-
-
News
News Highlights
- Books
Featured Books
- smt007 Magazine
Latest Issues
Current IssueWhat's Your Sweet Spot?
Are you in a niche that’s growing or shrinking? Is it time to reassess and refocus? We spotlight companies thriving by redefining or reinforcing their niche. What are their insights?
Moving Forward With Confidence
In this issue, we focus on sales and quoting, workforce training, new IPC leadership in the U.S. and Canada, the effects of tariffs, CFX standards, and much more—all designed to provide perspective as you move through the cloud bank of today's shifting economic market.
Intelligent Test and Inspection
Are you ready to explore the cutting-edge advancements shaping the electronics manufacturing industry? The May 2025 issue of SMT007 Magazine is packed with insights, innovations, and expert perspectives that you won’t want to miss.
- Articles
- Columns
- Links
- Media kit
||| MENU - smt007 Magazine
Selecting a Reflow Oven, Part 1
August 10, 2015 | Robert Voigt, DDM NovastarEstimated reading time: 1 minute
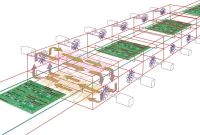
A reflow oven is simply any device that can liquefy solder in a controlled way to produce an electrical conductive bond between the component and its host (the board). There are several different methods to do this, not all of which can literally be called ovens. For instance, the simplest form of heating is performed by conduction, that is, by contact with a heated surface such as a hot plate. Other heating methods typically performed within a chamber (oven) but that rely on different heating methods include:
- Convection: Boards with their assembled components are passed through heated, circulating air from a conventional electrical heat source.
- Infrared (IR): Boards are passed inside a chamber over a direct IR heat source.
- Vapor Phase: Vapor is generated by heating a fluid with a specific boiling point (240°C) and transfers heat to the circuit board just above the melting point of the solder.
Let's begin with a commonly asked question: What size oven do I need? The answer is also a question: How many zones can you afford?
It seems like an odd way to start a discussion about reflow ovens, but it's not entirely unreasonable. As with any complex process, there will be tradeoffs between cost and capabilities, and more zones will always give you better flexibility and more control over your profile—but at a cost. The decision has to be qualified primarily on your anticipated throughput; that is, how many boards you process in a day or a week.
There are other considerations too, such as board size, component density, and appropriate thermal technology, but we’ll talk about those (and more) after identifying the work-flow volume.
A typical soldering operation in today's world requires three main stages for temperature profiling: preheat, soak (activate), and reflow, which perform these functions: 1) The preheat stage for a certain period of time to activation temperature; 2) the soak stage for a different period of time to activate the solder; and 3) the reflow stage where temperatures peak for yet a different time frame. After this, the board is typically cooled and removed. Depending on the material, e.g., leaded, lead-free or specialty materials such as epoxies, the heating profile for each stage will vary according to the manufacturer’s specifications to achieve optimal bonding.
Editor's Note: This article originally appeared in the August 2015 issue of SMT Magazine.
Suggested Items
Silicon Mountain Contract Services Enhances SMT Capabilities with New HELLER Reflow Oven
07/17/2025 | Silicon Mountain Contract ServicesSilicon Mountain Contract Services, a leading provider of custom electronics manufacturing solutions, is proud to announce a significant upgrade to its SMT production capability with the addition of a HELLER 2043 MK5 10‑zone reflow oven to its Nampa facility.
Knocking Down the Bone Pile: Addressing End-of-life Component Solderability Issues, Part 4
07/16/2025 | Nash Bell -- Column: Knocking Down the Bone PileIn 1983, the Department of Defense identified that over 40% of military electronic system failures in the field were electrical, with approximately 50% attributed to poor solder connections. Investigations revealed that plated finishes, typically nickel or tin, were porous and non-intermetallic.
SHENMAO Strengthens Semiconductor Capabilities with Acquisition of PMTC
07/10/2025 | SHENMAOSHENMAO America, Inc. has announced the acquisition of Profound Material Technology Co., Ltd. (PMTC), a premier Taiwan-based manufacturer of high-performance solder balls for semiconductor packaging.
KYZEN to Highlight Understencil and PCB Cleaners at SMTA Querétaro Expo and Tech Forum
07/09/2025 | KYZEN'KYZEN, the global leader in innovative environmentally responsible cleaning chemistries, will exhibit at the SMTA Querétaro Expo & Tech Forum, scheduled to take place Thursday, July 24, at Centro de Congresos y Teatro Metropolitano de Querétaro.
Driving Innovation: Direct Imaging vs. Conventional Exposure
07/01/2025 | Simon Khesin -- Column: Driving InnovationMy first camera used Kodak film. I even experimented with developing photos in the bathroom, though I usually dropped the film off at a Kodak center and received the prints two weeks later, only to discover that some images were out of focus or poorly framed. Today, every smartphone contains a high-quality camera capable of producing stunning images instantly.