-
-
News
News Highlights
- Books
Featured Books
- design007 Magazine
Latest Issues
Current IssueAll About That Route
Most designers favor manual routing, but today's interactive autorouters may be changing designers' minds by allowing users more direct control. In this issue, our expert contributors discuss a variety of manual and autorouting strategies.
Creating the Ideal Data Package
Why is it so difficult to create the ideal data package? Many of these simple errors can be alleviated by paying attention to detail—and knowing what issues to look out for. So, this month, our experts weigh in on the best practices for creating the ideal design data package for your design.
Designing Through the Noise
Our experts discuss the constantly evolving world of RF design, including the many tradeoffs, material considerations, and design tips and techniques that designers and design engineers need to know to succeed in this high-frequency realm.
- Articles
- Columns
- Links
- Media kit
||| MENU - design007 Magazine
The Composite Properties of Rigid vs. Multilayer PCBs
June 17, 2015 | Chet GuilesEstimated reading time: 2 minutes
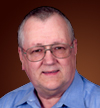
Abstract
Most materials systems used in PWBs (aka PCBs) are composites of resins, fabric substrates and metal cladding. Each of these components has its own unique electrical and mechanical properties that contribute to the final characteristics of the finished laminates, prepregs and fabricated multilayer boards (MLBs). In most cases variables such as glass style and resin content have offsetting impacts on physical vs. electrical properties.
Data sheets often provide data in standard IPC formats, which may look at properties in rigid laminates (nominal 0.062” made using heavyweight glass at 32–40% resin content) rather than thin lams and prepregs used for multilayer PWBs (which more typically average 55% resin content or more). To further complicate the situation, some product lines are manufactured with consistent resin content for all product thicknesses, thus maintaining the dielectric properties while letting the mechanical properties be dictated by the constructions and resin content.
An understanding of what such variations in properties mean and how they relate to what the users will actually encounter is essential to design, manufacturability, assembly and end-use viability. In this presentation we will look specifically at the effect of glass style and resin content on dielectric constant and CTE and discuss how even at the product design level it is important for design engineers to take these into consideration.
Conclusions
In most cases, no single value of dielectric constant or in-plane CTE (representative laminate properties that are impacted by resin content variation—obviously there are others as well, but for purposes of keeping this work manageable, we will focus on these two) will hold for all thicknesses of laminate or build-ups for MLBs. In those cases where either or both are critical, it is necessary to control resin content in both laminate and prepreg to ensure that the finished properties fall within the desired and expected ranges.
In some cases, such as with 85N polyimide and 92ML thermally conductive epoxy products, the specific values of Dk and CTE are less critical than other things such as processibility and design flexibility (as for 85N) or thermal conductivity (for 92ML) and so resin contents are allowed to vary so as to meet these needs.
In other cases either CTE (as in 85NT) or dielectric constant (as for Multiclad HF or 25N/FR) are critical needs, and in those cases the resin contents must be held to controlled limits so that the desired properties are consistently held for most or all of the laminate configurations.
To read this article, which originally appeared in the May 2016 issue of The PCB Design Magazine, click here.
Suggested Items
DownStream Acquisition Fits Siemens’ ‘Left-Shift’ Model
06/26/2025 | Andy Shaughnessy, I-Connect007I recently spoke to DownStream Technologies founder Joe Clark about the company’s acquisition by Siemens. We were later joined by A.J. Incorvaia, Siemens’ senior VP of electronic board systems. Joe discussed how he, Rick Almeida, and Ken Tepper launched the company in the months after 9/11 and how the acquisition came about. A.J. provides some background on the acquisition and explains why the companies’ tools are complementary.
Elementary Mr. Watson: Retro Routers vs. Modern Boards—The Silent Struggle on Your Screen
06/26/2025 | John Watson -- Column: Elementary, Mr. WatsonThere's a story about a young woman preparing a holiday ham. Before putting it in the pan, she cuts off the ends. When asked why, she shrugs and says, "That's how my mom always did it." She asks her mother, who gives the same answer. Eventually, the question reaches Grandma, who laughs and says, "Oh, I only cut the ends off because my pan was too small." This story is a powerful analogy for how many PCB designers approach routing today.
Siemens Turbocharges Semiconductor and PCB Design Portfolio with Generative and Agentic AI
06/24/2025 | SiemensAt the 2025 Design Automation Conference, Siemens Digital Industries Software today unveiled its AI-enhanced toolset for the EDA design flow.
Cadence AI Autorouter May Transform the Landscape
06/19/2025 | Andy Shaughnessy, Design007 MagazinePatrick Davis, product management director with Cadence Design Systems, discusses advancements in autorouting technology, including AI. He emphasizes a holistic approach that enhances placement and power distribution before routing. He points out that younger engineers seem more likely to embrace autorouting, while the veteran designers are still wary of giving up too much control. Will AI help autorouters finally gain industry-wide acceptance?
Beyond Design: The Metamorphosis of the PCB Router
06/18/2025 | Barry Olney -- Column: Beyond DesignThe traditional PCB design process is often time-consuming and labor-intensive. Routing a complex PCB layout can consume up to 30% of a designer’s time, and addressing this issue is not straightforward. We have all encountered this scenario: You spend hours setting the constraints and finally hit the Go button, only to be surprised by the lack of visual appeal and the obvious flaws in the result.