-
- News
- Books
Featured Books
- design007 Magazine
Latest Issues
Current IssueShowing Some Constraint
A strong design constraint strategy carefully balances a wide range of electrical and manufacturing trade-offs. This month, we explore the key requirements, common challenges, and best practices behind building an effective constraint strategy.
All About That Route
Most designers favor manual routing, but today's interactive autorouters may be changing designers' minds by allowing users more direct control. In this issue, our expert contributors discuss a variety of manual and autorouting strategies.
Creating the Ideal Data Package
Why is it so difficult to create the ideal data package? Many of these simple errors can be alleviated by paying attention to detail—and knowing what issues to look out for. So, this month, our experts weigh in on the best practices for creating the ideal design data package for your design.
- Articles
- Columns
- Links
- Media kit
||| MENU - design007 Magazine
Sayonara to the Last Standing Copper Foil Plant in North America
December 17, 2024 | Marcy LaRont, I-Connect007Estimated reading time: 4 minutes
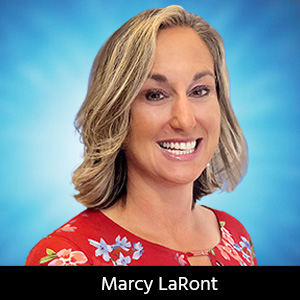
In July 2021, PCB007 Magazine published an interview with Michael Coll and Chris Stevens of Nippon Denkai about the new acquisition by Nippon Denkai of the last-standing ED foil manufacturer in North America. The plant in Augusta, Georgia, was formerly owned by Oak Mitsui, Inc. and had been purchased by Nippon Denkai the previous March, after which significant investment was made with the expectation of providing more jobs.
Many COVID-related shutdowns were still in effect. Copper prices were soaring, as was demand in the wake of the need for lithium-ion batteries for electric cars and massive projections for their growth. Copper foil suppliers for the PCB industry were working to allocate their supply between the PCB and EV industries.
The demand for copper was not isolated to just electronics. When asked about the pressure to supply industries outside of electronics, Chris Stevens responded, “As the only ED foil manufacturer in North America, we really feel that we have an obligation to the PCB market, which we have been supplying for over 40 years. We are spec’d into a lot of military, defense, and aerospace applications, and we know it is critical to continue supporting this business.”
It’s now the end of 2024 and the bottom has apparently fallen out. Nippon Denkai Ltd., plagued with financial difficulties reported to have been caused in part by the semiconductor shortage, a decline in the demand for smartphones, the enforcement of the U.S. Inflation Reduction Act, and the financial fallout from COVID amidst ever-increasing copper prices, recently filed for bankruptcy and civil rehabilitation proceedings. The company is dissolving its U.S. holdings and has announced the closure of the copper foil manufacturing plant in Georgia.
It is rarely a straight line to bankruptcy for any business and Nippon Denkai is no exception. Though the myriads of very real market challenges certainly adversely affected their business holdings, rarely are only market factors to blame for an organization’s financial demise, especially when that organization was positioned to capitalize on ridiculous market demand which should have more than made up for the high price of copper.
Poor decisions and organizational management may have played a part.
Nevertheless, the U.S. is now faced with the closure of the last standing copper foil manufacturing plant in North America serving the PCB fabrication industry and supporting many U.S. military and defense products.
How much will this matter? It will undoubtedly cause a ripple within the supply chain, mostly around the timing of negotiating new agreements with overseas copper foil suppliers and management of production output.
But amidst the backdrop of the CHIPS Act, and the drive to rebuild American manufacturing and secure the supply chain for products and applications that could put U.S. security at risk, the closure of this last U.S. plant right now feels a bit hard to believe. Who was minding the store? With all the government’s financial awards and strong statements of support for stateside electronics manufacturing, this certainly looks terrible. So, should the U.S. government step in and purchase the asset from Nippon Denkai, perhaps as part of the massive investment for the Printed Circuit Board Market Catalyst program?
American manufacturers and business owners who are already on tenterhooks about the future of American manufacturing and their role in it are wondering whether the government’s slow pace and inability to focus on anything but what is immediately in front of them makes them incapable of recognizing potentially important opportunities as they arise, even if largely symbolic, let alone taking advantage of them.
“We regret that our colleagues at Denkai are facing this situation,” said David Schild, executive director of the Printed Circuit Board Association of America. “Single points of failure in the microelectronic supply chain will have consequences for PCB manufacturers and related industries. With no more U.S. copper foil vendors, PCB manufacturers will have to qualify other vendors or find alternative materials. This will likely disrupt delivery of certain DoD programs of record as well as commercial customers supporting the nation’s critical infrastructure. DoD Industrial Base Policy needs to double down on domestic single-source/single-point failures in the microelectronics supply chain.”
If you are angry or frustrated at this news, I encourage you to reach out to your legislative representative, and advocacy groups like PCBAA and IPC.Visit them in Washington, D.C., and invite them to your site. They usually welcome the opportunity to visit with their constituents as a way to show they support business in their states. Advocacy staff at both IPC and PCBAA will help you do this.
This is the power we have collectively. It might be the only power we have left. No one is too small to get involved. No one’s business is unimportant. Don’t leave all the heavy lifting to the big guys who already work in advocacy. With something as important as this, it’s time to get involved. Don’t make excuses. Do more. Do something. The time is now, because it may be all that we have.
Today, we say “sayonara” to copper foil manufacturing in the U.S. and to the jobs attached to it. It feels a little like coal in our stockings, so here’s to better things in 2025 and beyond.
Testimonial
"The I-Connect007 team is outstanding—kind, responsive, and a true marketing partner. Their design team created fresh, eye-catching ads, and their editorial support polished our content to let our brand shine. Thank you all! "
Sweeney Ng - CEE PCBSuggested Items
Statement from the Global Electronics Association on the July 2025 Tariff on Copper Foil and Electronics-Grade Copper Inputs
07/31/2025 | Global Electronics AssociationWe are disappointed by today’s decision to impose a 50% tariff on imported copper foil and other essential materials critical to electronics manufacturing in the United States.
Considering the Future of Impending Copper Tariffs
07/30/2025 | I-Connect007 Editorial TeamThe Global Electronics Association is alerting industry members that a potential 50% tariff on copper could hit U.S. electronics manufacturers where it hurts.
Connect the Dots: Sequential Lamination in HDI PCB Manufacturing
07/31/2025 | Matt Stevenson -- Column: Connect the DotsAs HDI technology becomes mainstream in high-speed and miniaturized electronics, understanding the PCB manufacturing process can help PCB design engineers create successful, cost-effective designs using advanced technologies. Designs that incorporate blind and buried vias, boards with space constraints, sensitive signal integrity requirements, or internal heat dissipation concerns are often candidates for HDI technology and usually require sequential lamination to satisfy the requirements.
OKI Launches Rigid-Flex PCBs with Embedded Copper Coins Featuring Improved Heat Dissipation for Space Equipment Applications
07/29/2025 | BUSINESS WIREOKI Circuit Technology, the OKI Group’s printed circuit board (PCB) business company, has developed rigid-flex PCBs with embedded copper coins that offer improved heat dissipation for use in rockets and satellite-mounted equipment operating in vacuum environments.
Designers Notebook: Basic PCB Planning Criteria—Establishing Design Constraints
07/22/2025 | Vern Solberg -- Column: Designer's NotebookPrinted circuit board development flows more smoothly when all critical issues are predefined and understood from the start. As a basic planning strategy, the designer must first consider the product performance criteria, then determine the specific industry standards or specifications that the product must meet. Planning also includes a review of all significant issues that may affect the product’s manufacture, performance, reliability, overall quality, and safety.