-
- News
- Books
Featured Books
- smt007 Magazine
Latest Issues
Current IssueSpotlight on India
We invite you on a virtual tour of India’s thriving ecosystem, guided by the Global Electronics Association’s India office staff, who share their insights into the region’s growth and opportunities.
Supply Chain Strategies
A successful brand is built on strong customer relationships—anchored by a well-orchestrated supply chain at its core. This month, we look at how managing your supply chain directly influences customer perception.
What's Your Sweet Spot?
Are you in a niche that’s growing or shrinking? Is it time to reassess and refocus? We spotlight companies thriving by redefining or reinforcing their niche. What are their insights?
- Articles
- Columns
- Links
- Media kit
||| MENU - smt007 Magazine
Data-driven Precision in PCBA Manufacturing
November 13, 2024 | Julie Cliche-Dubois, CogiscanEstimated reading time: 1 minute
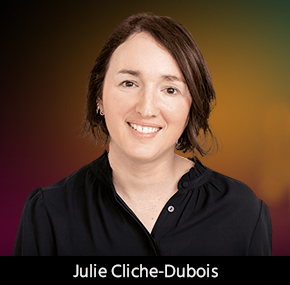
The intricacies involved in electronics manufacturing require more than just expensive equipment and skilled technicians; they necessitate an accurate understanding of the entire production flow, informed and driven by access and visibility to reliable data.
As more manufacturers focus on factory data to improve their operations, they turn to advanced analytics platforms, like one offered by Cogiscan. This fully customizable platform was designed for PCBA manufacturing and is specifically geared toward low- to mid-volume mixed-vendor environments where changeover is frequent, many different brands of machines are on the production floor, and a continuous improvement mindset is culturally embedded from the shop floor to the top floor. In this article, we'll use our software platform as a use case for helping electronics manufacturers across all levels of the production operation.
The Data Imperative
Let’s begin at the beginning regarding getting the data from the shop floor. In the domain of printed circuit board assembly (PCBA) manufacturing, data is as abundant as it is complicated. The manufacturing line comprises diverse, specialized machines working together to create complex PCBAs. From solder paste printers that lay the solder paste foundation for healthy circuit connections to placement machines that populate the board with hundreds of different types of components, each piece of equipment generates a wealth of data. Reflow ovens, solder paste inspection (SPI) machines, and automated optical inspection (AOI) systems further contribute to the data stream with their critical roles in the quality of the finished product.
Figure 1: Illustration of typical PCBA manufacturer.
However, the true value of this data can only be realized when it is effectively enriched–– transformed from raw and nonsensical numbers into a coherent narrative to inform strategic decision-making. Collecting and processing data from disparate sources, this software program makes it possible to achieve a comprehensive view of the manufacturing line, multiple lines, or even distributed manufacturing sites. With enriched data, electronics manufacturers can improve their current operations and future-proof manufacturing capabilities by prioritizing opportunities for process optimization, ensuring that every decision made is grounded in the reality of the shop floor.
To continue reading this article, which originally appeared in the November 2024 issue of SMT007 Magazine, click here.
Testimonial
"We’re proud to call I-Connect007 a trusted partner. Their innovative approach and industry insight made our podcast collaboration a success by connecting us with the right audience and delivering real results."
Julia McCaffrey - NCAB GroupSuggested Items
Walt Custer: Making Data Interesting
09/03/2025 | Andy Shaughnessy, I-Connect007I just learned that IPC Hall of Famer Walt Custer has passed away at 81. I first met Walt about 20 years ago when I started covering the fabrication industry. Right away, he started telling me which companies to watch and which trends to follow. This was in the years following 9/11, and things were still pretty fluid.
Altus Supports Datalink Electronics with Advanced Selective Soldering Solution to Boost Manufacturing Efficiency
09/02/2025 | Altus GroupDatalink Electronics has partnered with Altus Group to integrate a cutting-edge automated soldering solution, enhancing its production capabilities and reinforcing its strategic focus on quality, automation, and scalability.
Wisdom From Data-center Power Pioneer Mike Mosman
09/02/2025 | Barry Matties, I-Connect007Few engineers have moved the levers of modern electronics more decisively than Mike Mosman. From the pre-email computer rooms of the 1980s to today’s hyperscale campuses cranking out AI cycles, the retired power engineer and co-founder of CCG Facilities Integration has spent four decades proving that uptime is a design discipline, not a hope.
HPE Accelerates Self-driving Network Operations with New Mist Agentic AI-native Innovations
08/26/2025 | BUSINESS WIREHPE announced major innovations to its HPE Juniper Networking portfolio, advancing its AI-native Mist platform to deliver agentic AIOps through more autonomous, intelligent and proactive network operations.
Macronix Introduces Cutting-Edge Secure-Boot NOR Flash Memory
08/08/2025 | PRNewswireMacronix International Co., Ltd., a leading integrated device manufacturer in the non-volatile memory (NVM) market, announced ArmorBoot MX76, a robust NOR flash memory combining in a single device, the essential performance and an array of security features that deliver rapid boot times and iron-clad data protection.