation, enhancing access to industrial-grade DC rectifiers for the US printed circuit board industry. With a legacy of power innovation and performance across the globe, SanRex rectifiers are available through Advint’s proficient distribution network.
Advint and Sayron Bring Advanced Rectifier Solutions to High-Reliability PCB Manufacturers
08/01/2025 | Advint IncorporatedAdvint Incorporated has partnered with Sayron, a leading global rectifier manufacturer, to supply cutting-edge IGBT-based DC rectifiers to high-performance PCB manufacturers across North America and beyond. Sayron’s precision-engineered rectifiers align with the stringent requirements of advanced PCB processes.