-
- News
- Books
Featured Books
- design007 Magazine
Latest Issues
Current IssueProper Floor Planning
Floor planning decisions can make or break performance, manufacturability, and timelines. This month’s contributors weigh in with their best practices for proper floor planning and specific strategies to get it right.
Showing Some Constraint
A strong design constraint strategy carefully balances a wide range of electrical and manufacturing trade-offs. This month, we explore the key requirements, common challenges, and best practices behind building an effective constraint strategy.
All About That Route
Most designers favor manual routing, but today's interactive autorouters may be changing designers' minds by allowing users more direct control. In this issue, our expert contributors discuss a variety of manual and autorouting strategies.
- Articles
- Columns
- Links
- Media kit
||| MENU - design007 Magazine
Estimated reading time: 3 minutes
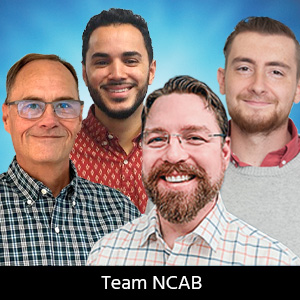
Fresh PCB Concepts: Traceability in PCB Design
Traceability has evolved from a safety-critical need in PCB production to a valuable tool across all electronic manufacturing industry sectors. The IPC-1782 standard addresses automated data collection, reduces ownership costs, and ensures accurate, timely information. It provides a flexible data architecture for different levels of traceability, from highly detailed systems (e.g., critical safety systems) to basic traceability needs (e.g., consumer products). The structure avoids data duplication and allows crucial information to be added post-production.
This standard also emphasizes the benefits of best-practice data collection, highlighting its role in raising quality and performance expectations while offering protection against market cost product issues. In short, IPC-1782 modernizes PCB traceability practices, integrating it into quality operations and enhancing manufacturing efficiency across industries.
The standard addresses the historical challenges caused by the lack of uniform traceability, which led to inefficiencies in tracking parts and resolving quality or reliability issues. It aims to improve operational efficiency, productivity, and product quality while enabling predictive manufacturing maintenance. It also helps organizations ensure products meet or exceed customer expectations and reduce counterfeit components in the supply chain.
Key Aspects
PCB/component traceability provides a structured approach to tracking bare PCBs and components in electronic assemblies, ensuring accurate identification, cataloging, and monitoring of all components throughout their lifecycle.
Supply chain transparency methods enable manufacturers and designers to trace components back to their source, thus ensuring quality control, compliance, and risk management.
By supporting detailed component tracking, robust traceability helps companies meet environmental regulations, such as Restriction of Hazardous Substances (RoHS) and Waste Electrical and Electronic Equipment (WEEE), together with internal benchmarks, and ensures compliance with industry standards.
Lifecycle management covers the entire lifecycle of a component, ensuring that manufacturers can verify the authenticity and quality of components and manage them through design, procurement, manufacturing, and service.
Benefits
Reduced risk of counterfeit parts: Traceability minimizes the risk of using substandard or counterfeit parts.
Improved quality control: By tracking components, manufacturers can address issues promptly and accurately.
Regulatory compliance: Traceability assists in maintaining compliance with global standards and regulations.
Supply chain visibility: Enhances the overall visibility of the supply chain, improving efficiency and accountability.
Tackling Traceability Solutions: Develop Serialization to Meet the Need
We start by opening a dialogue and determining specific requirements. The serialization details shall be As Agreed Upon Between User and Supplier (AABUS).
What are your project’s serialization needs?
- Methods of serialization
- Data to include
- Manufacturing details, component information, placement, etc.
- Compliance level
- Technology integration, software systems, and automated reader systems
By addressing these considerations, you can effectively implement serialization for PCBs and enhance traceability, quality control, and overall manufacturing optimization.
Implementing 2D Codes in PCB Manufacturing
Data matrix vs. QR format: These two codes appear similar (square or rectangular), but they serve different purposes. The easiest way to identify them is to look for the larger squares at the corners. If there are squares in the code, it’s a QR code, whereas a 2D code appears more uniform.
Technically, both QR and Data matrix codes are 2D barcodes (2D codes), and both are being used more in manufacturing. Data matrix codes are physically smaller than QR codes, offering high data density. These codes provide an ideal solution for marking PCBs where space is limited.
The U.S. Electronic Industries Alliance (EIA) recommends using a Data matrix for labeling small electronic components. Data matrix codes are also the only 2D codes approved by the Global Language of Business (GS1) for regulated healthcare items. They are also the default code for automotive and aerospace applications.[KH1]
QR and Data matrix codes are in the public domain and are royalty free. Published specifications and print requirements for each code are available from the International Organization for Standardization[KH2] (ISO).
Which 2D Code Is Right for You?
NCAB Group provides QR and Data matrix coding to encode more data than a traditional 1D barcode and provides additional information for internal traceability. Companies mostly use Data matrix codes for internal product identification and anti-counterfeit applications, while QR codes have become the standard for most consumer-facing applications.
This table outlines some common applications of both codes.
PCB traceability may seem like a minor factor when considering the entire design, assembly, and end product. However, I have found the IPC-1782 standard not only modernizes traceability but also drives operational excellence and enhances quality and reliability, ultimately building greater trust throughout the supply chain.
When considering traceability, consider your specific needs. Traceability can be as simple as an alpha/numeric configuration to the higher end by incorporating 2D coding techniques.
Mike Marshall is a field application engineer at NCAB Group.
More Columns from Fresh PCB Concepts
Fresh PCB Concepts: Designing for Success at the Rigid-flex Transition AreaFresh PCB Concepts: More Than Compliance—A Human-centered Sustainability Approach
Fresh PCB Concepts: Assembly Challenges with Micro Components and Standard Solder Mask Practices
Fresh PCB Concepts: The Power of a Lunch & Learn for PCB Professionals
Fresh PCB Concepts: Key Considerations for Reliability, Performance, and Compliance in PCBs
Fresh PCB Concepts: Tariffs and the Importance of a Diverse Supply Chain
Fresh PCB Concepts: PCB Stackup Strategies—Minimizing Crosstalk and EMI for Signal Integrity
Fresh PCB Concepts: PCB Plating Process Overview