-
- News
- Books
Featured Books
- pcb007 Magazine
Latest Issues
Current IssueInventing the Future with SEL
Two years after launching its state-of-the-art PCB facility, SEL shares lessons in vision, execution, and innovation, plus insights from industry icons and technology leaders shaping the future of PCB fabrication.
Sales: From Pitch to PO
From the first cold call to finally receiving that first purchase order, the July PCB007 Magazine breaks down some critical parts of the sales stack. To up your sales game, read on!
The Hole Truth: Via Integrity in an HDI World
From the drilled hole to registration across multiple sequential lamination cycles, to the quality of your copper plating, via reliability in an HDI world is becoming an ever-greater challenge. This month we look at “The Hole Truth,” from creating the “perfect” via to how you can assure via quality and reliability, the first time, every time.
- Articles
- Columns
- Links
- Media kit
||| MENU - pcb007 Magazine
Estimated reading time: 4 minutes
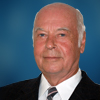
Contact Columnist Form
Karl's Tech Talk: Digital Imaging, Part A
Editor's Note: This article originally appeared in the October 2012 issue of The PCB Magazine.
The advantages of digital circuitization techniques have been described in detail by suppliers of equipment and photoresist. Since phototool generation and conditioning are omitted, there is the advantage of shorter lead time. Small lots can be customized at no extra cost (e.g., with added date and lot number information). There may be an advantage in fine-line imaging of surfaces with poor coplanarity because of the depth of focus of the laser beam. Perhaps the biggest advantage is the ability to scale (i.e., to change the dimension of each individual exposure for best fit to reference points on an underlying pattern of a multilayer structure). This is of particular value in soldermask LDI applications. Some processes excel in creating a metal pattern at great speed by laser ablation. Others can form recessed circuits with high resolution, excellent surface planarity, and improved anchoring of the circuit traces in the dielectric.
In this Part A, techniques that involve a mask, more specifically a dynamic mask will be covered. These are projection arrays that consist of many pixels, which can be addressed individually by electronic signals from a digital data base that turn the pixels on or off, allowing radiation from the light source to be projected onto the photoresist-covered board, or to be blocked from reaching the photoresist. A single projection exposure may create the entire circuitry (or soldermask) pattern, or the array of pixels may be stepped several times, with different pixel patterns, to complete the full image.
The most widely used dynamic mask is Texas Instruments’ Digital Micromirror Device™ (DMD), as shown in Figure 1.
Figure 1: Digital Micromirror Device (DMD). (Source: Texas Instruments.)
Figure 1 shows a picture of two mirrors on a chip--a small section of a DMD. These DMDs can be considered as microelectromechanical systems (MEMS) that consist of thousands of tiny mirrors per square inch (mirrors on a chip) that can pivot in one direction or another depending on the electric signal by which they are addressed, so that light reflected from the mirror is either directed to the resist or away from the resist. After the portion of the image represented by one such mirror configuration has been exposed, and a new mirror pattern is formed by new data, the board is stepped to the next image segment and exposed, a sequence that is repeated until the entire image has been completed. Earlier versions of DMD had a glass protective cover which made the DMDs not very suitable for UV light source imaging because of the UV light absorption of glass. Now available are DMDs with protective quartz covers that transmit a larger percentage of UV radiation. The following are commercial examples of digital imagers using DMDs:
- ORC DI-Impact (formerly by Pentax). The DI-Impact offers a minimum feature size of 15 µ L&S, position accuracy (repeatability) of +/- 7.5 µ, and a side-to-side registration of +/- 10 µ. The exposure time is about 35 seconds for 340 x 510 mm, depending on the photospeed of the resist. Use of 405 nm wavelength. High-pressure mercury lamp light source. Double-sided exposure, automated loading/unloading.
- Hitachi’s DE imagers DE-H, DE-S and DE-F series differentiate in their resolution capabilities. The imagers use a 405 nm diode laser, and make use of Texas Instrument’s DMD micromirror array model XGA. The DE-H has the highest resolution, capable of producing 10 µ lines and spaces. The overlapping pixels have addressability (center-to-center spacing) of 1.2 µ. The DE-S is capable of doing 20 µ L/S (2.6 µ addressability), and the DE-F does 40 µ L/S.
- Miva 2600X (MIVA Technologies GmbH, Germany). Direct imager, using Texas Instrument’s DMD micromirror array and LED light source. Highest resolution model: 2600X-16, 16,000 dpi, image time 125 sec (15mj/cm2; 18x24"). Also offered by Printprocess AG (Switzerland), as system Apollon-DI. Distributed by KuperTek in USA.
- Maskless Lithography uses DMDs and a mercury arc light source.
- Aiscent Technologies Inc. (Canada) is a newcomer in this field.
- Ball Semiconductor’s Direct Imager, using DMDs, was an early entry, but to the best of my knowledge, is not commercial at this time.
A different type of dynamic mask has been used by Dainippon Screen in its Mercurex direct imager that uses a high-pressure mercury lamp, and more recently in its UV LED Ledia 5 direct imager model. The projection system is called a spatial light modulator or a two-dimensional modulator. Basically, it is an array of liquid crystal polymer (LCP) cells (micro display). Each cell can be addressed by a digital signal. Depending whether the signal is on or off, the cell becomes either translucent or reflective. The LED light shines through the translucent cells of the display, projecting the image onto the resist.
Grating light valves (Figure 2) also fall into the category of dynamic masks. They have found applications in the printing industry and are now being considered for image transfer in electronics. They consist of parallel rows of flexible ribbons on silicon. Their shape can be modulated by electrical pulses so that they reflect or diffract light. The switching is extremely fast, which makes these devices interesting to digital imaging in electronics. However, I am not aware of an application in digital imaging of circuit boards yet.
Figure 2: Grating light valves.
Karl Dietz is president of Karl Dietz Consulting LLC, offering consulting services and tutorials in the field of circuit board and substrate fabrication technology. Dietz may be reached by E-mail at karldietz@earthlink.net, or phone (001) 919 870 6230.
More Columns from Karl's Tech Talk
Karl's Tech Talk: Digital Imaging UpdateKarl’s Tech Talk: Electronic Packaging Levels
Green Legislation and the Impact on Electronic Materials and Processes
Digital Imaging Revisited
Dry Film Photoresist Thickness Selection Criteria
Quick-Turn Circuit Board Shops
Optical Interconnects
Signal Loss