-
- News
- Books
Featured Books
- pcb007 Magazine
Latest Issues
Current IssueInventing the Future with SEL
Two years after launching its state-of-the-art PCB facility, SEL shares lessons in vision, execution, and innovation, plus insights from industry icons and technology leaders shaping the future of PCB fabrication.
Sales: From Pitch to PO
From the first cold call to finally receiving that first purchase order, the July PCB007 Magazine breaks down some critical parts of the sales stack. To up your sales game, read on!
The Hole Truth: Via Integrity in an HDI World
From the drilled hole to registration across multiple sequential lamination cycles, to the quality of your copper plating, via reliability in an HDI world is becoming an ever-greater challenge. This month we look at “The Hole Truth,” from creating the “perfect” via to how you can assure via quality and reliability, the first time, every time.
- Articles
- Columns
- Links
- Media kit
||| MENU - pcb007 Magazine
Estimated reading time: 3 minutes
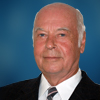
Contact Columnist Form
Karl's Tech Talk: Repeat Defects
Editor's Note: This column originally appeared in the June issue of The PCB Magazine.
In printed wiring board fabrication, random defects and so-called repeat (or repetitive) defects may be seen on several panels or plague an entire production run. These repeat defects are characterized by a distinct pattern. In some cases, the defects are always in the same location on the panel. In other cases, the defects may be noticed on a narrow strip on the panel in machine direction of the conveyorized spray process modules. Or, the repeat defect pattern is one where two defects always appear at the same distance from each other in machine direction; however, the absolute position of the two defects on the panel may vary, while the transverse direction location of the two defects pretty much stays the same. Then there are repeat defects that we would refer to as “pseudo repeat defects,” not because they did not fit the description of repeating defects that originate from the same problem source, but because they might appear on some panels, but not on all; or, they might show up for a while and then disappear.
To identify repeat defects by location, we used a clear polyester foil overlaid on top of the AOI inspected defective panel that bore the defect ink identification marks of the AOI. We then circled the defect locations on the polyester with a permanent marker ink and placed this defect template on subsequent defective panels. If the circles on the polyester foil fell in the same position as a defect on subsequent panels, this was a good indication that we had located a repeat defect. Today, some AOI software programs will allow you to do the same exercise more elegantly.
A repeat defect characterized by the fact that it is always in the same location on the panel is invariably linked to the photolithographic process. It could be a defective phototool. Or, it could originate from a piece of dirt trapped on the exposure frame. Whether such a defect appears on all panels or intermittently depends on the size of the imperfection and how good the contact was between the phototool and the photoresist for a particular exposure step. Of course, if a routine cleaning step of the phototool or the exposure frame removes the piece of dirt, or if it dislodges accidentally, then the defect no longer repeats.
If defects concentrate in a lane in machine direction, there are several potential sources for such defects. A damaged conveyor wheel could cause mechanical damage to the photoresist in the developer, or a partially plugged spray nozzle can cause highly localized, high-pressure spray impact in the developer or etcher resulting in over-development or over-etching.
Repeat defects related to hot roll lamination have two causes: either by a pit, indentation or cut in the rubber cover of the roll, or by a bump on the roll resulting from a nodule of foreign material on the otherwise smooth roll surface (see Figures 1 and 2 ).
A pit on the roll surface causes inadequate lamination pressure, which can cause an air void or low dry film adhesion that will not survive the rest of the process (see Figure 1). Bumps on the roll are usually caused by resist contamination. Such bumps increase lamination pressure, causing resist thinning. Such thin resist may not survive downstream processing. A thick bump with steep sidewalls may cause air voids or low adhesion around the edge of the bump as well as resist thinning (see Figure 2). Both types of roll defects will cause opens or nicks in etching applications, and shorts or excess copper in pattern plate applications.
Repetitive lamination voids can easily be detected. Most appear as light spots on laminated boards due to air under the resist. Thin resist spots without air voids are seen as dimples in the resist when observed at an angle. All defects caused by lamination rolls will repeat at the distance equal to the circumference of the roll. Note that, due to the spacing between boards, defects may not appear at the same location on each board.
Bumps on the lamination rolls caused by resist contamination can usually be removed by cleaning with isopropyl alcohol (caution: it’s flammable!). Problems caused by pits on the lamination rolls can be corrected permanently only by replacing the rolls. Some vendors offer repaired (recovered) rolls as a less costly alternative. Temporary repairs by filling the pits with a high temperature silicone adhesive sealant are possible, but they may fail within days because of thermal cycling.
Karl Dietz is President of Karl Dietz Consulting LLC. He is offering consulting services and tutorials in the field of Circuit Board & Substrate Fabrication Technology. Karl can be reached by e-mail at karldietz@earthlink.net or by phone at (001)- 919 870 6230.
More Columns from Karl's Tech Talk
Karl's Tech Talk: Digital Imaging UpdateKarl’s Tech Talk: Electronic Packaging Levels
Green Legislation and the Impact on Electronic Materials and Processes
Digital Imaging Revisited
Dry Film Photoresist Thickness Selection Criteria
Quick-Turn Circuit Board Shops
Optical Interconnects
Signal Loss