-
- News
- Books
Featured Books
- pcb007 Magazine
Latest Issues
Current IssueInventing the Future with SEL
Two years after launching its state-of-the-art PCB facility, SEL shares lessons in vision, execution, and innovation, plus insights from industry icons and technology leaders shaping the future of PCB fabrication.
Sales: From Pitch to PO
From the first cold call to finally receiving that first purchase order, the July PCB007 Magazine breaks down some critical parts of the sales stack. To up your sales game, read on!
The Hole Truth: Via Integrity in an HDI World
From the drilled hole to registration across multiple sequential lamination cycles, to the quality of your copper plating, via reliability in an HDI world is becoming an ever-greater challenge. This month we look at “The Hole Truth,” from creating the “perfect” via to how you can assure via quality and reliability, the first time, every time.
- Articles
- Columns
- Links
- Media kit
||| MENU - pcb007 Magazine
Estimated reading time: 1 minute
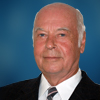
Contact Columnist Form
Solvent Use & Transition to Aqueous Processing in PCB Fabrication & Assembly
Looking back over the last 50 years of electronic manufacturing one will notice that solvents, in particular halogenated hydrocarbons, were widely used in a variety of process steps. They were used as developers and strippers in photoresist processing, to remove plater tape residues from board surfaces after nickel/gold plating, and to clean fluxes after soldering components in assembly. Due to health and environmental concerns, as well as cost issues, these solvents were phased out and replaced by aqueous chemistries or water-miscible solvents that present a lower health risk. To enable these transitions, new photoresists and new fluxes had to be developed, as well as plater tapes that release cleaner from the board surface without compromising adhesion during plating.
Imaging of Circuit Patterns
Screen printing of an etch resist and/or plating resist pattern, followed by etching (or plating and etching) was quite common in the ‘50s and ‘60s. Today, this process is only used for simple, single-sided boards. The screen is coated with a photosensitive emulsion, dried and exposed through a phototool. Unexposed emulsion is washed off with water. The emulsion stencil pattern and residual resist ink were typically stripped with trichloroethylene or a toluene based stripper for re-use of the screen. In today’s remaining applications other solvents are likely to be used.
Editor's Note: This article originally appeared in the April 2013 issue of The PCB Magazine.
More Columns from Karl's Tech Talk
Karl's Tech Talk: Digital Imaging UpdateKarl’s Tech Talk: Electronic Packaging Levels
Green Legislation and the Impact on Electronic Materials and Processes
Digital Imaging Revisited
Dry Film Photoresist Thickness Selection Criteria
Quick-Turn Circuit Board Shops
Optical Interconnects
Signal Loss