-
- News
- Books
Featured Books
- design007 Magazine
Latest Issues
Current IssueAll About That Route
Most designers favor manual routing, but today's interactive autorouters may be changing designers' minds by allowing users more direct control. In this issue, our expert contributors discuss a variety of manual and autorouting strategies.
Creating the Ideal Data Package
Why is it so difficult to create the ideal data package? Many of these simple errors can be alleviated by paying attention to detail—and knowing what issues to look out for. So, this month, our experts weigh in on the best practices for creating the ideal design data package for your design.
Designing Through the Noise
Our experts discuss the constantly evolving world of RF design, including the many tradeoffs, material considerations, and design tips and techniques that designers and design engineers need to know to succeed in this high-frequency realm.
- Articles
- Columns
- Links
- Media kit
||| MENU - design007 Magazine
Karel Tavernier: The Gerber Guide
August 19, 2015 | Karel Tavernier, UcamcoEstimated reading time: 2 minutes
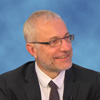
It is clearly possible to fabricate PCBs from the fabrication data sets currently being used—it's being done innumerable times every day all over the globe. But is it being done in an efficient, reliable, automated and standardized manner? At this moment in time, the honest answer is no, because there is plenty of room for improvement in the way in which PCB fabrication data is currently transferred from design to fabrication.
This is not about the format, which for over 90% of the world's PCB production is Gerber: There are very rarely problems with Gerber files themselves. They allow images to be transferred without a hitch. In fact, the Gerber format is part of the solution, given that it is the most reliable option in this field. The problems actually lie in which images are transferred, how the format is used and—more often—in how it is not used.
In this monthly column, Karel Tavernier explains in detail how to use the newly revised Gerber data format to communicate with your fabrication partners clearly and simply, using an unequivocal yet versatile language that enables you and them to get the very best out of your design data. Each month we will look at a different aspect of the design-to-fabrication data transfer process.
This column has been excerpted from the guide, PCB Fabrication Data: Design-to-Fabrication Data Transfer.
Chapter 1: How PCB Design Data is used by the Fabricator
In this first article of the series, we’ll be looking at what happens to the designer's data once it reaches the fabricator. This is not just a nice add-on, because for designers to construct truly valid PCB data sets, they must have a clear understanding of how their data is used. This, more than anything else, clarifies how it should be prepared.
We will not look at how to design PCBs for easy fabrication, which is completely outside the remit of the developer of the Gerber format and a matter for the PCB fabricators themselves.
What does a PCB fabricator do with CAD fabrication data?
PCBs are typically fabricated in about 22 steps, many of which are digitally controlled and require dedicated data modules called production tools.
Some designers believe that their PCB fabrication data will drive the fabricator's production machines directly; that the Gerber files will be used directly on the PCB fabricator's photoplotter; that Excellon drill files will go straight onto the fabricator's drilling machines; and that IPC-D-356A netlist will go right into electrical test machines.
Not so. Fabricators never use the Gerber or Excellon files directly on their equipment.
There are many reasons for this, the simplest of which is panelization. Even though the designer's data describes a single PCB or maybe an array, the job is never manufactured as such. It is always put on a production panel, which will typically have multiple jobs on it, as well as a border for plating, test coupons, etc.
To read this entire article, which appeared in the July 2015 issue of The PCB Design Magazine, click here.
Suggested Items
TTCI Joins Printed Circuit Engineering Association to Strengthen Design-to-Test Collaboration and Workforce Development
07/09/2025 | The Test Connection Inc.The Test Connection Inc. (TTCI), a leading provider of electronic test and manufacturing solutions, is proud to announce its membership in the Printed Circuit Engineering Association (PCEA), further expanding the company’s efforts to support cross-functional collaboration, industry standards, and technical education in the printed circuit design and manufacturing community.
Bell to Build X-Plane for Phase 2 of DARPA Speed and Runway Independent Technologies (SPRINT) X-Plane Program
07/09/2025 | Bell Textron Inc.Bell Textron Inc., a Textron Inc. company, has been down-selected for Phase 2 of Defense Advanced Research Projects Agency (DARPA) Speed and Runway Independent Technologies (SPRINT) X-Plane program with the objective to complete design, construction, ground testing and certification of an X-plane demonstrator.
Facing the Future: Time for Real Talk, Early and Often, Between Design and Fabrication
07/08/2025 | Prashant Patel -- Column: Facing the FutureThere has always been a subtle but significant divide between those who design and those who build printed circuit boards. It’s not a hostile gap, but it is a real one, and in today’s high-speed, high-complexity, high-stakes environment, that gap is costing us more than time and yield. It’s costing us innovation.
DownStream Acquisition Fits Siemens’ ‘Left-Shift’ Model
06/26/2025 | Andy Shaughnessy, I-Connect007I recently spoke to DownStream Technologies founder Joe Clark about the company’s acquisition by Siemens. We were later joined by A.J. Incorvaia, Siemens’ senior VP of electronic board systems. Joe discussed how he, Rick Almeida, and Ken Tepper launched the company in the months after 9/11 and how the acquisition came about. A.J. provides some background on the acquisition and explains why the companies’ tools are complementary.
Elementary Mr. Watson: Retro Routers vs. Modern Boards—The Silent Struggle on Your Screen
06/26/2025 | John Watson -- Column: Elementary, Mr. WatsonThere's a story about a young woman preparing a holiday ham. Before putting it in the pan, she cuts off the ends. When asked why, she shrugs and says, "That's how my mom always did it." She asks her mother, who gives the same answer. Eventually, the question reaches Grandma, who laughs and says, "Oh, I only cut the ends off because my pan was too small." This story is a powerful analogy for how many PCB designers approach routing today.