-
- News
- Books
Featured Books
- pcb007 Magazine
Latest Issues
Current IssueInventing the Future with SEL
Two years after launching its state-of-the-art PCB facility, SEL shares lessons in vision, execution, and innovation, plus insights from industry icons and technology leaders shaping the future of PCB fabrication.
Sales: From Pitch to PO
From the first cold call to finally receiving that first purchase order, the July PCB007 Magazine breaks down some critical parts of the sales stack. To up your sales game, read on!
The Hole Truth: Via Integrity in an HDI World
From the drilled hole to registration across multiple sequential lamination cycles, to the quality of your copper plating, via reliability in an HDI world is becoming an ever-greater challenge. This month we look at “The Hole Truth,” from creating the “perfect” via to how you can assure via quality and reliability, the first time, every time.
- Articles
- Columns
- Links
- Media kit
||| MENU - pcb007 Magazine
Estimated reading time: 1 minute
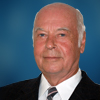
Contact Columnist Form
Green Technologies in PCB Fabrication
“Green” and “environmentally friendly” are ill-defined terms. In general, these terms refer to manufacturing that involves the replacement of toxic substances with less toxic materials, the elimination of materials or processing steps, and less consumption of chemicals (i.e., more efficient or higher yield processing, reduction of water use, reduction of energy use, less space requirement, smaller equipment foot print, and recycling and on-site recovery of materials).
Direct Metallization
This family of processes eliminates the electroless copper process. These processes typically have fewer process steps, use less rinse water, have less floor space requirement, and use less toxic chemicals. Direct metallization processes include:
Palladium-based
These processes pretty much follow the classic electroless copper processing step sequence, except the sequence ends with the application of the palladium catalyst, followed by the activation, then skips the electroless bath and proceeds to copper electro-plating.
Carbon or Graphite-based
Using small carbon or graphite particles to render the dielectric hole-wall electro-platable, this process involves very few steps.
Conductive Polymer-based
The process of using a non-conductive monomer to coat the board surface follows an oxidation step that forms a conductive polymer from the non-conductive monomer. The polymer then facilitates copper electro-plating on the non-conductive dielectric hole wall. An example of such a conductive polymer formation is the oxidation of pyrrole to poly-pyrrole, using permanganate as the oxidation agent. The permanganate is reduced to manganese dioxide, which is insoluble and needs to be further reduced to the soluble manganese Mn2+ ion. Another example is the polymerization of “EDOT” (3,4-ethylenedioxy-thiophene) to poly-EDOT.
Read the full column here.
Editor's Note: This column originally appeared in the April 2014 issue of The PCB Magazine.
More Columns from Karl's Tech Talk
Karl's Tech Talk: Digital Imaging UpdateKarl’s Tech Talk: Electronic Packaging Levels
Green Legislation and the Impact on Electronic Materials and Processes
Digital Imaging Revisited
Dry Film Photoresist Thickness Selection Criteria
Quick-Turn Circuit Board Shops
Optical Interconnects
Signal Loss