-
- News
- Books
Featured Books
- smt007 Magazine
Latest Issues
Current IssueWhat's Your Sweet Spot?
Are you in a niche that’s growing or shrinking? Is it time to reassess and refocus? We spotlight companies thriving by redefining or reinforcing their niche. What are their insights?
Moving Forward With Confidence
In this issue, we focus on sales and quoting, workforce training, new IPC leadership in the U.S. and Canada, the effects of tariffs, CFX standards, and much more—all designed to provide perspective as you move through the cloud bank of today's shifting economic market.
Intelligent Test and Inspection
Are you ready to explore the cutting-edge advancements shaping the electronics manufacturing industry? The May 2025 issue of SMT007 Magazine is packed with insights, innovations, and expert perspectives that you won’t want to miss.
- Articles
- Columns
- Links
- Media kit
||| MENU - smt007 Magazine
Estimated reading time: 4 minutes
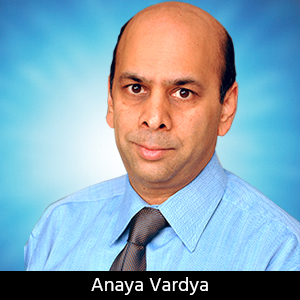
Standard of Excellence: Hiring for Quality Positions in Manufacturing, Engineering, and Management
In continuing my series on finding, signing, and keeping good people for your company, this month we discuss hiring good people for your quality department. Even when hiring was easier, hiring for the quality department has always been especially challenging. It takes a special kind of person: someone with attention to detail, someone ready to stand for his or her convictions, and someone who can stand up under pressure when the company needs to ship product and the quality manager refuses to because it is not up to par. The quality department is the very soul of any manufacturing company.
Accordingly, the manufacturing quality sector is vital to ensuring that products meet the highest standards of excellence. However, hiring the right individuals for these positions and developing their career paths to become quality engineers and managers can be challenging. In my experience, several strategies can help you build a strong team that will ensure your manufacturing processes are top-notch.
When hiring for manufacturing quality positions, it’s important to identify the key competencies required for the role. These typically include attention to detail, analytical thinking, problem-solving skills, and a strong understanding of manufacturing processes.
Look for candidates who have demonstrated these competencies in previous roles, even if they haven’t worked in a formal quality position before. For example, someone with experience in a production role may have developed a keen eye for detail that could be highly valuable in a quality position.
While theoretical knowledge is important, hands-on experience in a manufacturing environment is often critical for quality roles. Candidates who have worked on the production floor or who have been involved in process improvements will have a better understanding of the challenges and opportunities in manufacturing quality.
When evaluating candidates, prioritize those who have direct experience with the types of products and processes your company uses. This experience will allow them to hit the ground running and make immediate contributions to your quality efforts.
One key to retaining quality talent is providing clear career development paths. Employees want to know that they have opportunities for growth and advancement. When hiring for entry-level quality positions, make it clear that there is a path to becoming a quality engineer or manager. This can include offering training programs, mentorship opportunities, and regular performance reviews. For example, you might offer a training program that allows employees to learn new skills and take on more responsibilities over time.
Mentorship is a powerful tool for developing talent. Pairing new hires with experienced quality engineers or managers can provide them with the guidance and support they need to succeed.
On-the-job training is also critical. Allow new hires to learn by having them gradually take on more complex tasks as they gain experience. This hands-on approach helps them build the skills and confidence needed to excel in their positions.
Quality is all about continuous improvement. Encourage your employees to always look for ways to improve processes, reduce defects, and enhance product quality. Your company culture should instill this mindset from the moment a new hire joins your team. One way to do this is by involving employees in quality improvement projects. Allow them to contribute ideas and take ownership of initiatives that can have a real impact on the company’s performance. This not only improves quality but also helps employees develop the skills and experience needed to advance in their careers.
Recognition and rewards are important for motivating employees and encouraging them to strive for excellence. When employees achieve quality milestones or make significant contributions to the team, be sure to recognize their efforts. Companies can do this through formal recognition programs, bonuses, or simply saying “thank you.” Furthermore, provide opportunities for further growth by offering promotions or additional responsibilities to those who consistently perform at a high level.
Quality is not the responsibility of one person or department. It’s a team effort. Fostering a collaborative environment where employees work together to achieve quality goals is essential. Encourage communication and collaboration between different departments, such as production, engineering, and quality assurance. This collaboration helps to ensure that everyone is on the same page and working toward the same objectives. It also provides opportunities for employees to learn from each other and develop a deeper understanding of the entire manufacturing process.
Hiring for manufacturing quality positions and developing career paths for quality engineers and managers requires a strategic approach. By identifying key competencies, prioritizing hands-on experience, providing clear career paths, offering mentorship and on-the-job training, encouraging continuous improvement, rewarding success, and fostering collaboration, you can build a strong quality team that will ensure your manufacturing processes meet the highest standards of excellence. With the right team in place, you’ll be well-positioned to achieve your company’s quality goals and drive long-term success.
Anaya Vardya is president and CEO of American Standard Circuits; co-author of The Printed Circuit Designer’s Guide to… Fundamentals of RF/Microwave PCBs and Flex and Rigid-Flex Fundamentals. He is the author of The Printed Circuit Designer's Guide to DFM Essentials, Thermal Management: A Fabricator's Perspective and The Companion Guide to Flex and Rigid-Flex Fundamentals .Visit I-007eBooks.com to download these and other free, educational titles.
More Columns from Standard of Excellence
Standard of Excellence: Delivering Excellence—A Daily GoalStandard of Excellence: The Role of Technology in Enhancing the Customer Experience
Standard of Excellence: Turning Negative Customer Feedback Into Positive Outcomes
Standard of Excellence: Anticipating Customer Needs Early and Often
Standard of Excellence: The Power of Personalization in Customer Care
Standard of Excellence: Building Trust with Customers—The Foundation of Excellent Service
Standard of Excellence: Finding and Developing Future Leaders in Manufacturing
Standard of Excellence: Finding and Hiring the Right Candidates for Engineering Positions