-
- News
- Books
Featured Books
- pcb007 Magazine
Latest Issues
Current IssueInventing the Future with SEL
Two years after launching its state-of-the-art PCB facility, SEL shares lessons in vision, execution, and innovation, plus insights from industry icons and technology leaders shaping the future of PCB fabrication.
Sales: From Pitch to PO
From the first cold call to finally receiving that first purchase order, the July PCB007 Magazine breaks down some critical parts of the sales stack. To up your sales game, read on!
The Hole Truth: Via Integrity in an HDI World
From the drilled hole to registration across multiple sequential lamination cycles, to the quality of your copper plating, via reliability in an HDI world is becoming an ever-greater challenge. This month we look at “The Hole Truth,” from creating the “perfect” via to how you can assure via quality and reliability, the first time, every time.
- Articles
- Columns
- Links
- Media kit
||| MENU - pcb007 Magazine
Estimated reading time: 1 minute
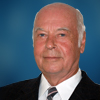
Contact Columnist Form
Supporting Thin Structures
In the world of PCB fabrication, there are few examples of special support features for thin substrates. But they do exist in the form of assist features in conveyorized spray modules designed to prevent mishaps during the transfer of very thin innerlayers, or in the transport of flex circuit boards, employing the use of leaders or frames. On the other hand, tape supports have been used in wafer-level processing for quite some time, such as dicing tapes to support and hold in place the wafer and the diced chips during singulation, and more recently, support systems that enable backgrinding of wafers, and post-backgrinding processing steps such as sputtering and plating. This application presents challenging material and process control requirements that are worth becoming familiar with.
Background Information
Wafer backgrinding is the process of grinding the backside of the wafer to the correct wafer thickness prior to assembly. It is also referred to as “wafer thinning.” Wafers are ground back from about 300 micron thickness down to 50 micron, for example. Wafer backgrinding has not always been necessary, but the drive to make packages thinner has made it indispensable. Most package types in the semiconductor industry today would require a wafer thickness ranging from 8 to 20 mils.
Wafers normally undergo a cleaning and surface lamination process prior to the actual backgrinding process. Surface lamination involves the application of a protective tape over the surface of the wafer to protect it from mechanical damage and contamination during backgrinding.
The surface-laminated wafers are then loaded into cassettes that will go into the cassette holder of the backgrinding machine. The machine picks up the wafer from its backside (untaped side) with a robotic arm, which positions the wafer for backgrinding. The process is automatically accomplished by a grinding wheel, following a precise set of parameters to ensure proper backgrinding.
To remove debris from the wafer, it is usually washed continuously with D/I water while undergoing backgrinding. Once the wafer has been background, the wafer is returned to the cassette, and the cycle is repeated for the next wafer.
Read the full column here.
Editor's Note: This column originally appeared in the June 2014 issue of The PCB Magazine.
More Columns from Karl's Tech Talk
Karl's Tech Talk: Digital Imaging UpdateKarl’s Tech Talk: Electronic Packaging Levels
Green Legislation and the Impact on Electronic Materials and Processes
Digital Imaging Revisited
Dry Film Photoresist Thickness Selection Criteria
Quick-Turn Circuit Board Shops
Optical Interconnects
Signal Loss