-
- News
- Books
Featured Books
- smt007 Magazine
Latest Issues
Current IssueSpotlight on India
We invite you on a virtual tour of India’s thriving ecosystem, guided by the Global Electronics Association’s India office staff, who share their insights into the region’s growth and opportunities.
Supply Chain Strategies
A successful brand is built on strong customer relationships—anchored by a well-orchestrated supply chain at its core. This month, we look at how managing your supply chain directly influences customer perception.
What's Your Sweet Spot?
Are you in a niche that’s growing or shrinking? Is it time to reassess and refocus? We spotlight companies thriving by redefining or reinforcing their niche. What are their insights?
- Articles
- Columns
- Links
- Media kit
||| MENU - smt007 Magazine
Estimated reading time: 5 minutes
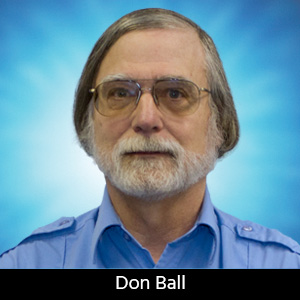
The Chemical Connection: Getting the Best from Your Cupric Chloride Etchant
Over the past several months, we have received a lot of questions from our customers about cupric chloride etching—mostly about how to improve etch quality, but also about process problems. Most of them were easily dealt with, but the questions arose because the people involved in running the etching process were not aware of the finer nuances involved in using cupric chloride as the primary etchant. (They don’t have courses on etching in most colleges and trade schools.) I thought this might be a good time to summarize some things I have learned in my 50 years of experience with cupric chloride etching and clear up some of the confusion.
When I started in the industry (1974), the mantra was speed, speed, speed. The main goal was the ability to process as many square feet of product as possible in the shortest amount of time. State-of-the-art was 10-mil (250 µm) lines and spaces and double-sided panels, so etch quality was not of prime importance. The etched lines just had to carry the proper amount of current with enough space between them to prevent shorts and crosstalk. Chemistry-wise, the best etch rate was attained at a specific gravity of 32°Be (1.283 sg) or about 24% cupric chloride. The freer the acid, the faster the etch rate, so a lot of people then ran their cupric at 32°Be, with free acid levels of up to 2N and some as high as 3N.
By etch quality, I am talking about etch factors or straightness of sidewalls. Cupric chloride generally etches 1 unit sideways for every three units down. This means that if you are attempting to etch a 3-mil (75 µm) line in 1-ounce (35 µm) foil, you would measure about 2.5 mils (64 µm) across the top of the line when the bottom of the line reaches its finished etch width of 3 mils (75 µm). Reducing the amount of sideways etch will give a wider measurement across the top of the line and a better etch quality. Perfection would be measuring 3 mils (75 µm) across the top of the line when you measure 3 mils (75 µm) across the bottom.
Those carefree days are long gone (although they didn’t seem so carefree at the time). Lines and spaces, and specifications have become much tighter, and improving etch quality by reducing sideways etch has become paramount. We did one of our best projects in the mid-’90s with a manufacturer of lead frames who was pushing the limits of finger spacing and finger widths in 6-mil (150 µm) copper etched from both sides. We considered every variable in the chemistry and etching equipment that might affect the sideways etch, and we incorporated them into a complicated design of experiment (DOE) with 32 separate tests. The advantage of the DOE method is that it allows the simultaneous testing of several variables. Then, using statistical methods, it is possible to determine which variables have the most effect on the process being studied. The chemical variables we studied included etchant specific gravity, etchant temperature, free acid level, and oxidation/reduction potential (ORP). Equipment variables included spray pressure, type of nozzles (fan or cone), nozzle height, nozzle flow rate, and oscillation (yes or no). Finally, we included a test with different panel widths.
It took a few months to run all 32 tests twice, but the results were conclusive: The variables that had the largest effect on sideways etch were the free acid level followed closely by the specific gravity. The rest of the variables tested had only minor effects and were not worth the effort to test further. It may surprise some to learn that fan and cone nozzles did not have a statistical difference in their effect on sideways etch.
Tests were then run on specific gravities of between 28–40°Be (1.24-1.38 sg). As the specific gravity increased, the etch rate slowly decreased until reaching 36°Be (1.33 sg), after which the etch rate began to drop significantly. The rate of sideways etch also slowly decreased (which is what we want), until, again, the specific gravity reached 36°Be, when the rate of decrease also began to drop significantly. Once the specific gravity reaches 36°Be, the reduction in sideways etch becomes insignificant compared to the loss in productivity caused by the significant decrease in etch rate, even in low-productivity environments.
Therefore, I usually recommend a specific gravity of 36°Be for cupric chloride for the best etch rate and quality.
The free acid level had the largest effect on sideways etch, with less sideways etch as the free acid level decreased, but so did the etch rate. It appears to be a given that anything done to decrease sideways etch also lowers the etch rate. Testing has shown the lowest sideways etch occurs at around 0.8N. Free acid levels below this become hard to control and don’t improve the etch quality that much.
I usually recommend running the cupric chloride etchant at a specific gravity of 36°Be and a free acid level of 0.8N for the best etch quality. There is an etch rate penalty for this, however. The etch rate for a cupric etch bath running at 32oBe and 1N free acid is usually around 1.2 to 1.3 mils/min (30.5 to 33 µm/min) as opposed to 1 mil/min (25.4 µm/min) for a bath running at 36°Be and 0.8N free acid level.
There is one potential process problem while running at low acid levels that was recently brought to my attention: losing control and finding that there is no free acid left. One function of free acid is to keep the cuprous chloride byproduct of the etch reaction in solution. It is not very soluble in water and precipitates out of solution when the acid level gets too low. This will affect your ORP readings since they indicate the ratio of cupric ions to cuprous ions. If the cuprous ions precipitate out of solution, then the ORP reading will be inaccurate, and your etch bath will stop etching. The signs of this are the color of the etchant changing from dark jade to neon green and your ORP readings going to 900+ mv but with no chlorine odor. Fortunately, adding acid back to the bath (and a lot more than you think) will bring the bath back to normal.
Hopefully, this will help answer some questions that come up about the best operating conditions for achieving the highest cupric chloride etch quality under production conditions.
This column originally appeared in the November 2024 issue of PCB007 Magazine.
More Columns from The Chemical Connection
The Chemical Connection: Experience and Wisdom Gained by Doing BusinessThe Chemical Connection: Sales Organization from a Capital Equipment Perspective
The Chemical Connection: Through-glass Vias in Glass Substrates
The Chemical Connection: Reducing Defects in Circuit Board Production
The Chemical Connection: Common Misconceptions in Wet Processing
The Chemical Connection: Surface Finishes for PCBs
The Chemical Connection: Earthquakes, Astronauts, and Aquatics—A Lighter Look at the Past
The Chemical Connection: Better Fabs Attract a Better Workforce