-
- News
- Books
Featured Books
- pcb007 Magazine
Latest Issues
Current IssueInventing the Future with SEL
Two years after launching its state-of-the-art PCB facility, SEL shares lessons in vision, execution, and innovation, plus insights from industry icons and technology leaders shaping the future of PCB fabrication.
Sales: From Pitch to PO
From the first cold call to finally receiving that first purchase order, the July PCB007 Magazine breaks down some critical parts of the sales stack. To up your sales game, read on!
The Hole Truth: Via Integrity in an HDI World
From the drilled hole to registration across multiple sequential lamination cycles, to the quality of your copper plating, via reliability in an HDI world is becoming an ever-greater challenge. This month we look at “The Hole Truth,” from creating the “perfect” via to how you can assure via quality and reliability, the first time, every time.
- Articles
- Columns
- Links
- Media kit
||| MENU - pcb007 Magazine
Estimated reading time: 1 minute
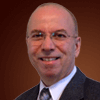
Obsessing over Conductor Surface Roughness: What’s the Effect on Dk?
You know you have an obsession when you are flying six miles over Colorado and you look out the window at the beautiful scenery, and all you can think about is how the rocky mountain topology reminds you of conductor surface roughness! Well, call me obsessed, because that’s exactly what I thought on my way to DesignCon 2017 in Santa Clara, California.
For those of you who know me, you know that I have been researching practical methods to model conductor surface roughness and its effect on insertion loss (IL). I have presented several papers on the subject over the last couple of years. It’s one of my pet projects. This year at DesignCon, I presented a paper titled "A Practical Method to Model Effective Permittivity and Phase Delay Due to Conductor Surface Roughness."
Everyone involved in the design and manufacture of PCBs knows that one of the most important properties of the dielectric material is the relative permittivity (εr), commonly referred to as dielectric constant (Dk). But in reality, Dk is not constant at all. It varies over frequency as you will see later.
We often assume the value reported in manufacturers’ data sheets is the intrinsic property of the material. But in actual fact, it is the effective dielectric constant (Dkeff) generated by a specific test method. When you compare simulation against measurements, you will often see a discrepancy in Dkeff and IL, due to the increased phase delay caused by surface roughness. This has always bothered me. For a long time, I was always looking for ways to come up with Dkeff from data sheet numbers alone. Thus the obsession and motivation for my recent research work.
Since phase delay, also known as time delay (TD), is proportional to Dkeff of the material, my theory was that the surface roughness profile decreases the effective separation between parallel plates, thereby increasing the electric field (e-field) strength, resulting in additional capacitance, which accounts for an increase in effective Dk and TD.
To read this column, which appeared in the March 2017 issue of The PCB Design Magazine, click here.
More Columns from Bert's Practical Design Notes
Practical Modeling of High-Speed Backplane ChannelsThe PDN Bandini Mountain and Other Things I Didn’t Know I Didn’t Know
Bert's Practical Design Notes: Accelerating the SI Learning Curve - Bogatin's SI Academy
Bert's Practical Design Notes: Are Guard Traces Worth It?
Bert's Practical Design Notes: Perils of Lumped Via Modeling
Bert's Practical Design Notes: The "Stubinator" vs. Back-Drilling
Backplane High-Level Design: The Secret to Success
Bert's Practical Design Notes: Why Backplane Architecture is Crucial