-
- News
- Books
Featured Books
- design007 Magazine
Latest Issues
Current IssueProper Floor Planning
Floor planning decisions can make or break performance, manufacturability, and timelines. This month’s contributors weigh in with their best practices for proper floor planning and specific strategies to get it right.
Showing Some Constraint
A strong design constraint strategy carefully balances a wide range of electrical and manufacturing trade-offs. This month, we explore the key requirements, common challenges, and best practices behind building an effective constraint strategy.
All About That Route
Most designers favor manual routing, but today's interactive autorouters may be changing designers' minds by allowing users more direct control. In this issue, our expert contributors discuss a variety of manual and autorouting strategies.
- Articles
- Columns
- Links
- Media kit
||| MENU - design007 Magazine
Estimated reading time: 1 minute
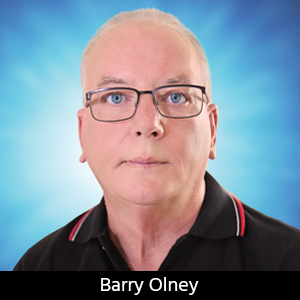
Mythbusting: There are No One-way Trips!
One of the greatest myths in PCB design is that we only have to route signal traces from pin-to-pin to make a complete connection. And, that ensuring these traces have matched delay is the only timing issue we need to consider. However, current is not a one way trip--it must complete the circuit back to the source to provide the round-trip current loop. This misconception comes from the fact that we only draw the pin-to-pin connections on the schematic and ground the chips at one point.
Current always flows in a loop. However, it does not go down to the end of the trace, to the load, and then begin to make its way back to the source. But rather, the outbound pulse charges the local parasitic capacitance as it propagates down the transmission line and returns to the driver. As the pulse progresses down the line, current returns to the source as the wave front moves until it finally reaches the load. If the return path is disrupted and does not flow directly beneath the trace, the loop area and hence delay are extended. This generally results in increased emissions of radiation.
In a previous column, The Dumping Ground, I discussed why the ground plane is not a dumping ground for unwanted signals. Most PCB designers think that the ground only serves to make the routing easier, allowing the designer to ground anything, anywhere without having to run multiple tracks. Generally, a component requiring a ground connect is just grounded at any point on the board creating the connection. But this does not consider the return current path which is just as important as the actual trace routing for high-speed design.
In a DC circuit, the return current takes the path of least resistance. But at high speeds, the return current takes the path of least inductance which just happens to be the reference plane (either ground or power) directly above or below the trace.
Read the full column here.
Editor's Note: This column originally appeared in the April 2014 issue of The PCB Design Magazine.
More Columns from Beyond Design
Beyond Design: Effective Floor Planning StrategiesBeyond Design: Refining Design Constraints
Beyond Design: The Metamorphosis of the PCB Router
Beyond Design: Radiation and Interference Coupling
Beyond Design: Key SI Considerations for High-speed PCB Design
Beyond Design: Electro-optical Circuit Boards
Beyond Design: AI-driven Inverse Stackup Optimization
Beyond Design: High-speed Rules of Thumb