-
- News
- Books
Featured Books
- pcb007 Magazine
Latest Issues
Current IssueInventing the Future with SEL
Two years after launching its state-of-the-art PCB facility, SEL shares lessons in vision, execution, and innovation, plus insights from industry icons and technology leaders shaping the future of PCB fabrication.
Sales: From Pitch to PO
From the first cold call to finally receiving that first purchase order, the July PCB007 Magazine breaks down some critical parts of the sales stack. To up your sales game, read on!
The Hole Truth: Via Integrity in an HDI World
From the drilled hole to registration across multiple sequential lamination cycles, to the quality of your copper plating, via reliability in an HDI world is becoming an ever-greater challenge. This month we look at “The Hole Truth,” from creating the “perfect” via to how you can assure via quality and reliability, the first time, every time.
- Articles
- Columns
- Links
- Media kit
||| MENU - pcb007 Magazine
Estimated reading time: 2 minutes
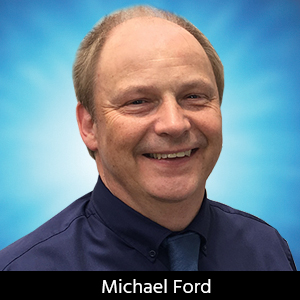
Contact Columnist Form
The Essential Pioneer's Survival Guide: Why Are ERP and MES So Limited in Electronics?
Enterprise resource planning (ERP) and manufacturing execution systems (MES) are great tools that have brought manufacturing progressively forward, meeting customer and market needs, empowering global operations, and bringing success. Although the price for these tools can cause sticker shock, especially considering the IT muscle needed for their continuous operation, the critical measure of return on investment is compelling--except in the case of electronics manufacturing.
An impenetrable chaos seems to exist within electronics manufacturing that neither ERP nor MES can crack. For sure, the core functionality of these systems applies equally well for electronics, yet somehow, key stubborn issues remain. Many of these poor practices were originally introduced as countermeasures to ensure a smoother production flow. The core issues then become more elusive to solve as operational momentum builds over time. However, most issues can be traced back to the fundamental lack of control of materials on the shop-floor, specifically, the lack of material inventory, integrity, and accuracy.
The effect of inventory inaccuracy is unexpected material starvation at key processes and inability to complete planned work-orders. Materials that were expected to be available, as reported by ERP, are not. Management, motivated simply by the need to ensure deliveries are met, decides to increase the overall materials stocks to prevent the starvation, increasing the warehouse and shop-floor material stock-holding. But this action serves only to delay the inevitable result of the continued accumulation of inventory error.
Then the only way to consolidate the mismatch between the ERP view of available materials and the actual physical materials is to perform a physical stock count. This is not a simple task because unmanaged materials on the shop-floor need to be counted as well as those in the warehouse. Several kits of materials for many work-orders for each line usually are on the shop floor, as well as partly used materials by the machines and on the machines, including live materials in use and materials not in use in a common family setup. Also, partly used materials are on trolleys reserved for production of other product families, along with partly used materials that are no longer in use, which have not been returned to the warehouse. Partly used materials are often left on the shop floor as an additional buffer-stock in case unexpected materials shortages happen. These are almost always very poorly managed, with many materials lost from the operation.Read the full column here.Editor's Note: This column originally appeared in the February 2014 issue of SMT Magazine.
More Columns from The Essential Pioneer's Survival Guide
If It's My Data, I Can Do What I Want, Right?The Essential Pioneer's Survival Guide: One Size Fits All?
Smart for Smart’s Sake, Part 3: Unification & Traceability
Smart for Smart's Sake, Part 2: Material Management
The 'New Face' of Automotive Traceability
Industry 4.0: Who Benefits?
To Be Lean is to Be Human
Stop the SMT Conspiracy, Part 2: Abduction