-
- News
- Books
Featured Books
- pcb007 Magazine
Latest Issues
Current IssueInventing the Future with SEL
Two years after launching its state-of-the-art PCB facility, SEL shares lessons in vision, execution, and innovation, plus insights from industry icons and technology leaders shaping the future of PCB fabrication.
Sales: From Pitch to PO
From the first cold call to finally receiving that first purchase order, the July PCB007 Magazine breaks down some critical parts of the sales stack. To up your sales game, read on!
The Hole Truth: Via Integrity in an HDI World
From the drilled hole to registration across multiple sequential lamination cycles, to the quality of your copper plating, via reliability in an HDI world is becoming an ever-greater challenge. This month we look at “The Hole Truth,” from creating the “perfect” via to how you can assure via quality and reliability, the first time, every time.
- Articles
- Columns
- Links
- Media kit
||| MENU - pcb007 Magazine
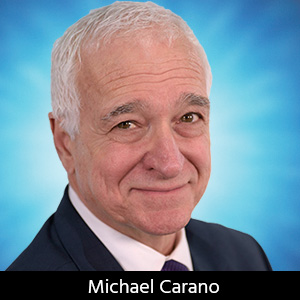
Trouble in Your Tank
Column from: Michael Carano
Mike brings over 40 years of electronics industry experience with special expertise in manufacturing, performance chemicals, metals, semiconductors, medical devices, and advanced packaging.
A recognized thought leader, subject matter expert (SME), and author, Mike holds 7 US and 20 foreign patents. He has published over 190 articles and presented peered reviewed technical papers all over the world.
Mike is currently a Technical and Market Intelligence consultant to the Global Electronics Association and a project facilitator for HDP User Group international.
Mike has served on more than 20 IPC Standards committees, and has served 14 years as a member of the Global Electronics Association Board of Directors. Mike has developed multiple professional development courses for the Global Electronics Association including the Advanced Trouble Shooting and Defect Analysis for Printed Circuit Boards.
In 2014 Mike was elected to the Global Electronics Association (IPC) Raymond E. Pritchard Hall of Fame, and later recognized for his standards work with Mike’s awarding of the Dieter Bergman Fellowship award and most recently the ANSI Finegan Medal. Previously Mike was the VP of Technology Business Development at RBP Chemical Technology, and the Global Director of R&D and Applications Engineering for the OM Group. He holds a B.A. in Chemistry and an M.B.A.