-
- News
- Books
Featured Books
- pcb007 Magazine
Latest Issues
Current IssueIn Pursuit of Perfection: Defect Reduction
For bare PCB board fabrication, defect reduction is a critical aspect of a company's bottom line profitability. In this issue, we examine how imaging, etching, and plating processes can provide information and insight into reducing defects and increasing yields.
Voices of the Industry
We take the pulse of the PCB industry by sharing insights from leading fabricators and suppliers in this month's issue. We've gathered their thoughts on the new U.S. administration, spending, the war in Ukraine, and their most pressing needs. It’s an eye-opening and enlightening look behind the curtain.
The Essential Guide to Surface Finishes
We go back to basics this month with a recount of a little history, and look forward to addressing the many challenges that high density, high frequency, adhesion, SI, and corrosion concerns for harsh environments bring to the fore. We compare and contrast surface finishes by type and application, take a hard look at the many iterations of gold plating, and address palladium as a surface finish.
- Articles
- Columns
Search Console
- Links
- Media kit
||| MENU - pcb007 Magazine
Nick Koop Launches IPC Flex Design Class
May 6, 2025 | Andy Shaughnessy, Design007 MagazineEstimated reading time: 7 minutes
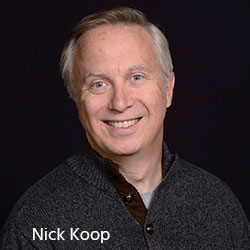
Nick Koop is director of flex technology for TTM Technologies, and he’s been a staple of IPC’s flex committees for decades. He’s also a longtime flex design instructor, and he’s about to debut a new IPC class, Flex and Rigid-Flex Design for Manufacturability, which will run May 12–21. I asked Nick to tell us about this new class and what attendees can expect to learn.
Andy Shaughnessy: Why don't you give us a quick background about yourself?
Nick Koop: I've been in flex for more years than I want to count. I was a college intern when I first started in the flex world. I didn't know what flex was when I first started, and I’ve only been with two companies over that timeframe. I started as an intern at Minco, moved into engineering, managed engineering, ran the operation, and then moved to another company, which is TTM. I’ve been involved with flex my entire career across these companies and helped them grow.
Shaughnessy: How did you get involved with IPC flex committees?
Koop: I got started with IPC in the ‘80s. It was almost like a reverse coup. I remember being in a meeting and Clark Webster said, “Hey, we need a new vice chair. What do you think, Nick?” Somehow, I became vice chair. From there, I just kept going. It's been great from both the industry and the business side. It’s been really rewarding over the years to be part of some of the cool stuff we get to see.
Shaughnessy: You’ve also been a flex instructor at IPC APEX EXPO for years. Tell us about this flex class that you will teach for IPC.
Koop: This class will be a spinoff from the IPC APEX EXPO classes. We will try to get a little bit more in-depth on certain topics, for people who maybe can't get to APEX EXPO. That's the idea here—to go into greater depth. With a class like this, attendees might be a little more open to asking questions and learning a bit more than they are in one class at a trade show. Once it’s done, then you’ve got information that can be referred to over and over, and because each session is recorded, students have access to the content for an additional year.
Shaughnessy: This class focuses on DFM for flex. What are some of the biggest DFM and reliability challenges you see in flex and rigid-flex?
Koop: Whether it's flex or rigid boards, everyone is pushing the envelope, saying, “Can we do this?” “You can, but…” Our customers will put something on the drawing and say, “Hey, so and so said they can do it.” But I’ll say, “Yeah, so can I. I can do a lot of things once. But if you want to build volume, you don't want to be relying on inspection to inspect all the bad stuff."
Inspection might only be 80% effective. But we want to design it in, not inspect it in. I'm in an aerospace defense world, where things are mission-critical. I know most kids would say their cell phone is mission-critical, but some of us survived several decades without a phone,
What I've seen over the years is the military or medical folks saying, “We need the best reliability ever.” Now you see the automotive groups pushing hard on everything for reliability because they don't want a warranty issue. I see the same thing in the computer segment. Every industry says, “I need highest reliability.” Nobody wants low reliability. So I’ll be helping them out and showing them where your gotchas are.
On the flex side the biggest areas where we see challenges are almost always mechanical. The rigid board just sits there all day long. It doesn't move. But flex has to be bent into place or in some cases needs to bend on a regular basis. So, when you’re working through those ideas, you see that the mechanical part is equally as important as making sure you have your signal integrity figured out.
Shaughnessy: Speaking of reliability, I talked to a Bose engineer a couple of years ago, and he said they switched to flex for some products for reliability reasons. Flex was just more reliable than a rigid board.
Koop: Exactly. In many cases, it’s more reliable than a bundle of wires and a connector. There's an opportunity to be more reliable. For years, that was the military’s technical solve. Now, a lot of companies say, “Flex is actually my go-to solution for these kinds of things.”
If you tear apart a hearing aid, there's a flex of some sort inside and the origami is brilliant inside those, because an ear canal is not a normal shape. It’s just a strange shape, and that's where flex starts to shine.
Shaughnessy: What are some takeaways that you hope the attendees get out of your class?
Koop: We’ll talk a bit about things like how to construct the flex, where the flex layers stack up, and whether you should do flex or rigid-flex. We'll talk about some of the mechanical stress risers and how to avoid those. We'll talk about via structures. Rigid designers might ask, “I'm used to all these different via structures in my rigid boards. Can I use them all in flex?” And the answer is yes, but with a few caveats. We’ll talk about that, and we’ll talk about impedance. We do impedance and rigid-flex all the time, and we high-frequency stuff. It can be done, but you need to pick the right materials and understand what works best. Those are some of the big ones we'll hit.
Shaughnessy: Do attendees need to have flex background coming into this class?
Koop: No. If they're coming in with just a rigid board background, they can learn quite a lot about flex and build on that rigid board foundation. This class will fall somewhere between Flex 101 and a Ph.D.-level class (laughs). We’ll start with introductory content, and later we’ll cover more advanced items. Every class will be different, and attendees will ask questions that will take us down different tangents. Questions are great, because if one person asks that question, there are probably five other people thinking about asking that question. Someone in the class might say, “Hey, I’ve done that.” Then they'll know someone else who can ask if they have a flex question.
Shaughnessy: Are you going to walk them through the flex standards?
Koop: Yes, but I won’t read 150 pages of standards. Basically, these are the five standards (IPC-2223, 4202, 4203, 4204, 6013) that students are given access to as a part of the class, you need to know when it's time, so get familiar with them. Know where to look.
Shaughnessy: Is there anything else you’d like to add?
Koop: We're happy to see so many people are interested in this class. People will learn a lot and get a fairly strong basis that they can work from even if they've never done any flex before. They’ll be a little more confident and see that flex can be an advantage. I'm trying to take it from “I have to do it” to “How can I turn flex into an advantage for myself and leverage flex technology?”
Shaughnessy: How long is the class?
Koop: It’s a two-week class, two sessions a week, about two hours each. It’s roughly eight hours of instruction over a two-week timeframe. No tests. Your test will be when you design a part for yourself and how well it goes.
Shaughnessy: A real-world test. Very good. Let us know how it goes, Nick. Thanks for speaking with me.
Koop: Thank you, Andy.
Registration is open for Nick’s upcoming online Flex and Rigid-Flex Design for Manufacturability course, which starts May 12. To enroll today, click here.
Suggested Items
Amphenol Printed Circuits Brings Its Boards to the 2025 IMSI
05/29/2025 | Amphenol Printed CircuitsAmphenol Printed Circuits will be offering a small but impressive sample of its vast design, manufacturing, and test capabilities in Radio Frequency (RF) printed circuit boards (PCBs) Rigid-Flex/Flex and backplanes at the 2025 IEEE MTT-S International Microwave Symposium exhibition.
Global PCB Connections: Rigid-flex and Flexible PCBs—The Backbone of Modern Electronics
05/20/2025 | Jerome Larez -- Column: Global PCB ConnectionsIn the past decade, flex and rigid-flex PCB technology has become the fastest-growing market segment. As an increasing number of PCB companies develop the capabilities to fabricate this technology, PCB designers are becoming comfortable incorporating these designs into their products.
Flexible PCB Market to Reach $61.75B by 2032, Driven by the Demand for Compact Electronics, Automotive and Medical Applications
05/16/2025 | Globe NewswireAccording to the SNS Insider, “The Flexible PCB Market was valued at USD 21.42 billion in 2023 and is expected to reach $61.75 billion by 2032, growing at a CAGR of 12.52% over the forecast period 2024-2032.”
CEE PCB to Exhibit at The Battery Show Europe 2025
05/14/2025 | CEE PCBTom Yang, CEO of CEE PCB, has announced that the company will exhibit at The Battery Show 2025, held from June 3-5 at the Messe Stuttgart in Stuttgart, Germany, in Booth F69 in Hall 7.
American Standard Circuits to Exhibit and Speak at SMTA Oregon Expo
05/14/2025 | American Standard CircuitsAnaya Vardya, President, and CEO of American Standard Sunstone Circuits has announced that his company will be exhibiting SMTA Oregon Expo & Tech Forum to be held on May 20 at the Wingspan Events and Conference Center in Hillsboro, Oregon.