-
- News
- Books
Featured Books
- smt007 Magazine
Latest Issues
Current IssueIntelligent Test and Inspection
Are you ready to explore the cutting-edge advancements shaping the electronics manufacturing industry? The May 2025 issue of SMT007 Magazine is packed with insights, innovations, and expert perspectives that you won’t want to miss.
Do You Have X-ray Vision?
Has X-ray’s time finally come in electronics manufacturing? Join us in this issue of SMT007 Magazine, where we answer this question and others to bring more efficiency to your bottom line.
IPC APEX EXPO 2025: A Preview
It’s that time again. If you’re going to Anaheim for IPC APEX EXPO 2025, we’ll see you there. In the meantime, consider this issue of SMT007 Magazine to be your golden ticket to planning the show.
- Articles
- Columns
Search Console
- Links
- Media kit
||| MENU - smt007 Magazine
Mechatronics Innovations and Applications
August 6, 2015 | Stephen Las Marias, I-Connect007Estimated reading time: 7 minutes
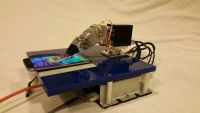
Edward Neff, President of SMAC Moving Coil Actuators, discusses with I-Connect007's Stephen Las Marias some of the mechatronics innovations happening in his company, and how these developments are being applied in different industries including electronics assembly.
Stephen Las Marias: First, please talk about the company. What does SMAC do, and what are your biggest markets?
Edward Neff: SMAC was set up to develop advanced and unique electric actuators aimed at replacing old technology devices such as pneumatic cylinders, ball screw actuators, and moving magnet type linear motors. Our main markets are electronic assembly, automotive manufacturing, packaging, and now biotech, consumer electronics, and semiconductor.
Las Marias: Please describe your main products – actuators. What makes them unique in the industry, and how do you position them to keep ahead of the competition?
Neff: Our devices are mechatronic – they perform work and feed back what happened. They are based on our proprietary moving coil designs. Like other devices they have programmable position and velocity modes. Unlike others they have the ability to find and then "soft land" on surfaces. They also have a force programmable mode. These are very useful in many applications. There are also SMAC invented unusual configurations such as LARs – independent linear and rotary axis units.
The company keeps ahead of the competition in many planned ways. First off, we follow a rule of thumb cost down approach that results in a 35% drop in price whenever we replace an old series with a new one. This happens every five years. We can achieve this because we do things like making our own encoders and developing very small and low-cost controllers. All key parts are manufactured in-house. We also periodically launch new R&D projects like our Robotic Finger – which winds up transferring new technology to our standard product line. The Finger enabled us to increase the force to package size ratio by 100% using the same current. That will show up commercially in our new LCB series. Better capabilities at a lower price.
Las Marias: Please discuss your patented Soft-Land technology. What is it, and what does it provide your customers?
Neff: Soft-Land is part of the patented mechatronic nature of our devices. We can, using any one of three different techniques, bump into a surface very softly and recognize the event. We are looking at one of the three control modes and monitoring changes that can only be caused by running into a surface – this is all done in milliseconds.
Las Marias: In which industry segments does this technology offer the biggest benefits?
Neff: Because we can also programmably change forces, we have a very useful tool. For example, in electronic assembly, different chips require different forces when placed and pressed onto circuit boards. We can do this very precisely and very quickly.
Another example is testing auto switches. We can map the force/distance relationship and even the hysterious loop of the switch. Our units are used to bevel glass, test touch screens, and deburr variable layered surfaces. The feature is quite useful in the assembly of forms for casting.
In packaging we can sort different size/weight products and not send them flying. There are thousands of different applications using these unique features.
Las Marias: Your linear rotary actuators used in OEM machines for PCB assembly feature a "fairly unusual" linear and rotary motion. Can you please elaborate this? What are its advantages?
Neff: The linear rotary actuators were first developed 17 years ago. The early applications were in electronic assembly. Here, parts are picked up and then orientated in theta. Parts often have connector pins that are slightly bent so slight rotations are rehired to insure correct contact on the board. Our rotary encoders, which are as small as 10mm in diameter, are high resolution – anywhere from 20K to 65K. So the ability to pick up, orientate, soft land, and press with a programmed force makes this operation easy to accomplish.
The LAR designs for electronic assembly are getting smaller and smaller. We have 13mm-wide units now out for sale and will be introducing an 8mm wide unit next year. These are aimed at the smaller and more fragile chips that continue to come out. Low-moving mass is critical in order to reduce impact.
Applications have spread into other industries. Larger LARs are widely used for automatic thread gauging in the automotive industry. In packaging, our patented devices are finding a great niche in capping – replacing cam systems.
Las Marias: At the recent Automate 2015 show, SMAC presented what is said to be the world's first direct drive servo motor robotic finger. Can you please describe this new technology, and why is it being considered a technological breakthrough?
Neff: First, robots seem to be stuck. There really hasn't been much change in the past 20 years. Part of the reason is that the robots are handicapped by the lack of dexterous hands. They only have grippers. I saw a very clever one introduced by SRI at the Chicago Robot Show, but it still is only a gripper.
The reason for that is there hasn't been a small powerful direct drive motor available. Geared motors are not a solution since the finger must be flexible, must have compliancy. The torque required at the knuckle the closest to your finger tip to apply 10N at the fingertip – like you can – must be 200mNm. And this needs to be at pretty low current, say under 750mA.
We have developed such a motor. By applying our basic technology and greatly improving what we had, we have developed a motor that puts out 150mNm at 1.5A and is about 1.5 times the size of your knuckle. We are in the midst of the next iteration, which will drop the size down to that of a human. Basically we came up with four improvements that upped our flux density by four times. All new – and all resulted in patent applications.
Because of this, we can duplicate what the human finger – and eventually the hand – can do. This motor design is the breakthrough. And it will lead to very useful robotic hands.
Page 1 of 2
Suggested Items
Choosing the Right Component to Reduce Cycle Times
10/19/2015 | Stephen Las Marias, I-Connect007SMAC Moving Coil Actuators president Edward Neff talks with I-Connect007's Stephen Las Marias about the strategies they implement in their production lines to reduce cycle times and go to market faster. He also talks about how using proven components can help manufacturers ensure the uptime of their equipment and processes.