Estimated reading time: 5 minutes
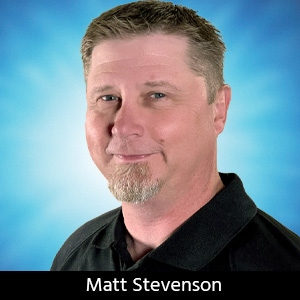
Connect the Dots: Stop Killing Your Yield—The Hidden Cost of Design Oversights
I’ve been in this industry long enough to recognize red flags in PCB designs. When designers send over PCBs that look great on the computer screen but have hidden flaws, it can lead to manufacturing problems. I have seen this happen too often: manufacturing delays, yield losses, and designers asking, “Why didn’t anyone tell me sooner?” Here’s the thing: Minor design improvements can greatly impact manufacturing yield, and design oversights can lead to expensive bottlenecks. Here’s how to find the hidden flaws in a design and avoid disaster.
Small Adjustments, Big Impact
Let’s start with the basics: Designing for yield. Small details in the layout matter, like via sizes, copper distribution, or tolerances. Designers often underestimate the impact a small design flaw can have on the PCB manufacturing processes, the reliability of the project, or the cost of manufacturing. A decision that does not line up with your manufacturer’s core competency can lead to project delays, reworking to rectify the error, electrical opens from voided plating, electrical shorts, and scrap boards. You can avoid these problems by understanding the manufacturer’s sweet spots.
Via aspect ratios (the ratio of the board thickness to the smallest hole diameter) matter. Disappointment will probably result if you use a small-diameter drill for via holes in a thicker-than-average board and expect perfect hole plating. As the aspect ratio increases, the ability to plate copper in these smallest holes becomes more difficult. The cost usually increases, as does the chance of yield loss and reliability. An aspect ratio of less than 10:1 is generally a rule of thumb for most fabricators. Above that threshold, fabricators must take special care to produce quality products.
Another error is improper copper balancing. Make sure the layer stackup is symmetrical about the center, and consider dielectric thicknesses, copper weights, and the distribution of plane versus signal layers. The more balanced and symmetrical the design is along the Z-axis, the better. Uneven copper distribution (in the X or Y axis) across the individual layers can also create issues and lead to board warpage, which often makes it difficult to assemble surface mount components accurately and reliably.
Unnecessarily tight tolerances can drive up costs and increase yield loss. Designers love pushing the limits, specifying tolerances that are not required or that fabricators can’t produce reliably. I once saw a design with zero deviation from nominal called out as the tolerance. When we asked the designer about deviating to a reasonable tolerance, he said, “It is not critical to have it so tight, but I thought. “What the heck? It takes out some of the variation in my design.” Specifying ultra-tight tolerances when you don’t need them is like driving a Ferrari at top speed to the grocery store: unnecessary and risky.
Please refer to our book, DFM Essentials, for an in-depth look at potential cost drivers and common design-related errors.
How Oversights Cause Bottlenecks
When small design issues pile up, the risk to the yield, board reliability, and your project’s delivery timeline increases. Layer misalignment is one of the most common causes of non-conformance on high-density projects. Materials shrink and expand during lamination. Sometimes, it is routine and predictable, but at other times, it can be design-specific. Working up front with your manufacturer when creating the layer stackup can help the first build be more successful. Using known material sets in known configurations can take some of the guesswork out of the build.
Another potential design issue is missing thermal relief on pads. Designers want to minimize resistance and maximize current flow, but connecting pads directly to large copper planes without thermal relief creates issues at assembly. Uneven heat distribution prevents proper solder wetting, resulting in weak or cold solder joints. These will fail inspection and require rework, or worse, fail in the field. A simple controlled heat path provided with the thermal relief pattern could have saved the batch.
Unclear or missing documentation can bottleneck an entire project. If you send incomplete design files or forget critical details, like drill files or stackup diagrams, your manufacturer must reach out to the designer for the pertinent information. I recall a project where the documentation was so vague we had to call the designer three times to confirm basic details. By the time we had what we needed, we’d missed deadlines.
The Cost of Getting It Wrong
When you don’t fix problems early, you pay for them—literally. Every defective board adds to your costs, be it scrapped material, rework time, or delayed shipments. Hidden costs can also damage relationships with your manufacturers or end customers. They are more likely to miss deadlines if they are constantly working to resolve design issues. I’ve seen companies lose valuable production partners because others deemed them difficult to work with. One designer told me they didn’t think a 5% defect rate was a big deal until they realized they were manufacturing 10,000 boards per run. That’s 500 boards that needed rework or scrapping. It doesn’t take a genius to see how quickly that eats into your bottom line.
Fixing the Problem
The good news is these problems are preventable. Involve your manufacturer early. Don’t wait until you’ve finalized the design to ask if it’s manufacturable. Manufacturers know their limits and can help you adjust your design before it’s too late.
Make sure your design rules match the manufacturer’s capabilities. If they say their minimum trace width is 4 mils, don’t design with 3-mil traces and hope for the best. Use automated DFM tools to catch issues like spacing errors or copper imbalances before you submit your design.
Finally, communicate. Clear documentation, detailed stackup diagrams, and frequent check-ins with your manufacturer can prevent most bottlenecks. You’d be surprised how many problems disappear when everyone is on the same page.
Final Thoughts: Stop Making Your Manufacturer Sweat
Designing for yield isn’t just about getting boards out the door; it’s about getting them out efficiently. Small design tweaks, like properly sized vias and balanced copper layers, can make the difference between smooth production and endless headaches. By taking the time to avoid common bottlenecks like potential layer misalignment or unclear documentation, you don’t just help yourself; you help your manufacturer, your deadlines, and your budget.
The next time you’re about to hit “send” on that design package, pause. Double-check the details. Call your manufacturer if you’re unsure about something. Your production line, boss, and future self will thank you.
Read Matt’s book, The Printed Circuit Designer’s Guide to… Designing for Reality, or listen to his podcast here.
This column originally appeared in the March 2025 issue of Design007 Magazine.
More Columns from Connect the Dots
Connect the Dots: How to Avoid Five Common Causes of Board FailureConnect the Dots: Sequential Lamination in HDI PCB Manufacturing
Connect the Dots: The Future of PCB Design and Manufacturing
Connect the Dots: Proactive Controlled Impedance
Connect the Dots: Involving Manufacturers Earlier Prevents Downstream Issues
Connect the Dots: Designing for Reality—Routing, Final Fab, and QC
Connect the Dots: Designing for Reality—Surface Finish
Connect the Dots: Designing for Reality—Solder Mask and Legend