-
-
News
News Highlights
- Books
Featured Books
- design007 Magazine
Latest Issues
Current IssueAll About That Route
Most designers favor manual routing, but today's interactive autorouters may be changing designers' minds by allowing users more direct control. In this issue, our expert contributors discuss a variety of manual and autorouting strategies.
Creating the Ideal Data Package
Why is it so difficult to create the ideal data package? Many of these simple errors can be alleviated by paying attention to detail—and knowing what issues to look out for. So, this month, our experts weigh in on the best practices for creating the ideal design data package for your design.
Designing Through the Noise
Our experts discuss the constantly evolving world of RF design, including the many tradeoffs, material considerations, and design tips and techniques that designers and design engineers need to know to succeed in this high-frequency realm.
- Articles
- Columns
- Links
- Media kit
||| MENU - design007 Magazine
Top Gear: PADS Professional Road Test
October 12, 2015 | Barry Olney, In-Circuit DesignEstimated reading time: 3 minutes
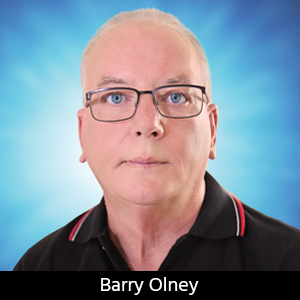
We hear all the hype about new EDA tools, but how do they actually perform on your design? This month, I road-test Mentor Graphics’ new PADS Professional and put it through a rigorous performance evaluation. Let’s see how the Xpedition technology actually performs when integrated into the PADS tool suite.
Opening the hood, we see an impressive line-up of features including signal and power integrity, thermal analysis and DRC support for traces violating split planes, reference plane changes and shielding. All the essentials for today’s complex high-speed designs! Plus, I am looking forward to trying the dynamic plane generation feature—regenerating copper pours is always a pain to perform, in any software. And of course, PADS Professional includes all the standard features one would expect in a high-end tool.
Based on Xpedition technology, PADS Professional is a major improvement over the previous PADS suite of tools. I was first impressed by this technology in 1994, when I attended the VeriBest PCB training and the sales kick-off in Boulder, Colorado. During the sessions, a few of the Intergraph Electronics sales guys were taken out back, into R&D, and were shown the latest routing technology—eyes lit up with dollar signs as the VeriBest (now Xpedition) router was put through its paces.
Meanwhile back in Australia, where I was responsible for Intergraph Electronics sales and support, customers were also suitably impressed. My first sale was six seats of VeriBest PCB with 20 seats of Design Capture to Fujitsu Australia, who had previously used Cadence. Both Cadence and Mentor presented their flagship products (Allegro and Board Station, respectively), but the VeriBest router was so impressive that the competition did not rate mentioning. Ron Oates, CAD manager of Fujitsu Australia at that time, stated in a press release, “VeriBest is light years ahead of the competitors.” And it is still arguably the best routing technology available today. Mentor went on to acquire VeriBest in 1999, as the lack of routing technology formed a fairly large hole in their PCB offerings. Needless to say, Mentor’s stock rose 9% after the acquisition was announced.
I won’t bore you with a full list of functionality or standard EDA tool features, but rather I will take you through, in detail, what I see as the outstanding features of PADS Professional.
PADS Professional utilizes xDX Designer as the front-end design entry tool. This schematic capture package was originally a ViewLogic Systems tools called ViewDraw, which became the unified front-end tool for all Mentor PCB products some years ago following an acquisition. Originally developed for creating hardware description language (HDL) function blocks for digital and mixed-signal systems, such as FPGAs and ASICs, it has a multitude of interfaces and is adaptable to many environments. In the PADS environment, it interfaces to the PCB (of course) but also allows FPGA I/O optimization, the integration of library tools, DxDatabook, and downstream digital and analog (EZWave) simulation tools.
But as far as I am concerned, the ability to launch HyperLynx LineSim at the schematic level is its best attribute. After selecting a net, the LineSim link loads the data from xDX Designer and exports it to HyperLynx to create a pre-layout free-form schematic view of the nets topology as in Figure 2. You can then simulate a sample of nets for, say, data, address, clocks and strobes to define the layout design rules. These rules are embedded in the schematic via the constraints manager, and they will then flow through to the layout database with forward annotation. Constraints are maintained through a common database that is consistent and in an easy-to-use spreadsheet interface. There is no need to learn an obscure program language to create complex constraints as in other tools.
To read this entire article, which appeared in the September 2015 issue of The PCB Design Magazine, click here.
Suggested Items
The Evolution of Picosecond Laser Drilling
06/19/2025 | Marcy LaRont, PCB007 MagazineIs it hard to imagine a single laser pulse reduced not only from nanoseconds to picoseconds in its pulse duration, but even to femtoseconds? Well, buckle up because it seems we are there. In this interview, Dr. Stefan Rung, technical director of laser machines at Schmoll Maschinen GmbH, traces the technology trajectory of the laser drill from the CO2 laser to cutting-edge picosecond and hybrid laser drilling systems, highlighting the benefits and limitations of each method, and demonstrating how laser innovations are shaping the future of PCB fabrication.
Day 2: More Cutting-edge Insights at the EIPC Summer Conference
06/18/2025 | Pete Starkey, I-Connect007The European Institute for the PCB Community (EIPC) summer conference took place this year in Edinburgh, Scotland, June 3-4. This is the third of three articles on the conference. The other two cover Day 1’s sessions and the opening keynote speech. Below is a recap of the second day’s sessions.
Day 1: Cutting Edge Insights at the EIPC Summer Conference
06/17/2025 | Pete Starkey, I-Connect007The European Institute for the PCB Community (EIPC) Summer Conference took place this year in Edinburgh, Scotland, June 3-4. This is the second of three articles on the conference. The other two cover the keynote speeches and Day 2 of the technical conference. Below is a recap of the first day’s sessions.
Preventing Surface Prep Defects and Ensuring Reliability
06/10/2025 | Marcy LaRont, PCB007 MagazineIn printed circuit board (PCB) fabrication, surface preparation is a critical process that ensures strong adhesion, reliable plating, and long-term product performance. Without proper surface treatment, manufacturers may encounter defects such as delamination, poor solder mask adhesion, and plating failures. This article examines key surface preparation techniques, common defects resulting from improper processes, and real-world case studies that illustrate best practices.
RF PCB Design Tips and Tricks
05/08/2025 | Cherie Litson, EPTAC MIT CID/CID+There are many great books, videos, and information online about designing PCBs for RF circuits. A few of my favorite RF sources are Hans Rosenberg, Stephen Chavez, and Rick Hartley, but there are many more. These PCB design engineers have a very good perspective on what it takes to take an RF design from schematic concept to PCB layout.