-
- News
- Books
Featured Books
- pcb007 Magazine
Latest Issues
Current IssueSales: From Pitch to PO
From the first cold call to finally receiving that first purchase order, the July PCB007 Magazine breaks down some critical parts of the sales stack. To up your sales game, read on!
The Hole Truth: Via Integrity in an HDI World
From the drilled hole to registration across multiple sequential lamination cycles, to the quality of your copper plating, via reliability in an HDI world is becoming an ever-greater challenge. This month we look at “The Hole Truth,” from creating the “perfect” via to how you can assure via quality and reliability, the first time, every time.
In Pursuit of Perfection: Defect Reduction
For bare PCB board fabrication, defect reduction is a critical aspect of a company's bottom line profitability. In this issue, we examine how imaging, etching, and plating processes can provide information and insight into reducing defects and increasing yields.
- Articles
- Columns
- Links
- Media kit
||| MENU - pcb007 Magazine
Estimated reading time: 1 minute
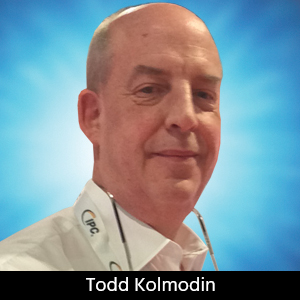
Challenges of Electrical Test
Challenges to electrical test are many, but a few come to mind as the most challenging. What do you think they are? Here’s what I think:
3. Pitch and density
2. Volume
And the #1 most challenging attribute to electrical test: soldermask! In our arena today, we can solve pitch and density with flying probe machines, and volume with our grid testers, but the catalyst that is in the mix is that pesky soldermask! So why do I bring up that necessary process as a problem for electrical test?
Electrical test is an absolute science test based on mathematics and absolutes. Frontend systems rasterize the given data to absolutes. If the IPC, Gerber, and ODB++ data show the alignment of layers to the mask, it is an absolute measurement. There are no easements for registration. The test points are assigned to the product based on the absolute clearance allowed in the “Golden” data supplied in the CAD Reference.
But there is a disconnect.
To be blatantly accurate, it never happens. The phenomenon of via cap, via fill and zeroheight via fill all come in to play to change the whole game regardless of what the OEM designed. Tolerances are never considered.
Read the full column here.Editor's Note: This column originally appeared in the January 2015 issue of The PCB Magazine.
More Columns from Testing Todd
Testing Todd: Why 4-wire Kelvin?Testing Todd: Why TDR?
Testing Todd: Positivity Boosts Employee Morale
Testing Todd: Preparing Employees for the Long Haul
Testing Todd: Where Can We Improve?
Testing Todd: Turning Into the Wind
Testing Todd: Coming Back to Life—Design Recovery
Testing Todd: Decision Time—Invest or Delegate?