-
- News
- Books
Featured Books
- pcb007 Magazine
Latest Issues
Current IssueInventing the Future with SEL
Two years after launching its state-of-the-art PCB facility, SEL shares lessons in vision, execution, and innovation, plus insights from industry icons and technology leaders shaping the future of PCB fabrication.
Sales: From Pitch to PO
From the first cold call to finally receiving that first purchase order, the July PCB007 Magazine breaks down some critical parts of the sales stack. To up your sales game, read on!
The Hole Truth: Via Integrity in an HDI World
From the drilled hole to registration across multiple sequential lamination cycles, to the quality of your copper plating, via reliability in an HDI world is becoming an ever-greater challenge. This month we look at “The Hole Truth,” from creating the “perfect” via to how you can assure via quality and reliability, the first time, every time.
- Articles
- Columns
- Links
- Media kit
||| MENU - pcb007 Magazine
Estimated reading time: 3 minutes
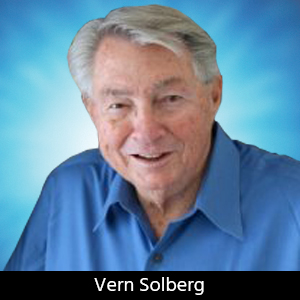
PCB Designers Notebook: Flexible Circuit Design
The flexible circuit was originally used as a conductive element for interfacing signals from one electronics assembly to another. Early designs often included nothing more than connectors at each end of the circuit. As surface mount devices became more available, companies began adding electronic functionality to the circuit. As far as attachment methods for surface mount devices, conductive adhesives can be used, but the soldering process most often is used for attaching devices to the copper circuit pattern. Depending on the assembly process, base material selection can be critical. While conductive adhesive and single-point soldering can be applied to polyester films, the dielectric material favored as a base for mass reflow soldering surface mount devices is polyimide film. Polyimide holds up better when exposed to the high temperatures needed to melt solder and complete the joining process.
Previously, I focused on base materials, with an overview of fabrication processes and SMT design recommendations for flexible circuits. This column explores alternative techniques for preparing a flexible circuit for efficient high-volume in-line surface mount assembly processing.
The handling and assembly of individual flexible circuits in an automated in-line process can be challenging, especially those with irregular shapes. Pallet fixtures can be developed to retain the circuit-in position throughout the various assembly process steps. However, these fixtures can be costly and typically require hand loading and unloading of the circuit assembly. Retaining the flexible circuit in a panel format can prove more efficient, especially when processing in high volume. In this format, a number of individual flexible circuit units can be uniformly arranged within the panel (much like the rigid circuits) and retained with narrow tabs that can be removed after assembly processing.
Although circuit outlines may have a non-uniform profile, the panel outline can be designed to furnish a uniform rectangular outline, and include the same features needed for rigid circuit-board assembly processing. The panel formatted circuit can be mounted to a less complex pallet fixture or furnished by the circuit fabricator with a rigid carrier panel backing ready for assembly processing. As for specifying the rigid backing, this material is typically a low-cost paper-based epoxy composite that provides the stiffness needed for automated conveyor transfer from machine to machine. This supports the circuit during solder-paste printing, component placement, reflow soldering and cleaning. The polyimide panel is retained to the rigid backing with adhesive in areas outside the individual circuit profiles. Following assembly, the narrow tab sections are cut allowing finished circuit assemblies to separate from the pallet carrier panel.
When dimensioning the circuit units and the panel, the Sectional Design Standard for Flexible Printed Boards, IPC-2223A recommends establishing primary datum features. The document also recommends the use of multiple datum features when the circuit has an extended profile requiring unique feature control. An example would be provisions for mounting or defining critical component locations. Use of multiple datum locations also will reduce or eliminate the effects of material shrinkage or process related distortion of flexible materials. One of the primary advantages of flexible circuit is that it can be folded or formed into non-planer shapes. With this capability, the circuit may not retain the same dimensional stability expected with rigid circuit structures. To compensate for these possibilities, fabrication specialists recommend allowing a greater positional tolerance between global datum features but specify a closer tolerance within each datum or component termination zone. While designing the circuit, designers should attempt to include sets of local fiducial features within each critical zone or extended portion of the circuit. This ensures that the automated placement of the surface mount devices within these separated or secondary areas will be as accurate as those in the primary area of the circuit.
Fiducial target size and shape recommended by equipment manufacturers is a round copper feature measuring 1.0 mm in diameter that is etched into the circuit pattern during fabrication. It is a good design practice to locate global or panel fiducials in a three-point grid-based datum system. The first fiducial is located at the 0-0 location. The second and third fiducials are located in the X and Y directions from 0-0 in the positive quadrant. The IPC recommends that all fine-pitch components have two additional local fiducials within or near the components mounting area. All fiducials also should have a solder mask opening that is large enough to keep the optical target free of solder mask. If solder mask or cover-layer materials overlap onto the optical target, vision alignment systems may be compromised due to insufficient contrast at the target site. In conclusion, before developing the panelized format for the flexible circuit, it is a good idea to work out optimum panel layout configuration with the fabricator.
More Columns from Designer's Notebook
Designers Notebook: Basic PCB Planning Criteria—Establishing Design ConstraintsDesigners Notebook: Layer Stackup Planning for RF Circuit Boards
Designers Notebook: Addressing Future Challenges for Designers
Designers Notebook: Impact of Advanced Semiconductor Packaging on PCB Stackup
Designers Notebook: Implementing HDI and UHDI Circuit Board Technology
Designer's Notebook: Heterogeneous Integration and High-density SiP Technologies
Designers Notebook: PCB Design and IPC-CFX for Assembly Automation
Designer’s Notebook: What Designers Need to Know About Manufacturing, Part 2