-
- News
- Books
Featured Books
- pcb007 Magazine
Latest Issues
Current IssueInventing the Future with SEL
Two years after launching its state-of-the-art PCB facility, SEL shares lessons in vision, execution, and innovation, plus insights from industry icons and technology leaders shaping the future of PCB fabrication.
Sales: From Pitch to PO
From the first cold call to finally receiving that first purchase order, the July PCB007 Magazine breaks down some critical parts of the sales stack. To up your sales game, read on!
The Hole Truth: Via Integrity in an HDI World
From the drilled hole to registration across multiple sequential lamination cycles, to the quality of your copper plating, via reliability in an HDI world is becoming an ever-greater challenge. This month we look at “The Hole Truth,” from creating the “perfect” via to how you can assure via quality and reliability, the first time, every time.
- Articles
- Columns
- Links
- Media kit
||| MENU - pcb007 Magazine
Estimated reading time: 5 minutes
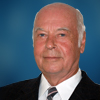
Contact Columnist Form
PCB Industry 2011: A Year in Review
Editor's Note: This article originally appeared in the December 2011 issue of The PCB Magazine.
Welcome to one person’s anecdotal, myopic view of events and trends in the PCB industry during this past year. The year started with encouraging, double-digit growth, which flattened out in the second half of the year. The total value of rigid and flex circuit boards produced in 2011 is about $55 billion. About 40% of the boards were produced in China, 17% in Japan, about 13% in Taiwan and 11% in South Korea. Europe and the U.S. accounted for less than 10% each. This is not much different than the previous year. Nevertheless, there is a continuing trend of production shifts to Asia.
The top three circuit board shops in the world remained neck-and-neck: Unimicron, Ibiden, and Nippon Mektron. Production capacity in Europe and the U.S. continued to shrink, with about 280 shops remaining in Europe and 340 in the U.S. Only one European-owned company (AT&S) was in the ranks of the top 20 PCB producers worldwide.
The microvia board (HDI) production that Japan dominated for years has now found competition of equal size in China. Most of the larger Chinese PCB shops are still Taiwanese owned, as in previous years. However, there are several large, growing Chinese PCB shops such as CCTC and the Founder Group whose roots go back to the Chinese University system. U.S.-owned companies still remain well represented in China through companies such as Multek, Viasystems, and M-Flex.
Europe has seen a steady decline of PCB output from 2000 to 2009, but it enjoyed an increase of 21% (over the previous year) in 2010, then continued double-digit growth in the first half of 2011 that flattened out in the second half. Germany accounted for over 40% of the European production. All other European countries accounted for less than 10% each. If one focuses on the German-speaking European countries (Germany, Austria, Switzerland), they produce over 75% of the European PCBs. The end-uses are dominated by automotive, industrial and some photovoltaic and medical applications.
The top European producers are Wuerth, AT&S, Schweizer Electronic AG, Multek and KSG. KSG Leiterplatten emerged from an East German (communist) conglomerate to a fast-growing PCB producer, located in the state of Saxony. The main production site of Ruwel, in Geldern, Germany, has been taken over by Unimicron. Unimicron will do prototypes, quick-turn, and small-scale production as well as product and process development at Geldern. Another former Ruwel site in the town of Wetter survived through a management buy-out and is doing well due to its specialization in rigid-flex. There are other shops that have weathered the exodus to Asia, such as a small shop that produces only double-sided boards. Rising production costs in China and high shipping costs have allowed this specialized shop to survive.
Europe and North America are facing a dwindling base of suppliers to the PCB industry. Not many years ago, Europe had a fair number of laminate (base material) suppliers. Now only Isola (Germany) and Panasonic (Austria) remain.
North American PCB producers serve mainly the military/aerospace market and the computer (and computer peripherals) industry.
Rising raw material costs have led to modest PCB price increases. Copper peaked at $4.50/pound in early 2011. It is now selling at about $3.00/pound. Tin prices peaked at about the same time at $15.00/pound and have come down since then to about $9.00. Precious metal price movements caused shifts in surface finishing selections. The dominant precious metal finishes are still ENIG (electroless nickel/immersion gold), ENEPIG (electroless nickel/electroless palladium/immersion gold) and electrolytic nickel/electrolytic gold. The popularity of ENEPIG shifts with the price of palladium. This finish is more expensive than ENIG, but is sometimes preferred as an insurance against the dreaded black pad which has plagued ENIG. A lesser-known finish, ASIG (autocatalytic silver/immersion gold) has gotten more attention recently. As gold and palladium prices soared, several companies switched to immersion silver. Finally, some companies that used to run immersion silver switched to OSPs (organic solderability preservatives).
Several PCB companies have developed specialty application boards, such as those that feature cavities with embedded passive and active devices, which have become more prevalent. In Japan, several companies practice embedding discrete passive devices. AT&S produces boards that use its patented embedded component technology, as does Schweizer Electronic AG. Another specialty PCB type are IMSs (insulated metal substrates). These typically have a thick metal layer that serves as heat sink, for applications such as high-performance LED (light emitting diodes) packaging. These devices produce a significant amount of heat that must be dissipated.
Some companies find it prudent to diversify into unfamiliar technologies such as photovoltaics and printed electronics. These emerging technologies are not entirely new territory to PCB shops that have expertise in metallization and screen printing. An example of a PCB company that ventured into photovoltaics is Unitech (Taiwan), offering solar cell products. Schweizer Electronic AG, which is a leading supplier of PCBs to the photovoltaic industry, announced an expansion into the energy field with the foundation of Schweizer Energy Pte. Ltd., headquartered in Singapore.
Printed Electronics is a less well defined field which attracts the attention of PCB makers. Applications include organic photovoltaics, flex displays, OLED lighting, printed RFIDs, printed memory, organic sensors, flex batteries, “smart textiles” and a variety of rather obscure uses.
Technological advances in the PCB industry have been mostly evolutionary in 2011. Via-fill copper plating has been perfected, several other innovations in plating such as the use of vertical continuous plating equipment and inert anodes have become more common.
The technology of LDI (laser direct imaging) also has become mainstream. It is useful to view LDI, i.e., the use of a laser tool to expose photoresist, pixel by pixel, as only one example of digital imaging. Lasers are also used in digital patterning by selectively ablating metal, or metal etch resist (Siemens process), or dielectric (e.g., Viking Process by Amkor). Not all light sources used in digital imaging are lasers. ORC (formerly Pentax) offers an imaging tool that makes use of DMD™ micromirror arrays and a high-pressure mercury lamp light source (405nm wavelength). Other digital imaging tools that make use of DMDs™ include Hitachi’s DE imagers that use a 405nm diode laser, the Miva 2600X (MIVA Technologies GmbH) that uses an LED light source, the Ball Semiconductor Direct Imager, Maskless Lithography’s digital imaging tool that uses a mercury arc light source, and the DMD™-based digital imaging tool from Aiscent Technologies Inc. (Canada).
Ink jetting of an etch resist pattern and of soldermask is being offered but has not yet made significant inroads. On the other hand, ink jetting of legend print is now widely accepted and has a broad base of suppliers.
Karl Dietz is president of Karl Dietz Consulting LLC, offering consulting services and tutorials in the field of Circuit Board & Substrate Fabrication Technology. His column, Tech Talk, appears monthly in The PCB Magazine. Contact Dietz by e-mail at karldietz@earthlink.net or phone (001)- 919 870 6230.
More Columns from Karl's Tech Talk
Karl's Tech Talk: Digital Imaging UpdateKarl’s Tech Talk: Electronic Packaging Levels
Green Legislation and the Impact on Electronic Materials and Processes
Digital Imaging Revisited
Dry Film Photoresist Thickness Selection Criteria
Quick-Turn Circuit Board Shops
Optical Interconnects
Signal Loss