-
- News
- Books
Featured Books
- pcb007 Magazine
Latest Issues
Current IssueInventing the Future with SEL
Two years after launching its state-of-the-art PCB facility, SEL shares lessons in vision, execution, and innovation, plus insights from industry icons and technology leaders shaping the future of PCB fabrication.
Sales: From Pitch to PO
From the first cold call to finally receiving that first purchase order, the July PCB007 Magazine breaks down some critical parts of the sales stack. To up your sales game, read on!
The Hole Truth: Via Integrity in an HDI World
From the drilled hole to registration across multiple sequential lamination cycles, to the quality of your copper plating, via reliability in an HDI world is becoming an ever-greater challenge. This month we look at “The Hole Truth,” from creating the “perfect” via to how you can assure via quality and reliability, the first time, every time.
- Articles
- Columns
- Links
- Media kit
||| MENU - pcb007 Magazine
Estimated reading time: 6 minutes
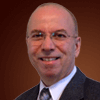
Bert's Practical Design Notes: Fiber Weave-Induced Timing Skew
A couple of times this year, fiber weave effect timing skew came up for discussion on the SI-List that many of us subscribe to. This is becoming more of an issue for many designers as bit rates continue to soar upwards.
For signaling rates of 5GB/s and beyond, it can actually ruin your day.
So what is fiber weave effect anyway, and why should we be concerned about it? Well, it’s the term commonly used when we want to describe the scenario in which a fiberglass-reinforced dielectric substrate causes timing skew between two or more transmission lines of the same length. Since the dielectric material used in the PCB fabrication process is made up of fiberglass yarns woven into cloth and impregnated with epoxy resin, it becomes non-homogeneous.
In high-speed differential signaling this is an issue because any timing skew between the positive (D+) and negative (D-) data converts some of the differential signal into a common signal component. Ultimately this results in eye closure at the receiver and contributes to EMI radiation.
The speed at which a signal propagates along a transmission line depends on the surrounding material’s relative permittivity (er), more commonly referred to in the PCB industry as dielectric constant (Dk). The higher the Dk, the slower the signal propagates along the transmission line. When one trace happens to line up over a bundle of glass yarns for a portion of its length, as illustrated in Figure 1, the propagation delay is different compared to another trace of the same length which lines up over mostly resin. This is known as timing or phase skew and is due to the delta Dk surrounding the respective traces.
Figure 1. Illustration of differential pair routing showing the cause of fiber weave effect timing skew.
Fiber weave effect is a statistical problem. Because the fiber weave pattern tends to run parallel to the x-y axis, any traces running the same way will eventually encounter a situation of worst-case timing skew if you build enough boards. It is not uncommon for PCB designs to have long parallel lengths of track routing without any bends or jogs. This is particularly true in large passive backplane designs. This was demonstrated by Intel after compiling more than 58,000 TDR and TDT measurements over two years. In 2007, Jeff Loyer et al [5] presented a DesignCon paper titled “Fiber Weave Effect: Practical Impact Analysis and Mitigation Strategies” where they published the data and proposed techniques to mitigate the effect of fiber weave skew. They showed statistically it is possible to have a worst-case timing skew of approximately 16ps per inch, representing a delta Dk of approximately 0.8.
You can calculate the timing skew by using the following equation:
Equation 1
Where:
tskew= total timing skew due to fiber weave effect length (sec)
Dkmax= dielectric constant of material predominated by fiberglass.
Dkmin= dielectric constant of material predominated by resin.
c = speed of light = 2.998E+8 m/s (1.18E+10 in/s)
A practical methodology you can use to estimate the minimum and maximum values of Dk is by studying the material properties available from PCB laminate suppliers. Consider two extreme styles of fiberglass cloths used in modern PCB laminate construction as illustrated by Figure 2.
Figure 2. Illustration showing a comparison of 106 vs 7628 weave pattern.
The loose weave pattern of 106 has the highest resin content of all the most popular weaves, while the tight weave pattern of 7628 has the lowest. Therefore, you could use the specified values of Dk for cloth styles 106 and 7628 to get Dkmin and Dkmax respectively. Once you have these and apply a tolerance, you can estimate the tskew .
Example:
Assume FR-4 material; one inch of fiber weave effect; Dk106= 3.34(+/-0.05) and Dk7628= 3.97(+/-0.05), then timing skew is calculated as follows:
Modern serial link interfaces use differential signaling on a pair of transmission lines of equal length for interconnect between two points. In a DesignCon 2007 paper, “Losses Induced by Asymmetry in Differential Transmission Lines” by Gustavo Blando et al [6], they showed how intra-pair timing skew between the positive (D+) and negative (D-) data caused an increase in the differential insertion loss profile due to timing induced resonances. These resonances manifest themselves as dips in the differential insertion loss profiles of the channel.
Figure 3 shows the results from an Agilent ADS circuit simulation of a PCIe Gen2 channel model running at 5GT/s. The eye diagrams are at the receiver after approximately 30 inches of track length chip to chip.
Figure 3. Agilent ADS simulation showing timing induced resonances and the effect on received eye due to various lengths of fiber weave effect. Click here to see larger image of simulations.
The channel model was parameterized to allow for adjusting the fiber weave effect length as required. As you can see when the length of the fiber weave effect induced skew increases from 0 to 12.7 inches, the fundamental frequency nulls in the respective differential insertion loss plots decrease. These nulls occur at the fundamental frequency (fo) and every odd harmonic.
As you can see, the eye begins to show some degradation at 5.6 inches and starts to distort significantly after only 7.8 inches of fiber weave effect. At 12.7 inches, fo equals the Nyquist frequency of the data rate (in this case 2.5GHz) and the eye is totally closed.
You can predict the resonant frequency ahead of time and use it to gain some intuition before you simulate and to validate the results afterwards. If you know the total intra-pair timing skew, then fo is calculated using the following equation:
Equation 2
Where:
fo = resonant frequency
tskew= total intra-pair timing skew
Example:
Using tskew= 16 ps/in we calculated in the previous example, and using 12.7 inches from the last simulation results in Figure 3, the fundamental resonant frequency null is:
Some common ways to mitigate the fiber weave effect is to route any long traces on a 10 degree angle with respect to the x-y axis, or purposely angle the panel 10 degrees during fabrication [5]. Both methods will work, but they are a hassle to implement and are expensive.
Fortunately recent advancements in technology have resulted in prepreg sheets with a flatter, more uniform distribution of the weave pattern. Isola’s FR408HR material, for example, has alternatives for some of the more popular weaves; 1086 replaces 1080; 106 is replaced by 1067 and two plies of 3313 replaces 7628.
You can find more details of this phenomena, plus a novel way to model and simulate fiber weave effect, in a recent white paper I published titled, “Practical Fiber Weave Effect Modeling” located on my Web site.
References
[1] Bert Simonovich, “Practical Fiber Weave Effect Modeling,” Issue 2.0, Jan/10/2011
[2] Park Electrochemical Corp., www.parkelectro.com
[3] Isola-group, www.isola-group.com/index.php
[4] Gary Brist et al, “Woven Glass Reinforcement Patterns,” Printed Circuit Design & Manufacture, Nov. 2004
[5] Jeff Loyer et al, “Fiber Weave Effect: Practical Impact Analysis and Mitigation Strategies”
[6] Gustavo Blando et al, “Losses Induced by Asymmetry in Differential Transmission Lines”
[7] Eric Bogatin, http://bethesignal.net/blog, Blog post: “4/9/09 A new glass weave skew solution”
[8] Agilent Technologies, EEsofEDA, Advanced Design System, 2009 Update1 software.
[9] SI-list Mailing Archive, www.freelists.org/archive/si-list
Bert Simonovich was born in Hamilton, ON, Canada. He received his Electronic Engineering Technology diploma from Mohawk College of Applied Arts and Technology, Hamilton, ON, Canada in 1976. Over a 32-year career, working as an Electronic Engineering Technologist at Bell Northern Research and later Nortel, in Ottawa, Canada, he helped pioneer several advanced technology solutions into products. He has held a variety of engineering, research and development positions, eventually specializing in signal integrity and backplane architecture for the last 10 years. He is the founder of Lamsim Enterprises Inc., where he continues to provide innovative signal integrity and backplane solutions to clients as a consultant. With three patent applications and two patent grants to his name, he has also (co)authored several publications, including an award winning DesignCon2009 paper related to PCB via modeling. His current research interests include signal integrity, high-speed characterization, and modeling of high-speed serial links associated with backplane interconnects. To contact Bert, click here.
More Columns from Bert's Practical Design Notes
Practical Modeling of High-Speed Backplane ChannelsObsessing over Conductor Surface Roughness: What’s the Effect on Dk?
The PDN Bandini Mountain and Other Things I Didn’t Know I Didn’t Know
Bert's Practical Design Notes: Accelerating the SI Learning Curve - Bogatin's SI Academy
Bert's Practical Design Notes: Are Guard Traces Worth It?
Bert's Practical Design Notes: Perils of Lumped Via Modeling
Bert's Practical Design Notes: The "Stubinator" vs. Back-Drilling
Backplane High-Level Design: The Secret to Success