-
- News
- Books
Featured Books
- design007 Magazine
Latest Issues
Current IssueProper Floor Planning
Floor planning decisions can make or break performance, manufacturability, and timelines. This month’s contributors weigh in with their best practices for proper floor planning and specific strategies to get it right.
Showing Some Constraint
A strong design constraint strategy carefully balances a wide range of electrical and manufacturing trade-offs. This month, we explore the key requirements, common challenges, and best practices behind building an effective constraint strategy.
All About That Route
Most designers favor manual routing, but today's interactive autorouters may be changing designers' minds by allowing users more direct control. In this issue, our expert contributors discuss a variety of manual and autorouting strategies.
- Articles
- Columns
- Links
- Media kit
||| MENU - design007 Magazine
Estimated reading time: 1 minute
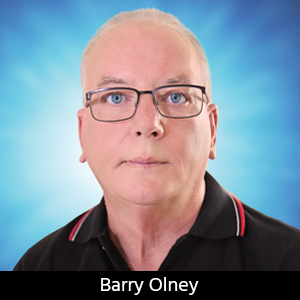
Beyond Design: Stackup Planning, Part 2
In Part 1 of the Stackup Planner series, I looked at how the stackup is built, the materials used in construction and the lamination process. And I set out some basic rules to follow for high-speed design. It is important keep return paths, crosstalk and EMI in mind during the design process. Part 2 follows on from this with definitions of basic stackups starting with four and six layers. Of course this methodology can be used for higher layer count boards—36, 72 layers and beyond.
Four-Layer Stackup
A four-layer board is probably not the most practical configuration for high-speed design. Although it does have the advantage, over double sided boards, of using planes for the distribution of power and ground and the planes also act as the return current path for signals. Microstrip traces tend to radiate emissions and this configuration should be avoided in preference to embedding the critical signals using a higher layer count configuration. On the other hand, if you intend mounting the four-layer board, completely shielded, in a metal box then this configuration may be acceptable.
Since all (most) stackups are symmetrical, then it is best to just work on just the top half of the stackup to begin with—this halves the construction time. Stackups are generally symmetrical, with even amounts of copper about the center, in order to prevent the board from warping during fabrication and during the reflow process. If one half has more copper, then it will cool at a slower rate thus warping the board.
The layer selection process is a follows:
- With four layers, two planes are placed in the center of the substrate. One ounce (1.4 mil) copper is typical for plane layers.
- Prepreg material separates the signal layers from the planes and this should be as thin as possible in order to achieve close coupling.
- Solder mask is generally added to the outer layers. This will reduce the impedance by a few ohms.
In Figure 1, the virtual materials yield a 54.44 ohm signal ended and 96.82 ohm differential impedance. This is close enough (to 50 ohms). Now let’s fine-tune this stackup by inserting real dielectric materials and then adjust the variables to get the desired impedance.
To read this entire article, which appeared in the July 2015 issue of The PCB Design Magazine, click here.
More Columns from Beyond Design
Beyond Design: Effective Floor Planning StrategiesBeyond Design: Refining Design Constraints
Beyond Design: The Metamorphosis of the PCB Router
Beyond Design: Radiation and Interference Coupling
Beyond Design: Key SI Considerations for High-speed PCB Design
Beyond Design: Electro-optical Circuit Boards
Beyond Design: AI-driven Inverse Stackup Optimization
Beyond Design: High-speed Rules of Thumb