-
- News
- Books
Featured Books
- smt007 Magazine
Latest Issues
Current IssueSupply Chain Strategies
A successful brand is built on strong customer relationships—anchored by a well-orchestrated supply chain at its core. This month, we look at how managing your supply chain directly influences customer perception.
What's Your Sweet Spot?
Are you in a niche that’s growing or shrinking? Is it time to reassess and refocus? We spotlight companies thriving by redefining or reinforcing their niche. What are their insights?
Moving Forward With Confidence
In this issue, we focus on sales and quoting, workforce training, new IPC leadership in the U.S. and Canada, the effects of tariffs, CFX standards, and much more—all designed to provide perspective as you move through the cloud bank of today's shifting economic market.
- Articles
- Columns
- Links
- Media kit
||| MENU - smt007 Magazine
Estimated reading time: 8 minutes
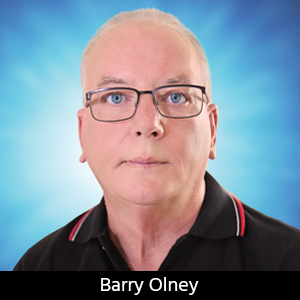
Beyond Design: Electro-optical Circuit Boards
Predicting the role of PCB designers in 10 years is a challenge. If only I had a crystal ball. However, we know that as technology progresses, the limitations of copper PCBs are increasingly apparent, particularly regarding speed, bandwidth, and signal integrity. Innovations such as optical interconnects and photonic integrated circuits are setting the stage for the next generation of PCBs, delivering higher performance and efficiency. The future of PCB design will probably incorporate these new technologies to address the challenges of traditional copper-based designs.
The prevailing trend in the PCB industry is a growing demand for smaller, lighter, flexible, and higher-performance PCBs. This trend began in the late 1980s with the mainstream adoption of surface mount technology. Shortly after, high density interconnects (HDI) became widespread, allowing denser integrated devices with closer placement. With the recent advent of artificial intelligence (AI), we face limitations in data rates, bandwidth, and power consumption. NVIDIA, the leader in AI chip development, recently released its Blackwell B200 graphics processing unit (GPU). NVIDIA says its systems can scale to tens of thousands of these Superchips running at 720 petaflops (one quadrillion or 1015 operations per second), connected via 800 Gbps networking using the new Quantum-X800 InfiniBand.
The bottleneck lies in the interconnects between these ultra-high-speed devices. Copper interconnects can only transfer information at a limited speed and bandwidth with minimal loss. Since the electromagnetic energy transporting the signals in a PCB propagates in the dielectric materials, not the copper traces, we need to improve the efficiency of the dielectric. The limitations lie in the dielectric constant and material loss. For example, FR-4 has a maximum speed of propagation of half the speed of light. Even the highest-grade materials with a very low dissipation factor (0.0002) don't significantly improve this. So, how do we overcome this limitation?
The Lord said: “Let there be light”—and there was. Multilayer electro-optical PCBs use light rather than electrical energy to transmit data. This technology offers superior signal integrity and achieves higher speeds and bandwidth at potentially greater distances than traditional copper circuits while also reducing losses and crosstalk from nearby circuits. The electronic transmission of information requires energy. The faster the interface, the more electrical power is required. At very high data transfer rates, optical interfaces can be significantly more efficient than electrical ones. Additionally, the components within these boards benefit from secure isolation between layers, ensuring uninterrupted transmission, resulting in faster transmission speeds and higher overall performance.
Electro-optical printed circuit boards (EOCBs) integrate optical and copper paths on the same board. While the copper paths distribute power and direct low-speed data, the optical paths handle high-speed signals. This segregation offers several advantages. At high frequencies, signal integrity suffers because of the skin effect, crosstalk, and skew when passing through copper systems. Optical systems do not have these issues and provide greater channel density than copper. Furthermore, optical signals do not require signal conditioning and equalization, resulting in lower power consumption compared to electrical signals. Additionally, optical systems can reduce the surface area of a PCB by 20% and the number of layers on the multilayer board by up to 50%.
Similarly, flexible-optical PCBs are becoming increasingly prevalent in modern electronics. They use specific transparent materials, such as acrylic or clear epoxy fixtures, and employ cutting-edge photolithography technology and a patented etching technique. This enables the embedding of numerous optical fibers or waveguides necessary for the modulation and transmission of light signals throughout the circuit pathways.
High-speed optical interconnects employ lasers, fiber optics, waveguide technology, and polarization components to send data directly from one interface to another without intermediate conversions or delays. This ensures high bandwidth capability and reliable, undistorted signal transmission. The essence of this concept lies in achieving three-dimensional optical routing at the board level using EOCBs combined with electro-optical transceivers.
A photonic integrated circuit (PIC) or integrated optical circuit is a microchip containing two or more photonic components forming a functioning circuit. This technology detects, generates, transports, and processes light. PICs are the driving technology behind next-generation, miniaturized, and high-performance devices. By leveraging advanced technologies such as distributed Bragg reflectors (mirrors), dielectric waveguides, vertical couplers, and electro-optic modulators, PICs enable unprecedented integration densities. This allows for a wide range of applications, from communications to sensing and packaging.
Onboard optical interconnects can manage extremely high data rates and provide a greater number of data channels compared to electrical interconnections. Moreover, as optical signal transmission is impervious to electromagnetic interference (EMI), it is ideal for mixed-signal systems, such as data acquisition and signal processing, where sensor applications need high accuracy of analog electronics.
Optical waveguides on PCBs require not only low attenuation but also a reliable manufacturing process for the optical layer. In an optical PCB, the fabrication steps and material properties of the waveguides need to be compatible with the manufacturing and assembly techniques prevalent in the PCB industry. Apart from the optical path in an optical interconnection system, there must be coupling elements that can transfer optical signals into and out of the waveguides. Additionally, common pick-and-place machines must be capable of suitably and automatically mounting these coupling elements without any active alignment between the optical waveguide and the coupling element. Using structured polymer foils helps this integration.
To construct an EOCB, laminate low-cost glass sheets with a conventional organic base material such as FR-4. You can use two structures together: Glass can be a core layer inside the conventional PCB base material and as the main carrier—a photonic interposer carrying all the PIC and electronic chip components. You can plate copper on the glass and the organic material. The processing is compatible with regular PCB processing but needs high-precision assembly.
Figure 2 illustrates the structure of a typical EOCB. The blue layer denotes a glass layer with integrated single-mode optical waveguides. The electrical processor is located on a glass interposer with a cooling surface on top. A critical point is the connection between the transceiver and the glass layer. While structuring through-glass electrical vias (TGVs) is an established process, steering the photonic signals is the challenge. Currently, there are at least two techniques under development: either a periscope placed from the top or a small mirror positioned from the bottom of the EOCB. However, industry standards or multi-source agreements for these techniques still need to be established.
There are multiple design challenges to address when developing an EOCB. These include:
- Electrical: Optimizing the path for RF and electrical signal transmission
- Optical: Ensuring signal optimization, free-space collimation, and effective optomechanical system design
- Thermal: Considering heat sources and integrating sinks as needed
An essential technology for EOCBs is the fabrication of waveguides in the glass layer (Figure 3), akin to the optical equivalent of printing circuits on a PCB. You can tailor waveguides for single-mode (SM) or multi-mode (MM) transmission. While datacom structures use multi-mode signals, silicon photonics primarily rely on single-mode signals. Lasers or other technologies can produce waveguides in glass, including by an ion exchange process that originated from semiconductor processing. The latter has the advantage of parallel processing, whereas laser processes are inherently sequential, as the laser must trace the waveguide path.
Microelectronics and printed circuit boards have developed dramatically over the 50 years I have been in the industry. In the future, EOCBs will be crucial for effective data processing. One significant requirement is the development of integrated optical connections between electrical or photonic processing and storage units at various levels, from chips and chiplets (system on chip) through interposers to full panels. Waveguides made using an ion-exchange process in inexpensive display glass laminated with conventional PCB materials can address this need. However, greater changes are on the horizon. As data usage and sharing for AI increase, optical conductors will increasingly complement electrical routing.
Key Points
- The limitations of copper PCBs have become increasingly clear.
- Optical interconnects and photonic integrated circuits are setting the stage for the next generation of PCBs.
- The bottleneck lies in the interconnects between the ultra-high-speed devices.
- Multilayer electro-optical PCBs use light rather than electrical energy to transmit data.
- At very high data transfer rates, optical interfaces can be significantly more efficient than electrical ones.
- Electro-optical printed circuit boards integrate optical and copper paths on the same board.
- At high frequencies, signal integrity suffers because of the skin effect, crosstalk, and skew when passing through copper systems. Optical systems do not have these issues and provide greater channel density than copper.
- Optical systems can reduce the surface area of a PCB by 20% and the number of layers on the multilayer board by up to 50%.
- Flexible optical PCBs use specific transparent materials, such as acrylic or clear epoxy fixtures.
- High-speed optical interconnects employ lasers, fiber optics, waveguide technology, and polarization components to send data directly from one interface to another without intermediate conversions or delays.
- A photonic integrated circuit (PIC) is a microchip containing two or more photonic components forming a functioning circuit. This technology detects, generates, transports, and processes light.
- Optical signal transmission is impervious to electromagnetic interference (EMI). It is ideal for mixed-signal systems.
- The fabrication steps in an optical PCB need to be compatible with processes in the prevalent PCB industry.
- To construct an EOCB, low-cost glass sheets can be laminated with a conventional organic base material such as FR-4.
- An essential technology for EOCB is the fabrication of waveguides in the glass, akin to the optical equivalent of printing circuits on a PCB.
Resources
- Beyond Design Columns by Barry Olney: “Next Gen PCBs—Substrate Integrated Waveguides,” “Fly-over Technology—When It All Gets Too Fast.”
- “Three trends driving the demand for EOCB,” Fraunhofer IZM.
- “Electro-optical circuit board (EOCB) enables photonic integrated circuits,” by Rajesh Uppal, International Defense, Security and Technology, June 28, 2021.
- The Glassy Future of Circuit Boards, RealIZM, March 4, 2020.
This column originally appeared in the January 2025 issue of Design007 Magazine.
More Columns from Beyond Design
Beyond Design: Effective Floor Planning StrategiesBeyond Design: Refining Design Constraints
Beyond Design: The Metamorphosis of the PCB Router
Beyond Design: Radiation and Interference Coupling
Beyond Design: Key SI Considerations for High-speed PCB Design
Beyond Design: AI-driven Inverse Stackup Optimization
Beyond Design: High-speed Rules of Thumb
Beyond Design: Integrated Circuit to PCB Integration