-
- News
- Books
Featured Books
- pcb007 Magazine
Latest Issues
Current IssueInventing the Future with SEL
Two years after launching its state-of-the-art PCB facility, SEL shares lessons in vision, execution, and innovation, plus insights from industry icons and technology leaders shaping the future of PCB fabrication.
Sales: From Pitch to PO
From the first cold call to finally receiving that first purchase order, the July PCB007 Magazine breaks down some critical parts of the sales stack. To up your sales game, read on!
The Hole Truth: Via Integrity in an HDI World
From the drilled hole to registration across multiple sequential lamination cycles, to the quality of your copper plating, via reliability in an HDI world is becoming an ever-greater challenge. This month we look at “The Hole Truth,” from creating the “perfect” via to how you can assure via quality and reliability, the first time, every time.
- Articles
- Columns
- Links
- Media kit
||| MENU - pcb007 Magazine
Estimated reading time: 5 minutes
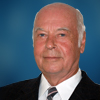
Contact Columnist Form
Karl's Tech Talk: Digital Imaging, Part B
Editor's Note: This article originally appeared in the November 2012 issue of The PCB Magazine.
The advantages of digital circuitization techniques have been described in detail by suppliers of equipment and photoresist. Since phototool generation and conditioning are omitted, there is the advantage of shorter lead time. Small lots can be customized at no extra cost (e.g., with added date and lot number information). There may be an advantage in fine-line imaging of surfaces with poor coplanarity because of the depth of focus of the laser beam. Perhaps the biggest advantage is the ability to “scale” (i.e., to change the dimension of each individual exposure for best fit to reference points on an underlying pattern of a multilayer structure). This is of particular value in soldermask LDI applications. Some processes excel in creating a metal pattern at great speed by laser ablation. Others can form recessed circuits with high resolution, excellent surface planarity, and improved anchoring of the circuit traces in the dielectric.
Digital Imaging, Part A covered techniques that involve a mask, more specifically a dynamic mask such as Texas Instruments’ Digital Micromirror Device™ (DMD), spatial light modulators (e.g., Dainippon Screen) and grating light valves.
In this column, we’ll look at inkjet applications. Inkjets work on the principle of forming and ejecting liquid droplets of uniform size in a continuous stream or on demand (Figures 1 and 2). In the case of demand-mode droplet formation, a volumetric change in the fluid initiates the droplet formation. This volumetric change can be induced by a voltage pulse to a piezoelectric material that is somehow coupled to the fluid or by focused acoustic energy. A thin-film resistor can also be substituted for the piezoelectric transducer. The fluid in contact with the resistor heats up, forming a vapor bubble (thermal inkjet).
In the case of continuous inkjetting, a continuous stream of droplets is created by inducing pressure oscillations in the jet by an electromechanical device. As the droplets exit the jet, an electrostatic field (charging field) charges the droplets, and a second high voltage field (deflection field), modulated by the digital image data, directs the droplets to the substrate or deflects them to a catcher reservoir.
Whichever inkjet technology is applied, signals from a digital database to either the droplet formation or the droplet trajectory path do the direct imaging.
Figure 1: Demand inkjet technology.
Figure 2: Continuous inkjet technology.
Several inkjetting patterning applications in electronics are emerging or are already fully commercial:
- Inkjetting “legend print” onto soldermask-covered circuit boards.
- Inkjetting resist pattern.
- Inkjetting a pattern of solubilizing agent (e.g., developer, stripper) onto a resist layer (e.g., diffusion patterning; John Felten, DuPont, patented).
- Inkjetting seed layer pattern.
- Inkjetting metal pattern (e.g., solder).
- Inkjetting metal patterns and dielectric layers to form multilayer circuits (e.g., Epson).
- Inkjetting passive components.
Inkjet printers have been technically perfected to achieve high-reliability, high-resolution, and high-speed at low cost. The technology appears suitable for a variety of applications in PWB fabrication and assembly. One of the first applications that comes to mind is the use of inkjets for legend printing. So it is not surprising to see several companies active in this arena. The great advantage of inkjet technology applications in electronics has to do with the fact that digital data such as CAD files directly drive the image formation. Inkjets employed in legend printing can form drops as small as 5-7 picoliters (pl) yielding adequate resolution for legend print.
The traditional legend print by screen-printing is a costly, multistep process with a long lead-time. By contrast to screen-printing, inkjet legend printing is remarkably simple, flexible, and has practically no lead-time. Changes from one image to the next for small lot sizes present no problem. This technology is ideally suited for quick-turn and prototype shops, and it is the legend-print equivalent to laser direct imaging (LDI) of the circuitry. The following list shows suppliers of commercial legend print inkjet systems:
- SD-1000 (ORC, formerly Pentax, Japan, Newprint (Orbotech, formerly New System, Italy), DPL (Jetmask Ltd., UK), Camtek (formerly Printar): LGP 809 legend printer (Israel) .
- EIE (Switzerland): CP400 Circuit Printer for legend print (inkjet head from MARKEM, nozzles from Spectra for hot inkjetting). Mivatec (Germany) legend inkjet built on Mivatec’s MIVA 28xx Series plotter platform architecture.
- Yokogawa (Japan) inkjet legend printer. MicroCraft (Japan): MicroJet 6050 DLP (direct legend print), linked to electrical tester.
- MARKEM Corporation provides Model 4000 inkjet print head to several printer system suppliers.
Suppliers of inkjet systems for jetting resist or soldermask patterns:
- Schmid (Germany): DirectMask DoD 8000. 80 micron lines and spaces have been achieved. The inkjet printhead (Spectra) dispenses droplets on demand. A UV drier is mounted directly on the printhead to render the resist tack-free within seconds and avoid bleeding of the resist droplets. The platform supporting the board is a laser drill architecture. The resist is from Shipley.
- Camtek (formerly Printar): soldermask (developmental?).
- Jetmask (Fuji, Patterning Technologies): etch resist.
- CircuitJet™ (MacDermid & New System): etch resist.
- Avecia Electronic Materials (UK): JeTrack™ soldermask and etchmask inks for inkjet applications (in cooperation with printer system suppliers).
- Newprint (Orbotech, formerly New System, Italy): soldermask and etchmask inkjetting.
- JetCompany BV (JetCo) (Germany): distributes inkjet imagers for soldermask and etchmask inkjetting, developed by a consortium (Patterning Technologies Ltd (PTL), KLG Machinen GmbH (KLG), Adeon Technologies BV).
Inkjetting a relatively thick layer may require multiple inkjet passes to build up the desired thickness, and may therefore be a low-throughput process. Patterning of a previously applied, non-patterned thick coating with an inkjet would be the better approach in this situation. A technology called diffusion patterning serves this purpose. The thick coating can be patterned by selectively applying a chemical that renders the resist either soluble or insoluble by diffusing into the coating and changing its chemical nature. An inkjet printer can be used to spray droplets of base (high pH chemical) onto an aqueous processable resist, creating a diffusion pattern of soluble resist, which can then be rinsed off. There don’t seem to be any commercial applications of this concept yet.
Figure 3: Diffusion patterning of resist.
MicroFab Technologies, Inc. has pioneered diverse end-use applications for inkjets, including electronics, biomedical and micro-optics. In the electronic field, MicroFab has demonstrated inkjet applications for dielectrics, adhesives, organometallic inks for conductors, and solder mask. The company has done work in the area of direct-writing of embedded passives. Another development effort is aimed at depositing molten solder in a pattern to form solder bump arrays. Solder jet technology is based on piezoelectric demand-mode inkjet printing of molten solder droplets, 25-125 mm in diameter at the rate of 400 per second.
Finally, another unique inkjet application was demonstrated by Epson. An inkjet printer (machine head, piezoelectric, not thermal) jets insulator ink and conductor ink (silver micro-particles with organic coating). A metal wiring pattern is inkjetted onto an insulating layer and baked at 150-200°C. Metal posts for Z-axis interconnects and insulating layer are inkjetted. A 20x20 mm, 20-layer board was built by this process.
Karl Dietz is president of Karl Dietz Consulting LLC. He is offering consulting services and tutorials in the field of circuit board and substrate fabrication technology. Dietz may be reached by e-mail at karldietz@earthlink.net or phone (001)- 919 870 6230.
More Columns from Karl's Tech Talk
Karl's Tech Talk: Digital Imaging UpdateKarl’s Tech Talk: Electronic Packaging Levels
Green Legislation and the Impact on Electronic Materials and Processes
Digital Imaging Revisited
Dry Film Photoresist Thickness Selection Criteria
Quick-Turn Circuit Board Shops
Optical Interconnects
Signal Loss