-
- News
- Books
Featured Books
- smt007 Magazine
Latest Issues
Current IssueSupply Chain Strategies
A successful brand is built on strong customer relationships—anchored by a well-orchestrated supply chain at its core. This month, we look at how managing your supply chain directly influences customer perception.
What's Your Sweet Spot?
Are you in a niche that’s growing or shrinking? Is it time to reassess and refocus? We spotlight companies thriving by redefining or reinforcing their niche. What are their insights?
Moving Forward With Confidence
In this issue, we focus on sales and quoting, workforce training, new IPC leadership in the U.S. and Canada, the effects of tariffs, CFX standards, and much more—all designed to provide perspective as you move through the cloud bank of today's shifting economic market.
- Articles
- Columns
- Links
- Media kit
||| MENU - smt007 Magazine
Estimated reading time: 5 minutes
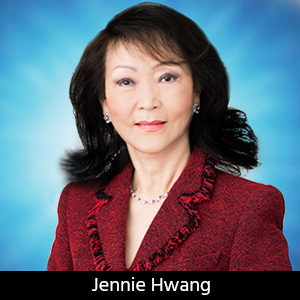
SMT Perspectives and Prospects: 100 Points on Lead-Free Performance and Reliability, Part 2
Editor's Note: This column originally appeared in the July 2012 issue of SMT Magazine.
Continuing last month’s list, this column wraps up the points on lead-free properties, performance, and reliability, retrospectively, and prospectively. Each of the summary points will not be discussed or elaborated. However, inquiries about any of the points for scientific base, rationale, and further discussion are welcome.
51. The SAC system has been successful in serving the intended function for most applications, but not all.
52. The SAC system encompasses compositions including: SAC405, SAC305 and in-between of 3 to 4% Ag and of 0.5 to 1.5% Cu; low-Ag content of SAC system; and all doped SAC compositions.
53. Low-Ag compositions denote the SACs containing less than 3% Ag, such as SAC105, SAC0803, etc.
54. Doped SAC compositions, in a practical sense, denote those incorporated with a non-alloying element(s) in a small dosage.
55. SnCu system has been successful in serving the intended function in wave soldering for some applications.
56. SnCu system denotes compositions of SnCu in various percentage of Cu, as well as the doped SnCu compositions.
57. Doped SnCu compositions denote those SnCu compositions incorporated with a non-alloying element(s) in a small dosage.
58. Effects of higher process temperature imposed by SAC solders should be considered in the areas of PCB bare board, components, flux chemistry, solder joints (including voids), and PCB surface finish, separately and collectively.
59. Higher process temperature contributes to PCB de-lamination, blistering, warp, PCB discoloration, large PCB sagging during reflow, Cu pad peel strength reduction, and pad-lifting.
60. Higher process temperature contributes to PCB through-hole barrel crack, Cu dissolution, PCB Z-axis thermal expansion (weakened through-hole via).
61. Higher process temperature could cause PCB intrinsic interconnect open, electroless Cu separates from the post, electrolytic Cu separates from electroless Cu, and electroless Cu cohesive failure.
62. Effects of higher process temperature on PCB surface finish (solderability and intermetallic compounds) should be considered.
63. Pad cratering was hardly observed in SnPb soldering.
64. Pad cratering and pad lifting should be differentiated. They have different phenomena and causations.
65. Effects of higher process temperature on the probability of electro-migration issue should be taken into consideration.
66. A higher process temperature may adversely affect aluminum electrolytic capacitors.
67. Defects or damages of MLCC should be avoided.
68. Heat-sensitive components should be protected when a high assembly process temperature is required.
69. Effects of higher process temperature on “internal” solder joints of modules or subsystem should be considered.
70. BGA solder balls drop at package interface must be avoided.
71. A higher process temperature may induce BGA/CSP delamination between the layers of interposer beneath the die.
72. Effects of higher process temperature on connector plastic housing changes (dimensional, functional) should be considered.
73. A higher process temperature may increase Z-axis thermal expansion, which, in turn, may induce undue effects on components during cooling (compressive stress).
74. Higher process temperatures exert adverse effects on component co-planarity (BGA).
75. Higher process temperatures on component moisture sensitivity should not be ignored. At a higher process temperature, components may have to be dried to a lower moisture content to avoid package crack.
76. Effects of higher process temperature on flux chemistry (user) should not be underestimated.
77. Higher process temperature impacts on flux formulation (supplier).
78. For cleaning, higher process temperature affects the ability to clean flux residue.
79. A higher process temperature may contribute to potential electrochemical failure (flux contaminants adsorbed onto or absorbed into the substrate).
80. Higher strain created by a higher process temperature may be imposed on solder joint during cooling.
81. A higher process temperature may contribute to solder joint voids. A higher process temperature can promote (CuNi)6Sn5 compound at the bonding interface, resulting in additional voids.
82. Head-on-pillow open joint was hardly observed in SnPb soldering.
83. Head-on-pillow occurs with SAC system.
84. Higher process temperature causes more oxidation on solder pads after the first reflow, which particularly affects OSP surface finish.
85. Higher process temperature increases the propensity to tin whisker phenomenon when a metal coating used (such as Sn or SnCu or SnAgCu) is prone to tin whisker.
86. Higher process temperature aggravates black pad problem.
87. Higher process temperature may incur wave soldering disadvantages (dross, equipment).
88. Higher process temperature affects the reflow oven (working life, residue accumulation).
89. Higher process temperature increases residual stress.
90. Higher process temperature increases energy cost.
91. Higher process temperature imposes higher demands on rework-ability.
92. Using a marginal process temperature will result in production defects and or potential reliability mishaps.
93. Lower process temperature has to come from the lower melting temperature solder alloy.
94. A lower melting temperature solder alloy needs to resort to a quaternary system. Under the constraints of all practical factors, a quaternary system incurs higher raw material cost per unit weight.
95. Cost is part of the equation. The cost of ownership is the bottom line.
96. It is vitally important to recognize that quaternary system denoted herein is separate and distinct from a doped system.
97. For die attach and package levels, a practical system having a higher melting temperature above 275oC is yet to be established.
98. Solder joint reliability cannot outperform an alloy’s intrinsic properties and mechanical behavior (interactive creep and fatigue).
99. The development of the balanced performance was, and still is, a demanding task to deliver the performance and reliability equivalent to or better than 63Sn37Pb. It is a highly intricate use of metallurgy. Solder alloys and processes rather than SAC system need to be established to fit all applications that are currently (as of June, 2012) under RoHS exemptions.100. Ultimate reliability calls for the establishment of a lower process temperature to ensure the integrity of PCBAs that are complex in structure and makeup and required to perform under versatile and/or harsh environments.
Dr. Hwang will present two lectures on “Array Package Interconnection: Forward/Backward Compatibility and Reliability” and “Preventing Production Defects and Failures” at SMTA International Conference on October 15, 2012, in Orlando, Florida.Dr. Hwang, a pioneer and long-standing contributor to SMT manufacturing since its inception as well as to the lead-free development, has helped improve production yield and solved challenging reliability issues. Among her many awards and honors, she has been inducted into the WIT International Hall of Fame, elected to the National Academy of Engineering and named an R&D Stars to Watch. Having held senior executive positions with Lockheed Martin Corporation, Sherwin Williams Co., SCM Corporation and IEM Corporation, she is currently CEO of H-Technologies Group providing business, technology and manufacturing solutions. She is a member of the U.S. Commerce Department’s Export Council, and serves on the board of Fortune 500 NYSE companies and civic and university boards. She is the author of 300+ publications and several textbooks and an international speaker and author on trade, business, education and social issues. Contact her at (216) 577-3284; e-mail JennieHwang@aol.com.
More Columns from SMT Perspectives and Prospects
SMT Perspectives and Prospects: Warren Buffett’s Perpetual Wisdom, Part 2SMT Perspectives and Prospects: Warren Buffett’s Perpetual Wisdom, Part 1
SMT Perspectives and Prospects: Artificial Intelligence, Part 5: Brain, Mind, Intelligence
SMT Perspectives and Prospects: Artificial Intelligence, Part 4—Prompt Engineering
SMT Perspectives and Prospects: The AI Era, Part 3: LLMs, SLMs, and Foundation Models
SMT Perspectives and Prospects: A Dose of Wisdom
SMT Prospects and Perspectives: AI Opportunities, Challenges, and Possibilities, Part 1
SMT Perspectives and Prospects: Critical Materials—A Compelling Case, Part 3