-
- News
- Books
Featured Books
- pcb007 Magazine
Latest Issues
Current IssueInventing the Future with SEL
Two years after launching its state-of-the-art PCB facility, SEL shares lessons in vision, execution, and innovation, plus insights from industry icons and technology leaders shaping the future of PCB fabrication.
Sales: From Pitch to PO
From the first cold call to finally receiving that first purchase order, the July PCB007 Magazine breaks down some critical parts of the sales stack. To up your sales game, read on!
The Hole Truth: Via Integrity in an HDI World
From the drilled hole to registration across multiple sequential lamination cycles, to the quality of your copper plating, via reliability in an HDI world is becoming an ever-greater challenge. This month we look at “The Hole Truth,” from creating the “perfect” via to how you can assure via quality and reliability, the first time, every time.
- Articles
- Columns
- Links
- Media kit
||| MENU - pcb007 Magazine
Estimated reading time: 8 minutes
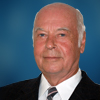
Contact Columnist Form
Karl’s Tech Talk: Color in Photoresists and Soldermasks
Editor's Note: This article originally appeared in the January 2012 issue of The PCB Magazine.
I always had a fascination with colorants, as a tool for artistic expression or the basis of a growing chemical industry in the 19th century, as the testing ground for an emerging patent system, or the gateway to new synthetic methods and chemical innovations. It was my privilege to have worked in the field of dyestuffs and colored pigment research before entering the world of electronics, where I was surprised and puzzled by the presence and role of colorants in photopolymer formulations. Since the functionality of color in this application was not readily apparent to a novice like me, I did some digging and came up with the following:
Color in Soldermasks and Coverlays
The traditional color for soldermasks has been green (Figure 1), maybe for historical reasons only or because of the good contrast the color of copper (see discussion below). However, there have been other colors, notably black and white. One application for white soldermask is packaging of LEDs that emit white light. Non-white soldermask will affect the hue of the emitted light which is undesirable. Circuit boards and components cover with black soldermask, coverlay, protective coating seem to appeal to Apple Inc. which perceives an aesthetic value in such appearance.
Figure 1: Example of a popular green dye stuff.
Photoresist Color as Visual Aid in the PWB Fabrication Process
Colorants have been used in photoresist formulations to assist the human eye in the resist application steps to:
- Better visually judge the uniformity and completeness of substrate coverage with liquid photoresists;
- Make it easier to align dry film resist to a panel on a hot roll laminator;
- Create an optical image counterpart ("print-out image") to the latent polymerization pattern for visual verification of image registration; and
- Have a good visual contrast of the developed resist pattern for easier inspection ("contrast to copper").
Early liquid formulations were either colored or had to be dipped into a colorant solution after the resist coating. The depth of color could be used as an indicator of resist thickness distribution, and coating defects, such as pinholes, were easier detected. This function of color was less important with dry-film photoresists, but color helped to judge the proper placement of the resist on the board and to make necessary adjustments.
First, there was a variety of photoresist colors in use, but blue and green shades have become most popular. The human eye perceives these hues to give the best contrast to the pinkish color of a copper surface. The pink-orange of copper and the bluish-green tints of the resist happen to be close to a pair of colors called complementary, a pair of colors which is perceived by the human brain to show good contrast. In addition, one could argue that the eye is most sensitive in the 550-nm (green) wavelength range. Typical colorants belong to the family of triarylmethane dyes or pigments. Pigments are less soluble than dyes and tend to have better light fastness. Examples of triarylmethane dyes are crystal violet and Victoria Blue (Figure 2 and 3).
Figure 2: Crystal violet.
Figure 3: Victoria blue.
After exposure, the resist has a "latent" image of polymerized and unpolymerized areas without visual contrast, unless the formulation contains ingredients that develop color or fade away upon exposure. The visual contrast of exposed areas to unexposed areas is helpful to production operators to verify that boards have been exposed, or to check the registration of the image relative to tooling holes or conductor vias. If exposed resist has a deeper color it is referred to as a print-out image. Conversely, if the exposed color is lighter, it is called a fade-out image. This fade-out characteristic is sometimes also referred to as photofugitive.
A typical color former or color precursor is a "leuco" (white) dye from the family of triarylmethane dyes. The leuco form may be a reduced, colorless compound (Figure 4) which oxidizes when exposed to form the color. Leuco crystal violet and leuco malachite green are examples.
Figure 4: Example of a colorless dye precursor.
To form a fade-out image, a color or color precursor needs to be chemically altered during the exposure process to non-colored, or non-colorforming species. An example of such chemistry is found in the familiar diazo phototool chemistry: a stabilized diazonium salt, part of a color precursor package, loses its diazonium group (N2) during exposure to form a phenol derivative which is incapable of linking with a coupler molecule to form the azo dye in the ammoniacal developer (Figure 5).
Figure 5: Exposure of the diazonium salt results in nitrogen loss and formation of phenol which cannot couple to form a dye.
Both approaches, print-out and fade-out images, are being offered in commercial products, but the print-out image seems to be more prevalent. However, a fade-out image may have the advantage of avoiding or minimizing a potential problem in some applications: Occasionally, colored exposed resist leaves an undesirable stain after stripping on the substrate. This is particularly objectionable in photochemical machining applications and a fade-out image may be the answer to this problem.
It is important that dyes and pigments have a low-absorption "window" in the 350 to 410 nm region so that little radiation energy is taken away from the photoinitiation process of the radical polymerization. Since all dyes show some absorption in this UV region, they tend to detrimentally affect the photospeed of the resist, so that depth of color and print-out image may have to be traded for higher photospeed.
Some dyes actually help initiate the photopolymerization. In dye-sensitized systems, dyes can play a role in an electron transfer process, typically an electron transfer from an activator to a photoexcited dye. However, these systems are not commonly used in photoresists because they lack adequate shelf life. Dyes capable of such electron transfers include structures from the families of xanthene, acridinium, phenazine and thiazene dyes.
Photoresist Color in Automatic Exposure Systems and Laser Direct Imaging (LDI)
Automatic exposure systems which use CCD cameras (charged coupled devices) for board-to-photomask alignment, rely on a minimum transparency of the colored photoresist for this alignment process to function properly. First, yellow light shines through registration holes and is detected on the other side by CCD cameras. Based on the coordinate information of the registration hole, the phototool is then moved in the right position relative to the holes. This registration process is typically done in two steps, a rough pre-registration, followed by a precision adjustment. The registration hole also serves as reference point for front-to-back registration.
When LDI exposure machines were first developed, tool suppliers quickly learned that predrilling boards for registrations purposes was not always acceptable to the fabricator. They prefer to position this relatively dirty process after the exposure, development and etching processes (post-etch-punch). An alternative was to use colored fiducials to aid front-to-back registration.
This is achieved through the “print-out image” characteristic of the photoresist, a color change of the resist during exposure that makes the latent polymerized features visible to the eye. The panel is placed on the machine’s table for topside exposure. As vacuum is applied, the markers, typically non-laser light sources, placed inside the table start to image the targets on the bottom side of the panel. CCD cameras then align the panel to the table as the panel moves in and the top-side is imaged during the reverse movement. After flipping the panel, CCD cameras locate the target marks on the bottom side (now the top side). Registration and imaging follow.
Figure 6: Marking the bottom-side registration target (courtesy: Orbotech).
Figure 7: Imaging the top-side (courtesy: Orbotech).
Figure 8: Locating the bottom-side targets, registration and bottom-side imaging (courtesy: Orbotech).
Photoresist Color and Automatic Optical Inspection (AOI)
Some PWB fabricators like the option of inspecting the developed resist image on the copper clad laminate before etching, a procedure that can easily cause resist pattern damage due to handling. Nevertheless, this inspection may be useful in a troubleshooting mode, and the resist color becomes an issue in such an inspection step. In this case one has to distinguish between reflectance type AOIs and (laser) fluorescence mode AOIs.
Regarding the reflective inspection, blue/green dry films which absorb strongly around 660 nm work well. The filter used in the AOI is orange, and the resist appears "black" to the machine while the copper appears bright. Red-colored photoresists are a rare species nowadays and are more difficult to inspect, but can be handled with a green filter in the AOI. One application challenge is in tent and etch board inspection. If the resist surface curves down into the hole and the resist surface is shiny, contrast degrades because the resist sends a reflection into the diffusive light gatherer, thus producing a signal relatively high versus the copper. Obviously, a matte resist surface will be less of a problem. Very thin resists also present a challenge because, for a given level of coloration, thinner resists absorb less than thicker resists (see Beer's Law). However, with some fine-tuning, reflectance mode AOIs seem to have no problems distinguishing resist from reflectant copper.
There is an interesting, special situation regarding AOI testing in the reflective mode in the presence of resist: the inspection of innerlayers after etching, with a permanent innerlayer resist remaining on top of the copper traces. To the best of our knowledge, there is no volume production experience for this scenario. Basically, the reflectance of the copper through the resist has to be high enough to provide sufficient contrast to the lower reflectance of the adjacent dielectric. If the coloration of the resists is low, e.g., to gain acceptable photospeed of the resist, this condition is generally met. However, what can interfere is a highly reflective, shiny resist surface.
Regarding the fluorescence mode AOI, the inspection of a resist image on solid copper, before etching, has not presented problems. Fluorescence is stimulated by a 442-nm (He-Cd) laser. The normal point of inspection is a board after etch and strip. The dielectric, sometimes formulated to include fluorescence enhancers, emits fluorescence in the 525-575 nm region. The copper, on the other hand, will reflect a good portion of the 442-nm light, and, to make the copper look "black", the AOI's detector is filtering out this wavelength. For resist inspectability on copper, the resists have to absorb in the 442-nm region and fluoresce in the 525-575 nm range. Experience shows that they do. The "window dyes" of the photoresist have an appreciable absorption around 442 nm (and above) and may assist in this process or, at least, won't interfere.
Karl Dietz is President of Karl Dietz Consulting LLC. He is offering consulting services and tutorials in the field of Circuit Board & Substrate Fabrication Technology. Contact Dietz by e-mail at karldietz@earthlink.net or phone (001)- 919 870 6230.
More Columns from Karl's Tech Talk
Karl's Tech Talk: Digital Imaging UpdateKarl’s Tech Talk: Electronic Packaging Levels
Green Legislation and the Impact on Electronic Materials and Processes
Digital Imaging Revisited
Dry Film Photoresist Thickness Selection Criteria
Quick-Turn Circuit Board Shops
Optical Interconnects
Signal Loss