-
- News
- Books
Featured Books
- design007 Magazine
Latest Issues
Current IssueShowing Some Constraint
A strong design constraint strategy carefully balances a wide range of electrical and manufacturing trade-offs. This month, we explore the key requirements, common challenges, and best practices behind building an effective constraint strategy.
All About That Route
Most designers favor manual routing, but today's interactive autorouters may be changing designers' minds by allowing users more direct control. In this issue, our expert contributors discuss a variety of manual and autorouting strategies.
Creating the Ideal Data Package
Why is it so difficult to create the ideal data package? Many of these simple errors can be alleviated by paying attention to detail—and knowing what issues to look out for. So, this month, our experts weigh in on the best practices for creating the ideal design data package for your design.
- Articles
- Columns
- Links
- Media kit
||| MENU - design007 Magazine
Estimated reading time: 6 minutes
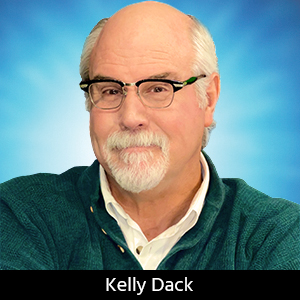
Contact Columnist Form
Target Condition: Designing vs. Inventing
After hearing me rave about IPC APEX EXPO for years, my boss, Chad Orebaugh, joined me at the show for the first time last year. We met at the registration counter, got our badges, and he said, “Okay, Kelly, impress me.”
For two days, we walked the show floor, attended committee meetings, professional development courses, and the EMS Leadership Summit (Chad is the executive VP of engineering for an EMS supplier). I was anxious to know his thoughts, but when I asked, his reply surprised me. He thought there was something missing. I was puzzled. What exactly was missing? “This is where design begins,” I told him. “This show provides a fantastic opportunity for PCB design engineers to get in touch with the capability of the machinery, materials, and processes.”
In a moment, I’ll circle back to his response.
The Show Floor
On our first day at IPC APEX EXPO, we walked the aisles, surveying the capabilities of the new PCB manufacturing machinery. Experienced PCB designers form solid contact with the companies that turn their CAD data and documentation into printed boards. Understanding manufacturing capability is key to never laying down a track that cannot be printed, plated, and etched. Supplier capability must be understood to effectively design a PCB stackup for impedance control or to select the proper hole size for a filled via. Machine process options and accuracy must be comprehended to define tolerance zones of a routed, punched or V-scored board edge.
These are all top examples of still-common design for manufacturing (DFM) failures that stop hundreds of production orders every day until a concession or design change is made to match supplier capability. At IPC APEX EXPO, PCB designers get the opportunity to keep up with improvements in machine and process capability. If you’re lucky, you may even see one of your suppliers inking a purchase order for new machines to update their own capability.
Standards Meetings, Sessions, and Discussions
I suggested to Chad that we attend several technical conference sessions, standards development committee meetings, and since we specialize in assembly, to attend the IPC EMS Leadership Summit. We spent a considerable amount of time in each, and I was glad we could do that together. This show brings together industry stakeholders to develop and establish our electronics industry standards—our rules of engagement—for design, process, and manufacturing expectations with the goal of achieving mutual quality success for all. Each session focused on challenges to updating older specifications and regulating which new committees must be formed to keep up with new technologies. It is at these meetings that our industry’s PCB design and manufacturing standards are crafted and revised. We were impressed to hear so many industry leaders address their challenges by stepping up plans to improve standards and guidelines. When followed, these standards streamline the many PCB project workflows for quoting, materials, manufacturing process and quality.
Design and manufacturing specification committees are widely represented, and their content is reviewed throughout the year to present best value standards for quality. The committees have cross-functional representation. No single stakeholder speaks for the others’ areas of expertise or defines a process that benefits their responsibility alone.
PCB designers should take note of this collaborative process of review and concurrence. Excellent design specifications are not created autonomously and neither are excellent PCB layouts. The designs that include the highest manufacturability and best performance are reviewed concurrently by multiple stakeholders—fabricators, assemblers, electrical, mechanical, and test engineers—they are not created alone in a vacuum.
Professional Development Courses
We were also introduced to a divergence of PCB creative thought through some of the advanced PCB design concept courses, including one on flex circuit design and another on dense packaging design strategies, including design for harsh environments. The message we heard consistently was to adhere to existing design and manufacturing standards. Manufacturers, especially EMS providers, love that because when designs match our PCB supplier’s capability standards and our assembly line standards, we all make money by saving money. However, due to the advanced design constraints, references were occasionally made to the importance of checking supplier capability.
There are sectors of product development in our industry where our specifications have not caught up to what PCB design engineers are being asked to achieve. The concept of “working with a supplier” to develop custom requirements needed to solve advanced packaging design—design for nanoscale or harsh environments—was explained by emphasizing that going outside of IPC Class 3 scope of design and manufacturing standards is extremely costly but often required for our aerospace and other new or emerging industries.
Designing vs. Inventing
Now, back to my boss’s comments about what was missing at the show. Chad said, “PCB designers need to know the difference between designing and inventing.”
From his perspective as an entrepreneur and inventor, the show floor was filled with machinery and services, available to anyone who wants to use them to design things. They offer a current snapshot of standardized capabilities. However, Chad believes that the show could be better served by providing a forum for the inventor—someone who must beat their competition, often through disruptive engineering—to reach the machine and process stakeholders to scream for what they need.
IPC APEX EXPO should be a place where we further expand electronics service, equipment, and material suppliers (who are already there to sell current capability) and hear from inventors and entrepreneurs regarding their perspectives on what is missing in materials and manufacturing so their current ideas and inventions can be realized.
My boss described two types of customers:
- The first brings us very manufacturable data and documentation that can be interpreted by our process stakeholders and can be easily quoted, procured, assembled, tested, and shipped without issues. These customers employ PCB designers who collaborate with all stakeholders.
- Another type brings us data and documentation that has been awkwardly used to prototype some very brilliant product ideas but, like the advanced technology examples brought up in the Professional Development classes, are full of capability mismatches for our standard, low-cost, high-volume suppliers.
He then offered a final, convincing point that truly expanded my previously dogmatic take on standards-based PCB product development. “We didn’t get to the moon, nor will we get to Mars, by designing and manufacturing to present standards,” he said. And with that, he gave me a fist-bump and headed to the airport.
IPC APEX EXPO is indeed a great place for designers to get in touch with present manufacturing capability, for machine manufacturers to show their present capability, and to learn to design with standards so that PCBs can be easily manufactured in volume.
I understand Chad’s point; he is an inventor and an entrepreneur. But if PCB designers are not designing with standards, they are either inventing a brilliant product that will require millions of dollars of investment, or inventing a supplier headache that could have been easily remedied with standard DFM principles.
Kelly Dack, CIT, CID+, provides DFx centered PCB design and manufacturing liaison expertise for a dynamic EMS provider in the Pacific Northwest while also serving as an IPC design certification instructor (CID) for EPTAC. To read past columns, click here.
References
Read more about my time with Chad Orebaugh here.
This column originally appeared in the March 2025 issue of Design007 Magazine.
More Columns from Target Condition
Target Condition: Are Autorouters Friend or Foe?Target Condition: From Dream House to Drill Files
Target Condition: ‘Boomer to Zoomer: Do You Copy?’
Target Condition: Advanced Packaging Technologies—Look Before You Leap
Target Condition: My Anti-venom to PCB Cost Adders
Target Condition: Taking the Stand at Your Own Design Review
Target Condition: Designing Unconventional Geometries
Target Condition: What the Heck? A PCB Tech Spec Check