Estimated reading time: 10 minutes
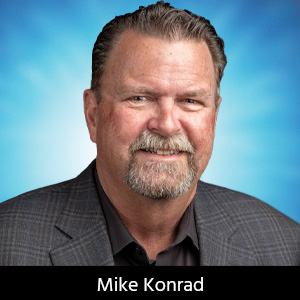
The Knowledge Base: The Impact of Harsh Environments on Residue Tolerance
Electronic devices are ubiquitous, performing critical functions in a wide range of applications, from consumer electronics to aerospace, medical devices, automotive systems, and industrial control systems. Many of these devices operate in harsh environments characterized by extremes in temperature, humidity, pollution, and chemical exposure.
While advances in electronics design and manufacturing have vastly improved reliability and performance, the challenges posed by these conditions have driven an increasing focus on one key factor: contamination (particularly ionic residue) on circuit assemblies. In these harsh environments, even small amounts of contamination can have significant consequences, notably the increased risk of electrochemical migration (ECM).
I’ll explore how harsh environments reduce the tolerance for residue on circuit assemblies, thereby exacerbating the risk of ECM, a failure mode that threatens the reliability of electronic systems.
Understanding Residue in Circuit Assemblies
In the manufacture of printed circuit assemblies (PCAs), the reflow soldering process is often accompanied by the presence of residues. These residues can arise from fluxes, solder pastes, adhesives, and various chemicals used throughout the board fabrication and assembly processes. Residues may be ionic or non-ionic, and their composition can vary based on the specific materials and processes employed.
Ionic residues, which include salts, acids, flux activators, and other conductive materials, are of particular concern. Under normal conditions, these residues may not immediately compromise the functionality of a circuit assembly. However, when exposed to moisture or high humidity, ionic residues can dissolve in the water layer that forms on the surface of the assembly, creating conductive pathways. This sets the stage for electrochemical migration, a phenomenon where metal ions are transported across the surface of the circuit board, leading to the formation of dendrites—tiny, tree-like structures of metal that grow over time and can ultimately cause electrical shorts between conductors.
The Role of Harsh Environments
Harsh environments exacerbate the risk posed by residues on circuit assemblies in several ways. High levels of humidity, extreme temperatures, and exposure to corrosive gases, pollutants, and other environmental stressors reduce the tolerance for contamination on the surface of PCAs. As the severity of environmental conditions increases, even minimal levels of residue that might have been acceptable in benign environments can become a significant reliability risk.
Humidity and Moisture
Humidity plays a central role in electrochemical migration. In environments with high relative humidity, moisture readily condenses on the surface of circuit assemblies, dissolving ionic residues into a conductive electrolyte. This dissolved solution of ions provides a medium through which electrical current can flow, accelerating the migration of metal ions from one conductor to another. With sufficient voltage across the gap between conductors, dendrite formation is initiated, creating the risk of short circuits.
The presence of hygroscopic residues, which absorb moisture from the air, worsens this problem. Even in environments with moderate humidity, hygroscopic residues can attract and retain moisture, further increasing the likelihood of electrochemical migration. In critical applications where system failure could lead to catastrophic consequences—such as aerospace or automotive safety systems—the presence of moisture-induced ECM is intolerable. As a result, stringent cleaning processes or alternative flux chemistries are often required to minimize residue levels and mitigate this risk.
Temperature Extremes
High temperatures accelerate chemical reactions, and this holds true for the formation of dendrites in electrochemical migration. When exposed to elevated temperatures, residues on circuit assemblies can degrade, releasing ionic species that further promote ECM. Conversely, low temperatures can lead to the condensation of moisture on cold surfaces, amplifying the effects of high humidity. The thermal cycling common in many harsh environments, such as electronics used in aerospace applications where electronic devices are repeatedly exposed to alternating high and low temperatures, places additional stress on the integrity of circuit assemblies. These conditions can cause residues to migrate and redistribute across the surface of the assembly, increasing the likelihood of ECM over time.
Additionally, the combination of high temperature and humidity—often referred to as "tropical" environments—poses an especially severe risk. Under these conditions, the synergy between moisture and heat accelerates the growth of dendrites, reducing the time to failure.
Corrosive Gases and Pollutants
In industrial, automotive, and urban environments, electronic devices may be exposed to corrosive gases such as sulfur dioxide (SO₂), nitrogen dioxide (NO₂), and hydrogen sulfide (H₂S), as well as airborne contaminants like dust and particulate matter. These substances can interact with residues on circuit assemblies, increasing their ionic conductivity and promoting the formation of dendrites. In particular, sulfur-based compounds are notorious for their corrosive effects on metals commonly used in PCB manufacturing, like silver, copper, and lead. The corrosive action of these gases can introduce new ionic species or exacerbate the degradation of existing residues, further heightening the risk of electrochemical migration.
Corrosive pollutants can also damage the protective coatings (conformal coatings) that are often applied to circuit assemblies to shield them from environmental exposure. Once these barriers are compromised, residues and contaminants become more vulnerable to environmental stressors, leading to increased ECM susceptibility.
Case Studies in Harsh Environment Failures
Documented failures of electronic systems in harsh environments illustrate the critical importance of residue management in mitigating ECM. One high-profile case occurred in the automotive industry, where electronic control units (ECUs) were exposed to high humidity and sulfur-containing gases during operation. The combination of these environmental factors, coupled with insufficient cleaning of the circuit assemblies, resulted in electrochemical migration, leading to intermittent failures in the vehicle's electronic systems. The cost of these failures was significant, both in terms of warranty repairs and reputational damage to the manufacturer.
In another example, a telecommunications infrastructure in a coastal environment suffered from corrosion-related ECM failures. Salt in the air combined with the high humidity and high temperatures of the coastal region to create ideal conditions for dendrite growth. Over time, failures in the equipment caused significant service disruptions, prompting a costly retrofit of the affected systems with better cleaning processes and protective coatings.
Even in environments where the humidity levels are moderate, ECM can occur. A major video game manufacturer experienced this firsthand. The game console’s motherboard design featured densely packed components, with small traces and vias vulnerable to the effects of ionic contamination. The lead-free solder used in the assemblies was highly susceptible to forming conductive paths when exposed to moisture. Reports indicated that ECM caused dendrite formation between the power and ground planes, leading to short circuits and intermittent failures in some units.
The problem was exacerbated by the console’s thermal design, which allowed significant heat buildup during use. As the console cooled down, condensation could form, further promoting the conditions necessary for ECM to occur.
These cases demonstrate the vulnerability of electronic systems operating in harsh environments and the critical need for proactive measures to mitigate the risks associated with residue and electrochemical migration.
The Impact of Miniaturization on Residue Tolerance
The trend toward miniaturization in electronics has significantly compounded the challenges associated with residues on circuit assemblies. As electronic devices shrink, the spacing between conductive elements, such as traces and pads, becomes smaller, often approaching micrometer scales. This reduction in spacing lowers the voltage threshold required for electrochemical migration to occur. Smaller distances between conductive elements provide less physical room for insulating barriers, meaning that even tiny amounts of residue can bridge these gaps and form conductive pathways, leading to increased susceptibility to electrochemical migration. As a result, the tolerance for any form of contamination, particularly ionic residues, has decreased dramatically. Even residues that might have been inconsequential in larger, more widely spaced circuits can pose severe risks in miniaturized assemblies, where the smaller dimensions amplify the potential for failure.
Furthermore, miniaturization has introduced new challenges in cleaning and residue removal. Low-standoff components—those with very little clearance between the component body and the PCB—are now commonly used in compact designs, making it more challenging for cleaning agents to penetrate under these components and remove contaminants effectively. Traditional cleaning methods, such as non-diffused or coherent nozzles, are often ineffective in reaching the narrow spaces under low-standoff components, leading to the risk of residual contamination being left behind. Advanced cleaning techniques, including diffused spray patterns and chemical additives that reduce surface tension, have become essential to ensure thorough cleaning in miniaturized assemblies. However, even with these advancements, the reduced tolerances in miniaturized designs mean that the margin for error is exceedingly small, requiring strict control over both manufacturing processes and post-reflow cleaning procedures to prevent residue-related failures like electrochemical migration.
Reducing Residue Tolerance: Best Practices
As the tolerance for residues diminishes in harsh environments, manufacturers must adopt rigorous practices to minimize contamination on circuit assemblies. These practices include thorough cleaning processes, careful material selection, and enhanced testing protocols.
Cleaning Processes
Effective cleaning is one of the most critical steps in reducing the risk of electrochemical migration. Cleaning processes must be optimized to remove not only visible residues but also microscopic and ionic contaminants that can contribute to ECM under harsh environmental conditions. Techniques such as aqueous cleaning, using a combination of deionized water and cleaning agents, have proven effective at removing ionic residues. Advanced cleaning systems that incorporate real-time monitoring of resistivity in the rinse water allow for precise control over the cleanliness of assemblies and ensure that contamination is reduced to acceptable levels.
In environments with very low residue tolerance, even "no-clean" fluxes—which are designed to leave behind benign residues—may not be acceptable, as these residues can still absorb moisture or interact with pollutants to create conductive pathways. In such cases, cleaning may be required despite the use of low-residue flux chemistries.
Material Selection
The choice of materials used in circuit assembly can also play a key role in minimizing residue-related risks. For instance, selecting fluxes and solder pastes with low ionic content can significantly reduce the amount of conductive contamination left behind after reflow. Similarly, the use of conformal coatings to protect against environmental exposure can provide an additional layer of defense, preventing residues from interacting with harmful pollutants. While most conformal coating materials are permeable, allowing small amounts of moisture to permeate through the membrane-like material, they can reduce, though not eliminate, the amount of moisture exposed to the surface of the assembly. However, the proverbial “fly in the ointment” is the fact that manufacturers of conformal coating materials recommend a thorough cleaning process prior to the application of conformal coating. If one embraces the rationale of conformal coating to avoid cleaning, this creates a circular logic event.
In addition, certain materials used in the manufacturing process, such as adhesives and potting compounds, must be chosen for their resistance to moisture absorption and ionic contamination.
Testing and Monitoring
Testing for ionic contamination has become a critical part of the quality assurance process in circuit assembly, particularly for applications exposed to harsh environments. Current IPC standards now mandate an objective evidence protocol to assess the cleanliness of circuit assemblies. Surface insulation resistance (SIR) testing under heat and humidity conditions is now required to generate objective evidence that the assembly will not fail when exposed to harsh environments. The ROSE (resistivity of solvent extract) test, which measures the conductivity of solvent extracts from a circuit assembly, is widely used to assess the level of ionic residues. IPC now requires ionic contamination testing on production assemblies as a process monitoring protocol.
Conclusion
As electronic devices operate in increasingly harsh environments, the tolerance for contamination on circuit assemblies becomes ever more critical. Humidity, temperature extremes, corrosive gases, and pollutants all contribute to the risk of electrochemical migration, particularly in the presence of ionic residues. In these conditions, even minimal levels of contamination can lead to the formation of conductive pathways and dendritic growth, resulting in catastrophic system failures.
The reducing tolerance for residues on circuit assemblies requires a multifaceted approach, including advanced cleaning processes, careful material selection, and rigorous testing and monitoring. As the demands on electronics reliability continue to grow, particularly in safety-critical industries, the ability to manage residue and mitigate the risks of electrochemical migration will be paramount to ensuring the long-term performance and reliability of electronic systems.
By understanding the interplay between harsh environments and residue tolerance, manufacturers can take proactive steps to safeguard their products against the risks of ECM and maintain their competitive edge in a rapidly evolving industry.
This column originally appeared in the November 2024 issue of SMT007 Magazine.
More Columns from The Knowledge Base
The Knowledge Base: Building the Workforce of Tomorrow With EMACThe Knowledge Base: Beyond the Badge—Why Membership Matters More Than Ever
The Knowledge Base: Unlocking the Invisible—The Critical Role of X-ray Technology
The Knowledge Base: At the Forefront of Electronics Manufacturing
The Knowledge Base: Challenges and Considerations of Harsh Environments
The Knowledge Base: My 2025 Industry Wish List
The Knowledge Base: The Era of Advanced Packaging
The Knowledge Base: The Pivotal Role of Solder Paste