-
-
News
News Highlights
- Books
Featured Books
- design007 Magazine
Latest Issues
Current IssueAll About That Route
Most designers favor manual routing, but today's interactive autorouters may be changing designers' minds by allowing users more direct control. In this issue, our expert contributors discuss a variety of manual and autorouting strategies.
Creating the Ideal Data Package
Why is it so difficult to create the ideal data package? Many of these simple errors can be alleviated by paying attention to detail—and knowing what issues to look out for. So, this month, our experts weigh in on the best practices for creating the ideal design data package for your design.
Designing Through the Noise
Our experts discuss the constantly evolving world of RF design, including the many tradeoffs, material considerations, and design tips and techniques that designers and design engineers need to know to succeed in this high-frequency realm.
- Articles
- Columns
- Links
- Media kit
||| MENU - design007 Magazine
Design and Manufacture of High-Voltage Electronics
July 27, 2015 | Pete Starkey, I-Connect007Estimated reading time: 4 minutes
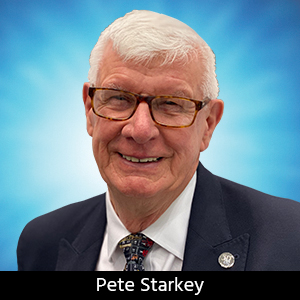
“With footprint becoming an ever-increasing issue, demands on high voltage electronics design and manufacture are becoming ever more difficult to manage. Decreasing size demands and HV requirements for creepage clearances and separation are at odds with each other, meaning that modern methods need to be refined in order to maintain performance and push the boundaries of current technical requirements.”
This SMART Group webinar, presented by Ian Lake, director of engineering at Applied Kilovolts Ltd, and moderated by Bob Willis, explored the current technical barriers faced in high-voltage electronics design and manufacturing processes. Although he made it clear that within the timeframe of a webinar session he could only scratch the surface of the topic, Lake gave a valuable insight into basic concepts and drivers and set a perspective on current state of the art and future trends.
Against a background of expectation that electronic designs would continue to get smaller, the rules of physics remained, and high voltages would continue to require creepage, clearance and insulation. The concerns were the effects of high-voltage breakdown, whether immediate or latent, on reliability and performance, and the effects of partial discharge and corona on the degradation of insulation. A set of rules was needed to facilitate the creation of designs which combined manufacturability and reliability, whilst managing creepage, clearance and insulation stress, backed up by standards such as EN/UL61010, EN/UL60601 and IPC-222, and best practice in manufacturing.
Defining “creepage” as the shortest path between conductors along the surface and “clearance” as the shortest path through air, Lake demonstrated how values depended on transient voltages and the comparative tracking index of the material, and gave numerical examples from EN61010.
Considering the electrical breakdown of insulating materials, which occurred when their dielectric strength was exceeded, he listed dielectric strengths of common materials and resins. A typical value for FR-4 rigid laminate was 20kV/mm, for Kapton flexible laminate 22kV/mm and for PTFE 50-170kV/mm. The dielectric strength of air was approximately 3.4kV/mm, but this varied with pressure according to Paschen’s Law. Actual breakdown voltage was heavily dependent on test conditions and thickness of sample; remarkably, thin films had much higher dielectric strengths although Lake admitted that he did not have the physics to explain why. It was clear that choice of materials for PCB substrates was critical.
The distribution of voltage between the electrodes depended on their geometry, and Lake’s illustrations with contour maps of equipotential clearly demonstrated the difference between smooth and pointed conductors. Finite element analysis software was available, which enabled analysis of voltage distribution and stresses in insulation systems with different dielectric constants. Plotting electrical field strength in kV/mm gave useful information when comparing electrodes of different geometries, and could indicate areas susceptible to corona and subsequent breakdown, driven by maximum field strength. Field strengths greater than 3kV/mm could cause local ionisation of air, with corrosive by-products that contributed to breakdown of materials.
When designing printed circuit boards for high-voltage applications, pad shape was critically important if field strength was to be kept to a minimum, and smoothly rounded pads were preferred. Conformal coating added an insulating layer, reduced peak field strength, protected conductors from contaminants and moisture, and reduced corona. And as previously stated, thin films of conformal coat could have remarkably high dielectric strength.
As high-voltage designs became more compact, with greater functionality packed into smaller spaces, additional precautions were necessary to minimise electrical stress and avoid breakdown. As well as rounded pads and shaped electrodes, conformal coating materials needed to be carefully chosen, and surface preparation and adhesion became critical factors. In particular, it was essential that conformal coatings were void-free, since partial discharge could occur in voids in areas of high field strength, producing ozone which could damage insulation and cause progressive breakdown.
From the point of view of assembly, component positioning was obviously an important consideration, with solder joints as smooth as possible. Cleanliness was crucial for reliability, since contaminants could have a lower breakdown voltage than the PCB material and could absorb moisture. So it was essential not only to clean assemblies meticulously but also to verify cleanliness by ionic contamination and residue testing. As with conformal coating, any potting or encapsulating material should be applied only to clean, dry surfaces and be void-free, using de-gassed material and processing under vacuum if necessary. A wide range of potting compounds was available, typically based on epoxy resins, silicone rubbers or polyurethanes, and many factors influenced the choice of material for a particular job, including ease of processing, mechanical and electrical strength, thermal conductivity and temperature rating. A good understanding of processing parameters and the use of appropriate mixing and dispensing equipment were obvious prerequisites.
Lake summarised by emphasising that although they were “just another area of electronics,” high-voltage products needed specialist design rules and a clear understanding of key process drivers. Whilst some specialist techniques were involved, successful manufacturing depended on carefully validated processes with effective control and monitoring.
About the SMART Group
The SMART Group Aims to Promote the Advancement of the Electronics Manufacturing Industry through the Education, Training and Notification of its Members in Surface Mount and Related Assembly Technologies, and by the Promotion of a Community of Electronics Manufacturing Professionals.
This is to be Accomplished by Active Encouragement of Member Inter-activity, through Meetings, Seminars, Conferences and Publication of Technical Information. The SMART Group Invites and Requires the Active Participation of all its Members in these Aims.
Suggested Items
Hands-On Demos Now Available for Apollo Seiko’s EF and AF Selective Soldering Lines
06/30/2025 | Apollo SeikoApollo Seiko, a leading innovator in soldering technology, is excited to spotlight its expanded lineup of EF and AF Series Selective Soldering Systems, now available for live demonstrations in its newly dedicated demo room.
Indium Corporation Expert to Present on Automotive and Industrial Solder Bonding Solutions at Global Electronics Association Workshop
06/26/2025 | IndiumIndium Corporation Principal Engineer, Advanced Materials, Andy Mackie, Ph.D., MSc, will deliver a technical presentation on innovative solder bonding solutions for automotive and industrial applications at the Global Electronics A
Fresh PCB Concepts: Assembly Challenges with Micro Components and Standard Solder Mask Practices
06/26/2025 | Team NCAB -- Column: Fresh PCB ConceptsMicro components have redefined what is possible in PCB design. With package sizes like 01005 and 0201 becoming more common in high-density layouts, designers are now expected to pack more performance into smaller spaces than ever before. While these advancements support miniaturization and functionality, they introduce new assembly challenges, particularly with traditional solder mask and legend application processes.
Knocking Down the Bone Pile: Tin Whisker Mitigation in Aerospace Applications, Part 3
06/25/2025 | Nash Bell -- Column: Knocking Down the Bone PileTin whiskers are slender, hair-like metallic growths that can develop on the surface of tin-plated electronic components. Typically measuring a few micrometers in diameter and growing several millimeters in length, they form through an electrochemical process influenced by environmental factors such as temperature variations, mechanical or compressive stress, and the aging of solder alloys.
SolderKing’s Successful Approach to Modern Soldering Needs
06/18/2025 | Nolan Johnson, I-Connect007Chris Ward, co-founder of the family-owned SolderKing, discusses his company's rapid growth and recent recognition with the King’s Award for Enterprise. Chris shares how SolderKing has achieved these award-winning levels of service in such a short timeframe. Their secret? Being flexible in a changing market, technical prowess, and strong customer support.