-
- News
- Books
Featured Books
- pcb007 Magazine
Latest Issues
Current IssueInventing the Future with SEL
Two years after launching its state-of-the-art PCB facility, SEL shares lessons in vision, execution, and innovation, plus insights from industry icons and technology leaders shaping the future of PCB fabrication.
Sales: From Pitch to PO
From the first cold call to finally receiving that first purchase order, the July PCB007 Magazine breaks down some critical parts of the sales stack. To up your sales game, read on!
The Hole Truth: Via Integrity in an HDI World
From the drilled hole to registration across multiple sequential lamination cycles, to the quality of your copper plating, via reliability in an HDI world is becoming an ever-greater challenge. This month we look at “The Hole Truth,” from creating the “perfect” via to how you can assure via quality and reliability, the first time, every time.
- Articles
- Columns
- Links
- Media kit
||| MENU - pcb007 Magazine
Estimated reading time: 3 minutes
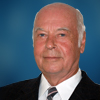
Contact Columnist Form
Karl’s Tech Talk: Advances in Copper Plating, Part B
Editor's Note: This article was originally posted in the Mach 2012 issue of The PCB Magazine.
Acid copper (electroplating) for electronic applications has seen many advances over the decades which include the introduction of the high through bath with lower copper and higher acid concentration, the development of proprietary organic additives for improved leveling, grain refining, and ductility, improved bath control methods such as CVS and many more. Last month’s Tech Talk column (Advances in Copper Plating, Part A) began a two-part series dealing with more recent innovations and evolutionary improvements in copper plating by introducing the topics of inert anodes and plating “shut” blind vias and through-holes. The order in which the topics are presented is somewhat arbitrary and not meant to suggest order of importance.
Conveyorized Plating Modules
There are a number of variables to be controlled to minimize plating non-uniformity:
- Improve primary current distribution (shielding, anode/cathode sizing)
- Controlling throwing power (plating additives, current density, Cu/acid ratio)
- Anode size control (use of inert anodes)
- Bath movement (use of eductors), and
- Uniform plating cell environment (use of conveyorized platers)
The latter addresses plating non-uniformity due to the position of a particular board location relative to the plating cell environment or cell geometry in plating baths with stationary plating racks. Plating differences due to location can be smoothed out in the more uniform plating cell environment of so called continuous or conveyorized platers. There are continuous plating lines that convey the boards horizontally; others convey the boards vertically. Such systems had to develop sophisticated transport mechanisms (clamp and release), especially for thin boards. Vertical continuous platers have become more popular in recent years for plating more complex boards such as HDI boards. Figure 1 shows such a vertical continuous plater (Example: VCP from Process Automation International Ltd. (PAL), Hong Kong, in alliance with Marunaka Kogyo Co. Ltd., Japan, and Applied Equipment Ltd., Taiwan. Proponents of this type point out the following advantages vs. horizontal conveyorized platers: better side-to-side uniformity, less air entrapment in microvias, lower cost, and smaller footprint. Figure 1: Vertical continuous plating (VCP) equipment for panel and pattern plating.Figure 2 shows a popular horizontal plating module (source: Atotech).
Figure 2: Horizontal plater example: Atotech’s horizontal pulse plating system. Pulse Plating
Pulse plating (specifically, periodic reverse pulse plating) has started to make inroads into acid copper plating about twenty years ago, but has really caught on in recent years as rectifiers became more affordable and reliable and as microvia and through-hole plating has become more challenging due to smaller via diameters and higher aspect ratios. Figure 3 shows a typical pulse plating cycle with its different segments and gives definitions of the different current flows and time segments of the cycle.
Figure 3: Generic PPR Waveform. It is interesting to note that the duty cycle, i.e., the actual plating time cycle is interrupted by reverse plating (or deplating) and off-time, which altogether would suggest that plating would be slower compared to conventional DC plating in which all the time is dedicated to plating (or duty cycle). However, pulse plating typically results in faster plating because it interferes with the formation of a polarized layer on the surface of the board, thus helping the faster replenishment of copper ions. The following are the key features of pulse plating when compared to DC plating:
- Better surface uniformity
- Better throwing power (more uniform through-hole/microvia plating)
- Faster plating (even though there are short time intervals in each pulse cycle when no plating happens; the pulse changes the diffusion layer and enhances copper ion replenishment at the board surface)
- Organic additive systems had to be tailored to pulse plating
- Rectifiers are more expensive than DC rectifiers
- Cell geometry is very important
Karl Dietz is president of Karl Dietz Consulting LLC. He is offering consulting services and tutorials in the field of circuit board and substrate fabrication technology. Karl can be reached by e-mail at karldietz@earthlink.net or phone (001)- 919 870 6230.
More Columns from Karl's Tech Talk
Karl's Tech Talk: Digital Imaging UpdateKarl’s Tech Talk: Electronic Packaging Levels
Green Legislation and the Impact on Electronic Materials and Processes
Digital Imaging Revisited
Dry Film Photoresist Thickness Selection Criteria
Quick-Turn Circuit Board Shops
Optical Interconnects
Signal Loss