-
- News
- Books
Featured Books
- design007 Magazine
Latest Issues
Current IssueShowing Some Constraint
A strong design constraint strategy carefully balances a wide range of electrical and manufacturing trade-offs. This month, we explore the key requirements, common challenges, and best practices behind building an effective constraint strategy.
All About That Route
Most designers favor manual routing, but today's interactive autorouters may be changing designers' minds by allowing users more direct control. In this issue, our expert contributors discuss a variety of manual and autorouting strategies.
Creating the Ideal Data Package
Why is it so difficult to create the ideal data package? Many of these simple errors can be alleviated by paying attention to detail—and knowing what issues to look out for. So, this month, our experts weigh in on the best practices for creating the ideal design data package for your design.
- Articles
- Columns
- Links
- Media kit
||| MENU - design007 Magazine
Multek CTO Excited About the Challenges of the Fast-Moving Wearables Market
March 26, 2015 | Barry Matties, I-Connect007Estimated reading time: 9 minutes
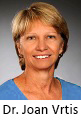
At IPC APEX EXPO 2015, held in San Diego, Calif. I had the opportunity to sit with Dr. Joan Vrtis to discuss the rapidly evolving wearables market, especially for medical, and the myriad questions that must be addressed. We also touched on Multek’s contribution to the wearables industry and what it sees as the main challenges to putting their circuits into various applications.
Barry Matties: Good morning, Joan. Why don't you start by telling me a little bit about what's that like being chief technology officer at Multek. I understand it is a recent position. Congratulations!
Dr. Joan Vrtis: Thank you very much. Multek is an industry leader in printed circuit technology, and the wholly owned subsidiary of Flextronics. As the chief technology officer, I’m looking at the wearable technology and how we can put our printed circuits into applications. So for Multek, it's really the solutions of what we can offer on the printed circuit side, whether it's a rigid circuit, a flex circuit, a rigid-flex and even things that can stretch and bend. We must be prepared for the broad markets we serve, specifically in the wearables. That's currently where I've been putting most of my effort.
Matties: Wearables is a fast-moving market, isn't it?
Vrtis: Yes, it is.
Matties: What is the state of the market as you see it, currently?
Vrtis: One of the things we've seen just recently is the expansion of the number of ideas as to what should be a wearable. How do we help translate these ideas to product and how do we market them? Some trends regarding wearables are in close proximity to the body, on the body and in the body. For example, the wristband type of technologies, such as activity band, watch, smart watch. Then there are the wearables on skin, which includes patch-like technologies used for authentication. Now, wearables ideas are growing, as inventors and companies look at putting electronics into a fabric. Can the button be used as the connection for the continuity of the circuit? Can the zipper be part of the solution to turn on and off the electronics if placed in a safety jacket? How do we integrate the components that go with that? We have to consider power, wireless, etc. And if you want something that's going to move—a gyroscope, or accelerometer—how do we put all of these components in and how do we select those components?
On the printed circuit side, historically we're used to circuit boards being like 2D structures, thus they would be flat, and then we would place the components on and go. But now we also have to take into account that they're going to bend and move. When it starts getting into the apparel side, do you make that cloth fabric your printed circuit substrate? Those are the things that people are coming to us with and saying, “Hey, can you guys do apparel?” But what does that mean? Are you going to wash it? There are a lot of questions to ask.
Matties: With the power technology in apparel and wearables, certainly washing must be a big issue.
Vrtis: Yes, it is a big issue, as is drying.
Matties: What's the craziest thing that someone has approached you with?
Vrtis: Let's see. I've had some very interesting requests for solutions with the printed circuit, but the craziest probably doesn’t need to be recorded here.
Matties: That’s okay; we can leave it to the imagination.
Vrtis: The important thing is that they needed all of the same components I have been talking about. They needed power and they needed some way to have this wireless to connect.
Matties: Let's talk about the market a little bit. What's the size of the market right now, the way you are seeing it?
Vrtis: Wow, it's in the billions! I’ve read eight billion is predicted in the next couple of years.
Matties: Where was that just a few years back?
Page 1 of 2
Suggested Items
Happy’s Tech Talk #40: Factors in PTH Reliability—Hole Voids
07/09/2025 | Happy Holden -- Column: Happy’s Tech TalkWhen we consider via reliability, the major contributing factors are typically processing deviations. These can be subtle and not always visible. One particularly insightful column was by Mike Carano, “Causes of Plating Voids, Pre-electroless Copper,” where he outlined some of the possible causes of hole defects for both plated through-hole (PTH) and blind vias.
Trouble in Your Tank: Can You Drill the Perfect Hole?
07/07/2025 | Michael Carano -- Column: Trouble in Your TankIn the movie “Friday Night Lights,” the head football coach (played by Billy Bob Thornton) addresses his high school football team on a hot day in August in West Texas. He asks his players one question: “Can you be perfect?” That is an interesting question, in football and the printed circuit board fabrication world, where being perfect is somewhat elusive. When it comes to mechanical drilling and via formation, can you drill the perfect hole time after time?
The Evolution of Picosecond Laser Drilling
06/19/2025 | Marcy LaRont, PCB007 MagazineIs it hard to imagine a single laser pulse reduced not only from nanoseconds to picoseconds in its pulse duration, but even to femtoseconds? Well, buckle up because it seems we are there. In this interview, Dr. Stefan Rung, technical director of laser machines at Schmoll Maschinen GmbH, traces the technology trajectory of the laser drill from the CO2 laser to cutting-edge picosecond and hybrid laser drilling systems, highlighting the benefits and limitations of each method, and demonstrating how laser innovations are shaping the future of PCB fabrication.
Day 2: More Cutting-edge Insights at the EIPC Summer Conference
06/18/2025 | Pete Starkey, I-Connect007The European Institute for the PCB Community (EIPC) summer conference took place this year in Edinburgh, Scotland, June 3-4. This is the third of three articles on the conference. The other two cover Day 1’s sessions and the opening keynote speech. Below is a recap of the second day’s sessions.
Day 1: Cutting Edge Insights at the EIPC Summer Conference
06/17/2025 | Pete Starkey, I-Connect007The European Institute for the PCB Community (EIPC) Summer Conference took place this year in Edinburgh, Scotland, June 3-4. This is the second of three articles on the conference. The other two cover the keynote speeches and Day 2 of the technical conference. Below is a recap of the first day’s sessions.