-
- News
- Books
Featured Books
- pcb007 Magazine
Latest Issues
Current IssueInventing the Future with SEL
Two years after launching its state-of-the-art PCB facility, SEL shares lessons in vision, execution, and innovation, plus insights from industry icons and technology leaders shaping the future of PCB fabrication.
Sales: From Pitch to PO
From the first cold call to finally receiving that first purchase order, the July PCB007 Magazine breaks down some critical parts of the sales stack. To up your sales game, read on!
The Hole Truth: Via Integrity in an HDI World
From the drilled hole to registration across multiple sequential lamination cycles, to the quality of your copper plating, via reliability in an HDI world is becoming an ever-greater challenge. This month we look at “The Hole Truth,” from creating the “perfect” via to how you can assure via quality and reliability, the first time, every time.
- Articles
- Columns
- Links
- Media kit
||| MENU - pcb007 Magazine
Estimated reading time: 1 minute
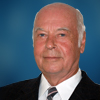
Contact Columnist Form
Karl's Tech Talk: Miniaturization and Reliability
Miniaturization of electronic devices has been a trend over decades and is continuing into the foreseeable future. How this trend affects the reliability of these devices is an important question. Some processes, when applied to ever-smaller dimensions, reach a point where they yield less reliable structures, and changes in materials and processing are necessary to maintain reliability. On the other hand, other novel technologies that enable smaller structures are inherently more reliable. The following technologies are examples of miniaturization-reliability relationships.
Wafer Bumping with Plated Copper Pillars
Wafer bumping, the formation of solderable, raised, conductive features that allow the connection of flip chips to a package, typically involves the use of solder, either applied by a stencil, or plated, or by the mechanical positioning of a preformed solder ball. Height and width of these bumps are about the same after reflow (i.e., the bumps become spherical after reflow). This means that minimum spacing requirements between solder bumps and the “stand-off height” are linked, and one cannot reduce one without reducing the other.
The use of plated copper pillars as bumps “decouples” the stand-off height from the minimum spacing between bumps because there is no reflow and the aspect ratio of the pillars remains as plated (Figures 1 and 2). The copper pillars are typically capped with a solderable surface such as plated tin. The higher stand-off height at smaller bump pitches can facilitate more reliable underfill coverage, and the better thermal (and electrical) conductivity of copper compared to solder may contribute to better thermal management; both factors contribute to interconnect reliability. However, the lower ductility of copper compared to solder is a potential detriment.
Editor's Note: This article originally appeared in the August 2013 issue of The PCB Magazine.
More Columns from Karl's Tech Talk
Karl's Tech Talk: Digital Imaging UpdateKarl’s Tech Talk: Electronic Packaging Levels
Green Legislation and the Impact on Electronic Materials and Processes
Digital Imaging Revisited
Dry Film Photoresist Thickness Selection Criteria
Quick-Turn Circuit Board Shops
Optical Interconnects
Signal Loss