Addressing Quality and Manufacturability Challenges of Mission-Critical Products
August 21, 2015 | Amy Yin Chen, NaprotekEstimated reading time: 2 minutes
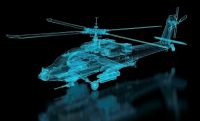
Typically, mission-critical military and aerospace printed circuit board assemblies (PCBAs) are based on 100% surface mount technology (SMT) and optimized for manufacturability from day one of design. The reality is that many of these products utilize mixed technology, either due to legacy designs or concerns about the interconnection strength of SMT connectors or other critical parts which may be subject to significant shock or vibration. Use of different soldering formulations can drive challenges in meeting cleanliness standards. In many cases, these mixed technology designs often violate industry-standard design guidelines, creating manufacturability issues.
From a contract manufacturing perspective, the first option is to make design for manufacturability (DfM) recommendations for changes to the design that would correct issues that are likely to drive production defects. This is not always a viable option, especially with legacy products or products that have gone through an extensive qualification process. Consequently, the best OEM-contract manufacturing relationships in this area focus not only on eliminating issues that drive defects before they happen, but also have the flexibility to deliver superior quality even when redesign isn’t possible. To better outline issues that should be closely watched in the design process, here are seven of the most common and potential options for addressing them:
Mismatched Footprints: PCB design library footprints don’t always match the specified component footprints, which can impact solderability on components with improperly sized pads. It can also contribute to additional defects when spacing among SMT and through-hole components is tight. Footprint accuracy should always be checked as part of the design review process.
If the design isn’t changed prior to prototyping, the appropriate approach is to manually place the parts and provide feedback to the customer on the issues. When the component is an integrated circuit, it is bonded pin 1 to pin 1. The preferred option is that the PCB be re-laid out or the bill of materials modified.
Failure to Provide Proper Spacing/Clearance for Through-Hole Components: Mixed technology, double-sided boards are often run on pallets through the wave solder in order to protect any bottom-side components that can’t be exposed to the wave. This issue can also make it difficult to use automated insertion equipment. Use of IPC design guidelines can help the design team to avoid this issue.
The recommended clearance for fixturing is 75 mils. However, as products shrink, many PCB designers are going to 35 mils.
Editor's Note: This article originally appeared in the August 2015 issue of SMT Magazine.
Testimonial
"Advertising in PCB007 Magazine has been a great way to showcase our bare board testers to the right audience. The I-Connect007 team makes the process smooth and professional. We’re proud to be featured in such a trusted publication."
Klaus Koziol - atgSuggested Items
ZESTRON Expands Capabilities with Addition of the EPS by i-Tech AG 75 Pallet Cleaning System
08/26/2025 | ZESTRONZESTRON, the global leader in high-precision cleaning solutions and services, is excited to announce the addition of a new capability in its Technical Center in Manassas, VA:
Pick and Place Machine Innovator - NECTEC Launches Next-Gen SMT Line Solution With LED and X-ray Technology
08/26/2025 | Globe NewswireNECTEC PTE. LTD., a leading provider of SMT electronics manufacturing equipment, announced the official launch of its next-generation SMT solutions, featuring newly upgraded pick and place machine, specialized LED pick and place machines, enhanced Reflow Oven technology, advanced X-ray Inspection, high-speed X-ray Counter, and premium Solder Paste
MS2 Technologies, LLC/P. Kay Focuses on Central America with First Installation in Honduras
08/24/2025 | P. Kay Metal, Inc.This year MS2 Technologies has turned their focused to the growing electronics market in Central America. With that focus came the adaptation of MS2 and the Akila System from a Honduras-based corporation with manufacturing plants in both Honduras and Mexico.
BEST Inc. Provides High-Reliability BGA Reballing and Component Rework Services
08/22/2025 | BEST Inc.BEST Inc., a leader in electronic component services, is pleased to announce its component rework services are available for all types of area array devices including ball grid array, land grid array and quad flat no-lead SMT packages.
Indium Corporation Promotes Two Leaders in EMEA (Europe, Middle East, and Africa) Markets
08/05/2025 | Indium CorporationWith its commitment to innovation and growth through employee development, Indium Corporation today announced the promotions of Andy Seager to Associate Director, Continental Sales (EMEA), and Karthik Vijay to Senior Technical Manager (EMEA). These advancements reflect their contributions to the company’s continued innovative efforts with customers across Europe, the Middle East, and Africa (EMEA).