Estimated reading time: 8 minutes
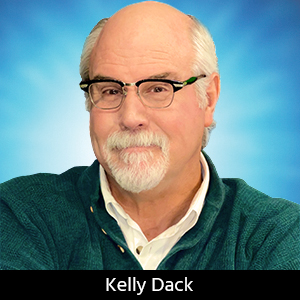
Contact Columnist Form
Target Condition: Advanced Packaging Technologies—Look Before You Leap
Every so often, I’m disappointed by a high expectation that didn’t work out. Some of these disappointments in the PCB design and manufacturing industry have been related to “new and advanced” PCB design products or services which proved to be impracticable for too many PCB designers (including me).
Often, my unmet expectations have involved automated or next-generation PCB layout software products that show well within the confines of a canned trade show presentation but fail miserably when applied in a real-life design. Over the years, I’ve been awed by “disruptive” technologies, products, or services only to realize I’d been reeled in by a slick, hyped-up sales and marketing presentation. I would find that the advanced technology was still in a development phase or so specialized that it was hardly executable within the scale of my workflow, and the sales team dropped me like a hot potato once they realized my production budget didn’t exist above the stratosphere.
Understanding Marketing Hype
However, just because a technology is advanced doesn’t mean it is right for your project. How many electronics engineers found this out after the 01005 chips came out? “Wow, smaller must be better,” they said. Yet some eagerly placed them in strategic areas of their layouts only to find very few suppliers with assembly equipment capable of placing or inspecting them. Even the “larger” 0201-sized chips are still considered advanced packaging by some EMS suppliers. They continue to cause headaches and lower profit margins due to processing issues relating to their scale.
On another front, how are those advanced, automated PCB DFM-checking tools working for us when we don’t even know the capabilities of the suppliers who will build the boards? Why is it so easy for an experienced manufacturing engineer to catch glaring DFM issues on a design after the CAM data has been run through an automated audit? As an EMS stakeholder who liaises between PCB design and global manufacturing suppliers, I can tell you that there is still much room for improvement. Supplier requests for DFM changes for outside designs continue nonstop.
Regarding using AI to design and lay out a circuit board, it’s not that it can’t happen. But I’ve learned that I need to be in touch with the context of feasibility when considering the implementation of something so advanced. Before redirecting any of my time or resources away from a workflow paradigm for which the wheels are already well-greased, I must be certain of the advantages. In sales and marketing, adding “advanced” to your products or capabilities can get them more attention. Potential customers will presume they must be “better” while still offering availability and manufacturability, though maybe with a higher price tag.
As cliché as it sounds, “cutting edge” has traditionally indicated a condition better than advanced; the product or service slices through all the peripheral BS. It implies direct contact and exposure to a problem at hand so a definitive solution can be implemented. As most of us know, when the marketing hype reaches “bleeding edge” status, there is at least an admission from the technology marketers that the product or service may hurt until fully implemented.
Deep-pocketed visionaries who can afford to bleed for a while get in early on, but this class of advancement can be risky. There is no guarantee that competitors won’t have caught up, even after the initial wounds heal and the process smooths out.
Understanding the Technology Development Hype Phases
If you are an informed, DFM-savvy PCB designer or engineer considering advanced technology, you must understand what happens throughout the development phases of a product or service. The Gartner hype cycle1 depicts the five phases of maturity for emerging technologies. Gartner Inc. actively tracks technologies to examine and report on their advancements using graphic milestones. This chart concept is an effective tool for the PCB design and manufacturing industries to evaluate which phase of an advanced technology makes the most sense to dive in.
The Gartner Hype Cycle: Breaking Down the Phases
Let’s examine the chart and see if we can relate to some of the common ups and downs many engineering groups experience when developing their own advanced solutions or trying to implement others from outside.
1. Innovation (Technology) Trigger
“A potential technology breakthrough kicks things off. Early proof-of-concept stories and media interest trigger significant publicity. Often no usable products exist and commercial viability is unproven.”1
This initial phase could come about as a noble challenge, like the day that JFK announced America would land a man on the moon. Innovation can be triggered by a change in technology, like a new chipset, or more capability packed into a less expensive part. Sometimes, a project launches to solve an immediate need during a world crisis, like when the Open Source Ventilator project was formed to quickly address the need for ventilators during the pandemic.2
Building a team to respond to an innovation trigger and then engage in a full-blown project is not for the faint of heart. At this stage, information and decision-making move fast. The concept involves unknown risks and no guarantee of success or reward.
2. Peak of Inflated Expectations
“Early publicity produces a number of success stories—often accompanied by scores of failures. Some companies take action; most do not.”1
Once news breaks of a new advanced product or service, a sales and marketing team will most certainly become involved. Often before the idea is developed and proven, publicity has been generated and investors are being solicited. This is the high point in a project in which hyped expectations have not been vetted against solid application, and a PCB designer obtains that new limited capability demo software to try out. It’s also when product or service development begins shaking hands with real users.
3. Trough of Disillusionment
“Interest wanes as experiments and implementations fail to deliver. Producers of the technology shake out or fail. Investment continues only if the surviving providers improve their products to the satisfaction of early adopters.”1
Both innovators and customers find themselves crashing and burning into the trough of disillusionment from time to time. At the bottom of the trough there is a bright adage attributed to author John C. Maxwell: “Fail early, fail often, but always fail forward.” This quote appears to have been adopted by some Silicon Valley startups, morphing into the more familiar “fail fast, fail often” meme most PCB industry development folks are familiar with. Continuing from here will require more investment and more time. Will it be worth it?
4. Slope of Enlightenment
“More instances of the technology's benefits start to crystallize and become more widely understood. Second- and third-generation products appear from technology providers. More enterprises fund pilots; conservative companies remain cautious.”1
If it is determined that the rewards can still exceed the risks, much can be gained from leveraging experience and feedback data collected from all the failures experienced during previous phases. Think of how many rockets exploded or crashed before SpaceX was successful in landing a reusable booster stage. New technology and ideas—successes and failures—make valuable reference points to gauge applicability over time. It may be during this advanced phase of a product or service timeline that an engineer with only a sub-stratosphere limited budget begins adopting a technology, as it appears to be the best place to jump in before the competition does.
5. Plateau of Productivity
“Mainstream adoption starts to take off. Criteria for assessing provider viability are more clearly defined. The technology's broad market applicability and relevance are clearly paying off. If the technology has more than a niche market, then it will continue to grow.”1
We are all familiar with and use products and services that have long resided on the plateau of productivity. They have been there so long that we no longer refer to them as advanced—though once they were. We take for granted the ease at which we can order or design around this basic, proven technology.
For instance, glass-epoxy materials have been around for more than a half-century. It is still the go-to laminate for more than 80% of the PCB designs in the world. Will it ever be widely displaced? Perhaps, but only after new materials or processing makes its way through the slope of enlightenment phase and levels out on the plateau of productivity. There are many on the way, and many with a long way to go.
Beyond the Fifth Phase
Obsolescence is not a phase that is made clear in the Gartner hype cycle chart for an obvious reason. There is not much to hype about a product so old it’s being discontinued or replaced by new technology.
Since I started doing PCB design layout in the 1980s, many advanced technologies have long since slid off the plateau of productivity and are mulching in a landfill somewhere. Some of our old designs are even preserved and featured in PCB design history museums every so often.
We must always be on the watch for better solutions for the products we design. We must balance all the forces of reason in selecting technology in order to design for excellence.
If you are an informed, DFM-savvy PCB designer or engineer thinking about implementing some advanced technology, consider that our industry “right-sizes” headcount, machinery, production volumes, and even software capability all the time. Rather than quickly reaching for that sparkling, glittery piece of advanced technology to incorporate into your design, it makes sense to consider a “right-tech” approach to product design.
References
- Gartner hype cycle, Wikipedia.com.
- Engineering Together to Save Lives — The Open Source Ventilator Project, Altium, youtube.com.
This column originally appeared in the December 2024 issue of Design007 Magazine.
More Columns from Target Condition
Target Condition: My Anti-venom to PCB Cost AddersTarget Condition: Taking the Stand at Your Own Design Review
Target Condition: Designing Unconventional Geometries
Target Condition: What the Heck? A PCB Tech Spec Check
Target Condition: Keeping Your Design on the Road
Target Condition: The Tale of Five CAD Monkeys
Target Condition: Scaling PCB Design to the Power of 10
Target Condition: Practical Packaging Density in PCB Design